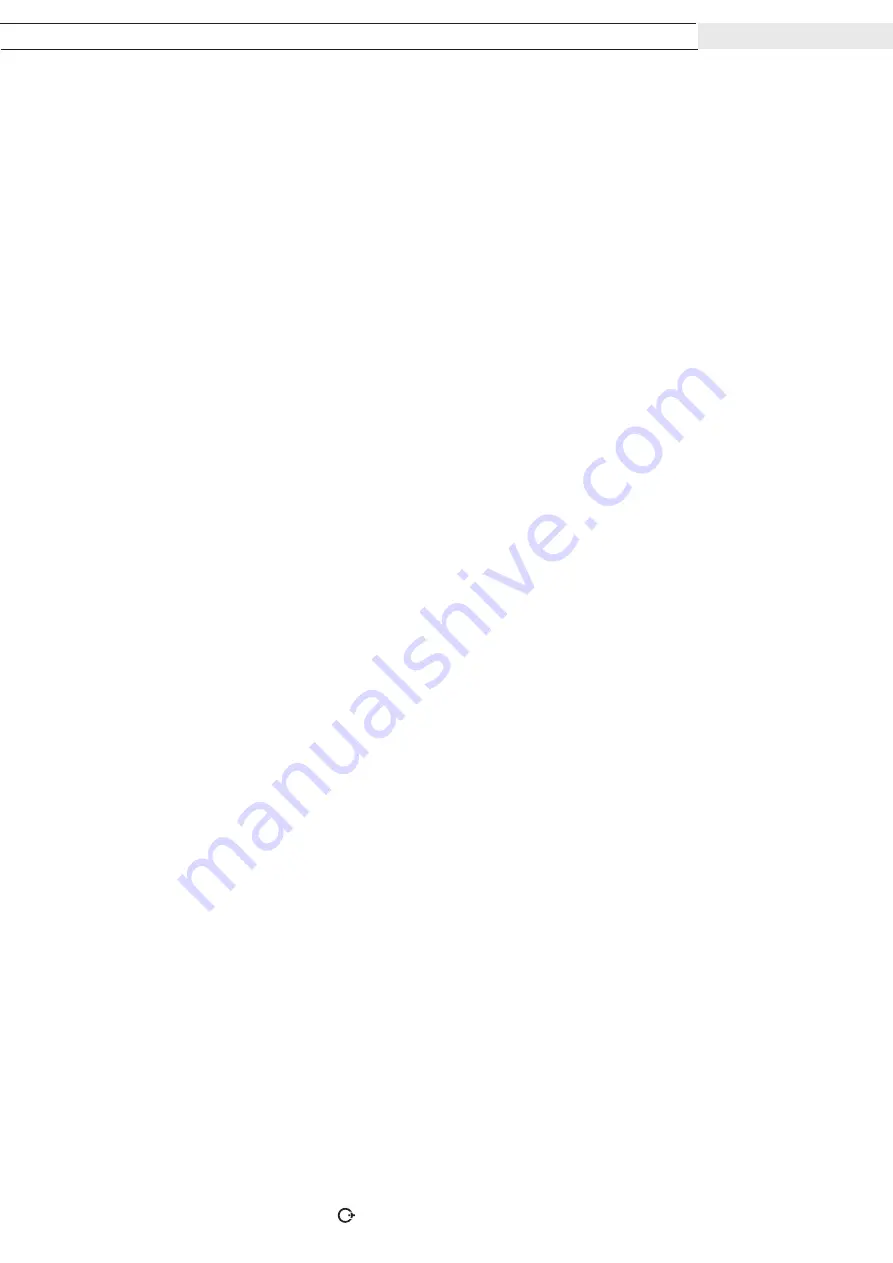
(14.01.21) OW_ORBIMAT_300SW_BA_852060202_00_EN
ORBITALUM TOOLS GMBH
,
D-78224 SINGEN, WWW.ORBITALUM.COM, PHONE +49 (0) 77 31 792-0 117
ORBIMAT 300 SW
EnGLISH
With other weld heads, the input fields are grayed-out.
Wire feed parameters:
• Wire start delay (in seconds)
• Wire final delay time (in seconds)
• Wire retract (in seconds)
• Wire HP speed (in mm/min)
• Wire LP speed (in mm/min)
Changing the wire feed quantity requires a change to the current, since more (cold) material is introduced to the weld-
ing process with an increased wire speed, for example. If the wire quantity is too high, it is difficult to control the melt
pool in the individual positions or it breaks away or drips off.
Wire start delay: The time from ignition of the arc to the introduction of the wire feed. The time corresponds with the
time for pool formation (start delay for the rotation motor). It cannot be longer than the pool formation time.
In special cases, it can be shorter than the bath formation time, so that the wire enters the melt pool while the rotation
motor is still not moving.
X
Do not set wire start delay too short, as the wire is not "taken up" if the melt pool has not yet been formed.
Wire final delay time: Time during which the wire is still fed to the process during current slope-off at the end of weld-
ing. Its minimum value is 0 and maximum value is as long as the current slope-off. With a value of 0, the wire feed stops
when the current slope-off begins. If the time corresponds to the duration of the current slope-off, wire continues to be
fed during the entire slope-off time.
Since the introduced energy declines as the current slopes off, the wire feed should stop when there is no longer a melt
pool.
Wire retract: Time during which the wire running direction is reversed at the end of the wire feed so that the wire
does not rest on the pipe when turning back the weld head. The retraction time should be approx. 1 - 2 sec. and is set
properly when the wire extends 2 - 3 mm from the feed tube after retraction. If the time is too long, the wire is pulled in
completely and the end (which is usually still a liquid ball) can adhere to the wire feed tube.
Wire HP/LP speed: The wire feed speeds of the filler wire (in mm/min) in the individual sectors. Auto programming usually
controls the wire in sync with the pulse: The wire feed motor does not move on the low pulse, as the energy of the arc
may not be sufficient to melt the wire under certain circumstances here.
To achieve a higher deposition rate:
X
Increase the speed of the wire in the high-pulse phase.
– or –
X
Feed wire in the low-pulse phase as well. The weld current set for low pulse must be sufficient here.
1. In the main menu, select "
Manual/Adjust programming
" > "
Adjust parameters
" > "
Pool formation
".
2. Consecutively select, highlight, adjust and save the "
Wire start delay
", "
Wire final delay time
" and "
Wire retract
"
parameters.
3. Select "
go forward to sector 1
" or select the desired sector.
The respective selected sector is highlighted in color to the right in the display. The angular degrees of this sector is
specified. An image of the seam scale appears below the process graphic.
4. Select, highlight, adjust and save the "
Wire HP speed
" and "
Wire LP speed
" parameters.
5. Press softkey 1 ("
Weld
") or softkey 2 ("
Test
").
The machine is ready to start.