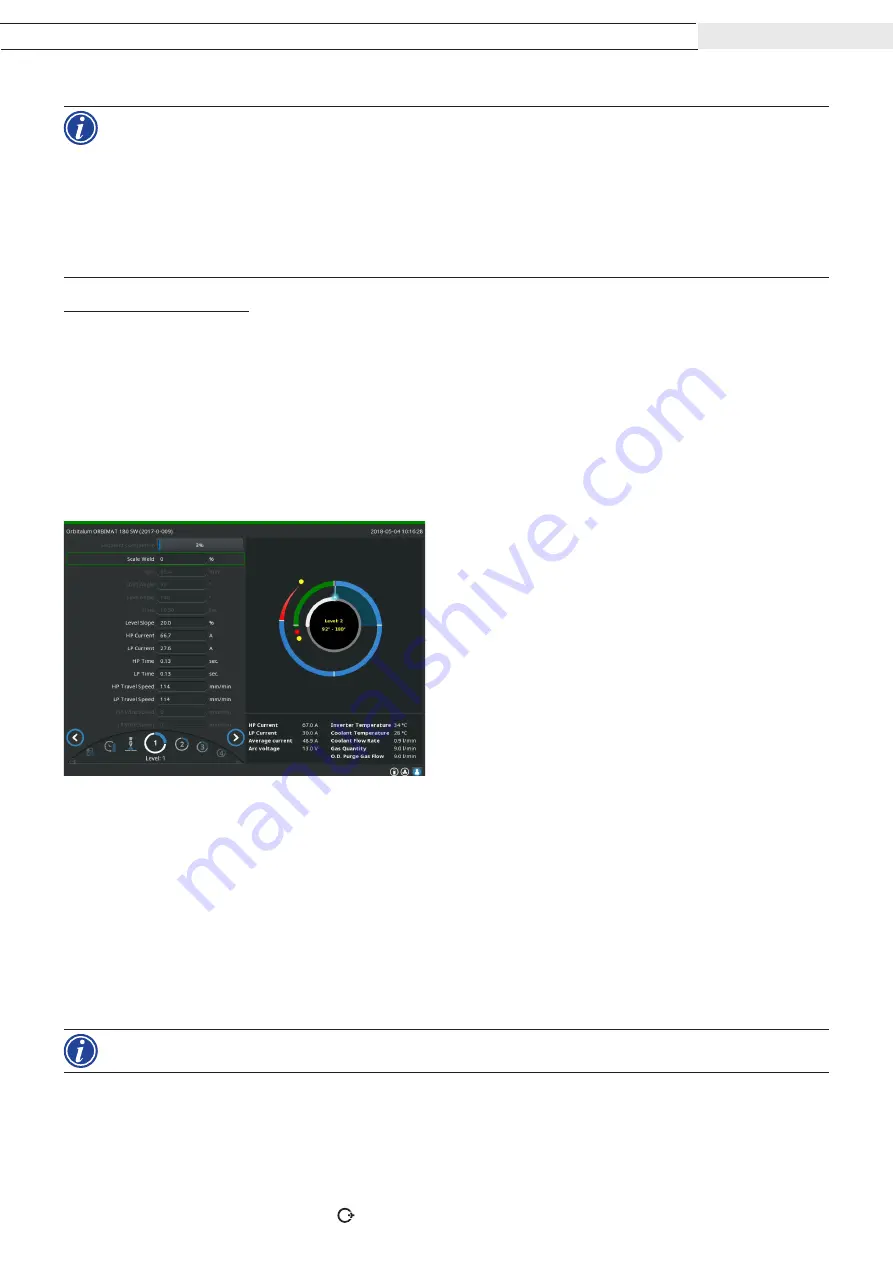
(14.01.21) OW_ORBIMAT_300SW_BA_852060202_00_EN
ORBITALUM TOOLS GMBH
,
D-78224 SINGEN, WWW.ORBITALUM.COM, PHONE +49 (0) 77 31 792-0 109
ORBIMAT 300 SW
EnGLISH
X
Observe the welding process continuously and be prepared to take action at any time.
X
With open weld tongs: Ensure proper guidance of the hose assembly while the rotor is circling.
Possible problems with the welding process:
• Incorrectly set weld current.
• LP weld tong not tensioned tightly enough.
• Forming gas quantity too high, holes being formed.
X
In these cases, interrupt the welding process (siehe Kap. 8.2.6, Seite 110).
Welding process – Sequence
The machine carries out the welding process completely. During the welding process, the machine monitors the welding
process and the following parameters:
• Coolant flow rate: The welding process is stopped if the limit value of 0.8 l/min is undershot.
• Gas flow: The welding process is interrupted if approximately 3 l/min is undershot.
• The weld current, weld voltage and weld speed process parameters: Limit values specified in the procedure are
taken into account.
The following details appear in the display during the running welding process:
Process completion: Bar graph with specification of pro-
cess completion (in %) for the respective current sector.
Correction factor: Percent value by which the current in
the current process was changed in comparison to the
saved procedure.
Parameters pipe diameter to wire LP speed: Display of
the process parameters of the procedure. The values can
be changed during the welding process. The changes
are saved by pressing the rotary knob (keyboard: ENTER)
to the current welding process. The changes are not yet
saved in the procedure. Fields with a gray background
cannot be edited.
Abb. 8:
Display during running welding process
Graphic: Display of the weld sequence. After starting up, a pointer pointing to the inner yellow dot appears during gas
pre purge. After the gas pre purge, pool formation occurs (the time after ignition during which no rotational movements
are occurring for buildup of the weld pool). In the individual sectors, the respective current sector is highlighted in
white, and the accompanying red indicator indicates the current electrode position. The current sector number and cur-
rent position (in angular degrees) appear in the bottom section of the graphic.
Info field: The following information appears in the info field (below the graphic): Name of the folder in which the proce-
dure is saved, name of the running procedure, current measurement values for coolant flow (in l/min), coolant tempera-
ture and inverter temperature (in °C); gas flow, mean current, arc voltage.
Warning messages and error messages appear in the "Warning" field.
The info field only appears during a running welding process.
Other: The following information appears on the two bottom lines: Help texts for operation with the rotary knob. On
the right, information on the activated printer and the USB stick. When the printer is activated (for example log printing
after welding) or the storage medium is activated (procedure being loaded), the symbols are highlighted in blue.