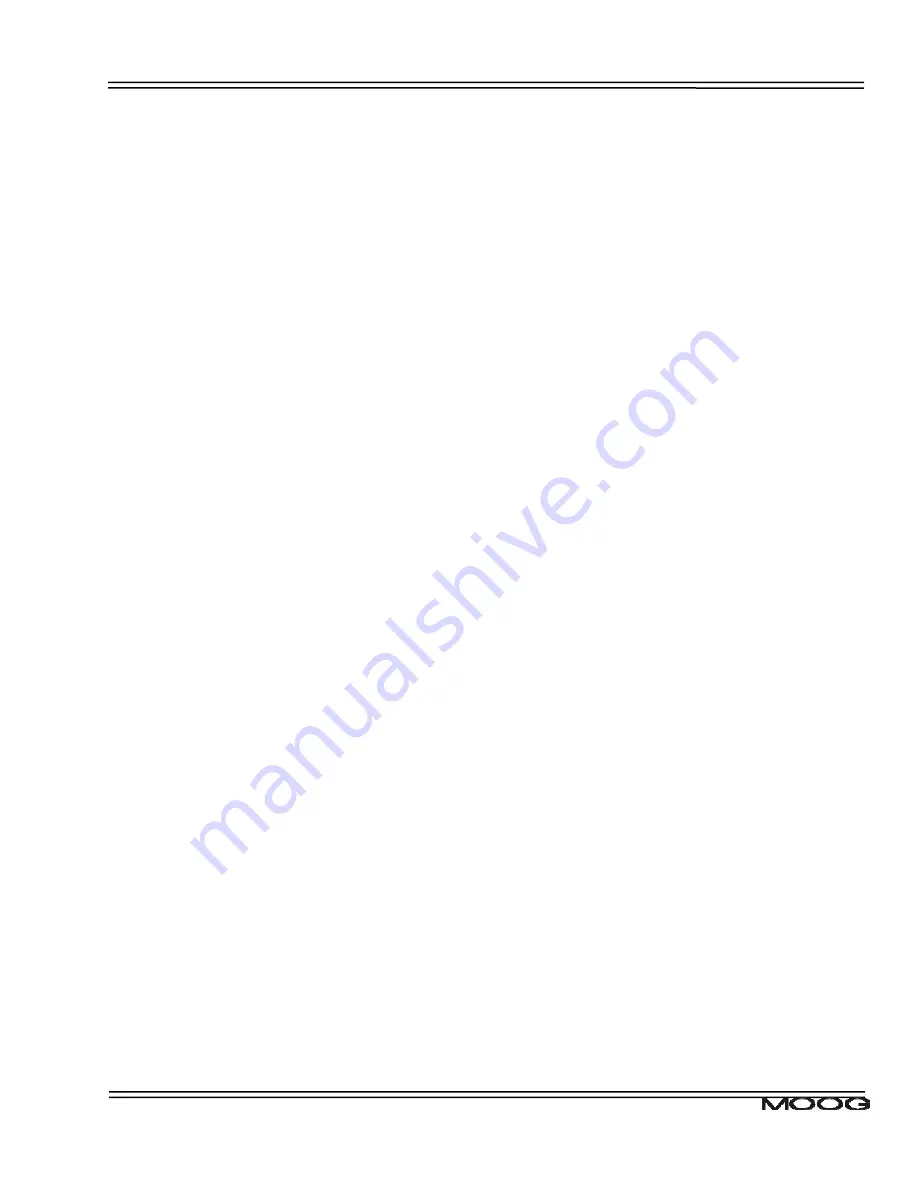
APPENDIX B – GUI
B-60
CDS7324 (FORMERLY LSF-0819)
Rev. A
INSTALLATION & USER’S MANUAL
B.2.16.70.3 Channel
Panels
Status
: Sets the channel to visible, hidden, or off.
Source
: Represents which parameter is logged.
Scaling
: Represents the vertical scaling for this channel.
Offset
: Represents the vertical offset for this channel.
B.2.16.70.4 Cursor
Panel
Allows 2 cursors to measure on the vertical axis, horizontal axis or a combination of both.
Also automatically displays the difference between the cursors in time and frequency.
B.2.16.70.5 Trigger
Panel
•
Status
: Displays the current status of the oscilloscope. This can be one of the following:
o
Stopped: The oscilloscope is currently not logging any data.
o
Waiting: The oscilloscope is currently waiting for the trigger to fire.
o
Sampling: The oscilloscope is currently sampling.
•
Source
: Represents the parameter which is used for triggering.
•
Level
: The value at which the trigger will fire.
•
Delay
: Allows setting of trigger delay or pre-trigger.
•
Coupling
: Coupling can be dc, ac, or bitmap masking.
•
Slope
: Determines whether to trigger on a rising or falling slope.
•
Mode
: Can be set by the user. This can be one of the following:
o
Continuous: The oscilloscope will sample from firing of trigger continuously.
o
Single: The oscilloscope will sample from firing of trigger for number of samples.
o
Roll: The oscilloscope will sample continuously (ignoring trigger settings).
o
Stop: The oscilloscope will stop sampling.