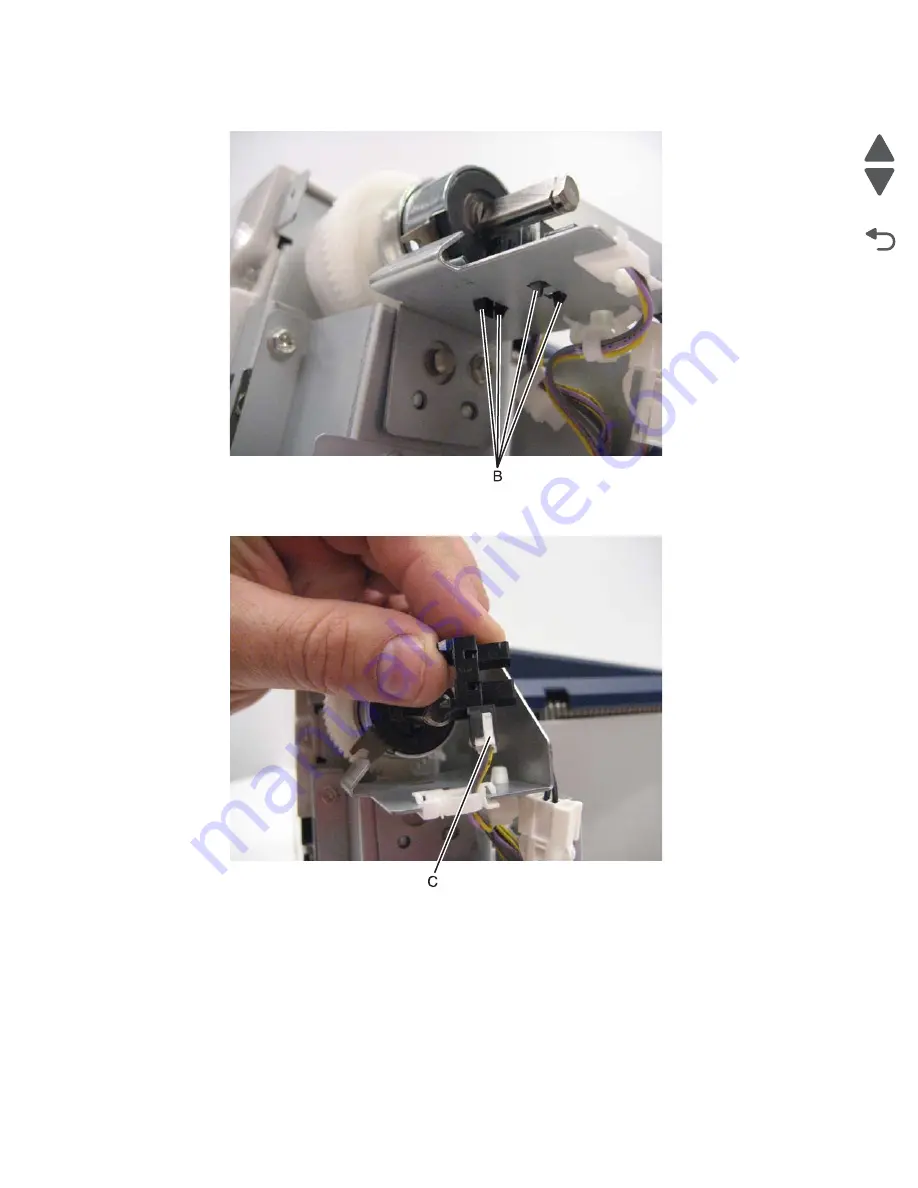
4-322
Service Manual
7558-
xxx
Go Back
Previous
Next
5.
Release the hooks (B) securing the sensor (decurler cam HP) to the machine.
6.
Remove the sensor (decurler cam HP).
7.
Disconnect the cable (C).
Sensor (decurler cover interlock) removal
1.
Remove the bridge unit assembly. See
“Bridge unit assembly removal” on page 4-308
.
2.
Remove the bridge decurler top cover. See
“Bridge decurler top cover removal” on page 4-305
.
Summary of Contents for X95 series
Page 26: ...xxvi Service Manual 7558 xxx Go Back Previous Next ...
Page 34: ...xxxiv Service Manual 7558 xxx Go Back Previous Next ...
Page 52: ...1 18 Service Manual 7558 xxx Go Back Previous Next ...
Page 464: ...3 112 Service Manual 7558 xxx Go Back Previous Next TTM theory of operations ...
Page 471: ...Diagnostic aids 3 119 7558 xxx Go Back Previous Next 3TM theory of operations ...
Page 477: ...Diagnostic aids 3 125 7558 xxx Go Back Previous Next 1TM theory of operations ...
Page 494: ...3 142 Service Manual 7558 xxx Go Back Previous Next ...
Page 506: ...4 12 Service Manual 7558 xxx Go Back Previous Next 6 Remove the operator panel top cover ...
Page 512: ...4 18 Service Manual 7558 xxx Go Back Previous Next 5 Remove the rear lower cover ...
Page 619: ...Repair information 4 125 7558 xxx Go Back Previous Next 4 Detach the media feed lift motor ...
Page 704: ...4 210 Service Manual 7558 xxx Go Back Previous Next 8 Remove the LED ...
Page 730: ...4 236 Service Manual 7558 xxx Go Back Previous Next 14 Remove the flatbed scanner assembly ...
Page 1038: ...6 12 Service Manual 7558 xxx Go Back Previous Next ...
Page 1076: ...7 38 Service Manual 7558 xxx Go Back Previous Next Assembly 37 TTM media feed 2 ...
Page 1112: ...7 74 Service Manual 7558 xxx Go Back Previous Next Assembly 71 Finisher punch 8 4 3 10 11 ...
Page 1158: ...7 120 Service Manual 7558 xxx Go Back Previous Next ...
Page 1168: ...I 10 Service Manual 7558 xxx Go Back Previous Next ...