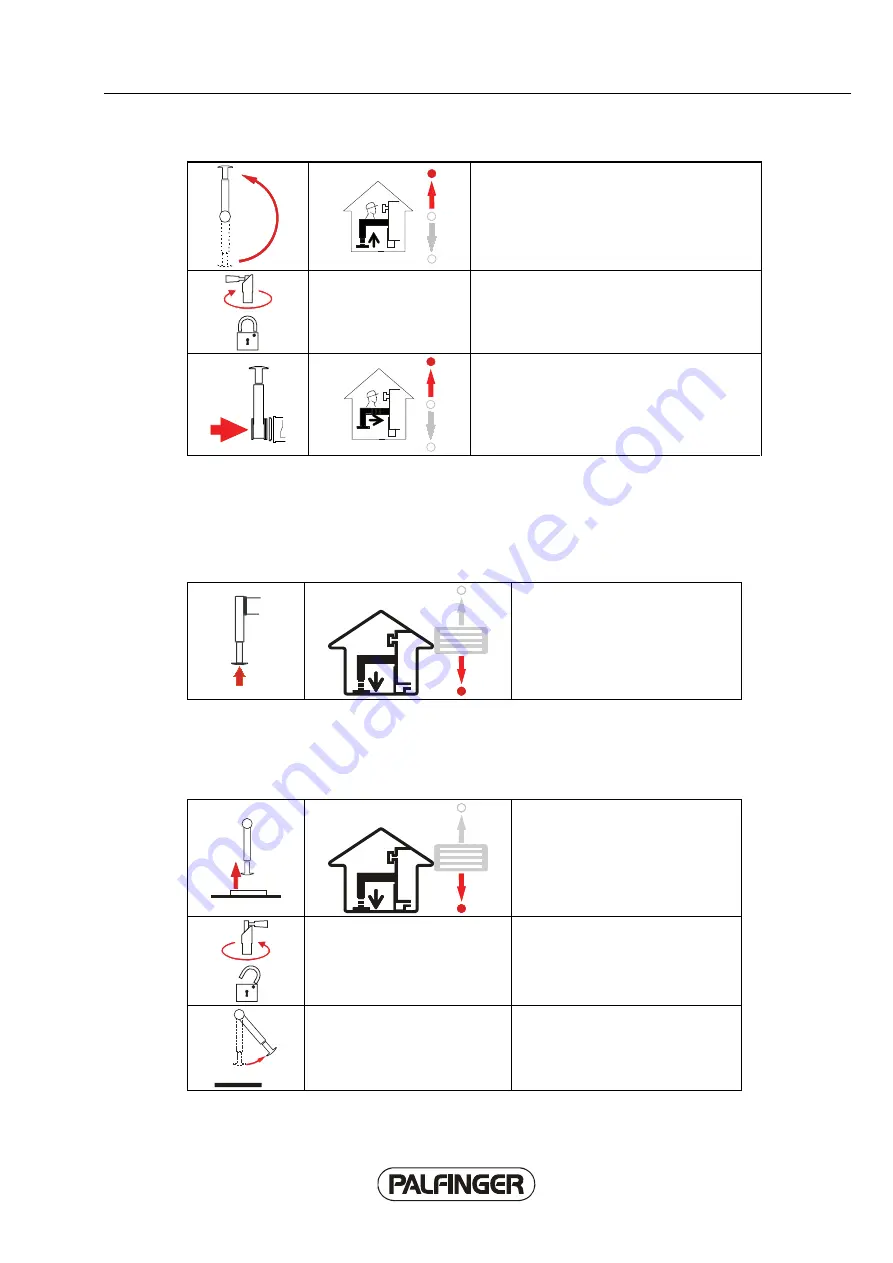
Chapter 9 Ending operation
211
Operate the function ‘Retract stabilizer
cylinder’ and tilt the cylinder up carefully and
slowly.
Close latch lever and make sure it is in the
locked position.
Retract the outrigger beams completely.
Stow supporting pads away in the correct way.
Retracting rigid stabilizer cylinders via radio remote control
Retract the stabilizer cylinders
completely.
Retracting manually tiltable stabilizer cylinders via radio remote control
Retract the tiltable stabilizer cylinders in transport position:
Retract the stabilizer cylinders
completely.
Open latch lever of stabilizer
cylinder.
Pivot stabilizer cylinder into transport
position.
Summary of Contents for PK 34002-SH P7
Page 1: ......
Page 2: ......
Page 4: ......
Page 8: ......
Page 12: ......
Page 14: ......
Page 24: ......
Page 26: ......
Page 30: ......
Page 66: ...Device and function 60 Overview of labels...
Page 76: ......
Page 78: ......
Page 128: ......
Page 158: ......
Page 182: ......
Page 184: ......
Page 208: ......
Page 210: ......
Page 222: ......
Page 224: ......
Page 242: ......
Page 252: ......
Page 254: ......
Page 258: ......
Page 259: ...Chapter 13 253 C H A P T E R 1 3 Technical description...
Page 260: ...254...