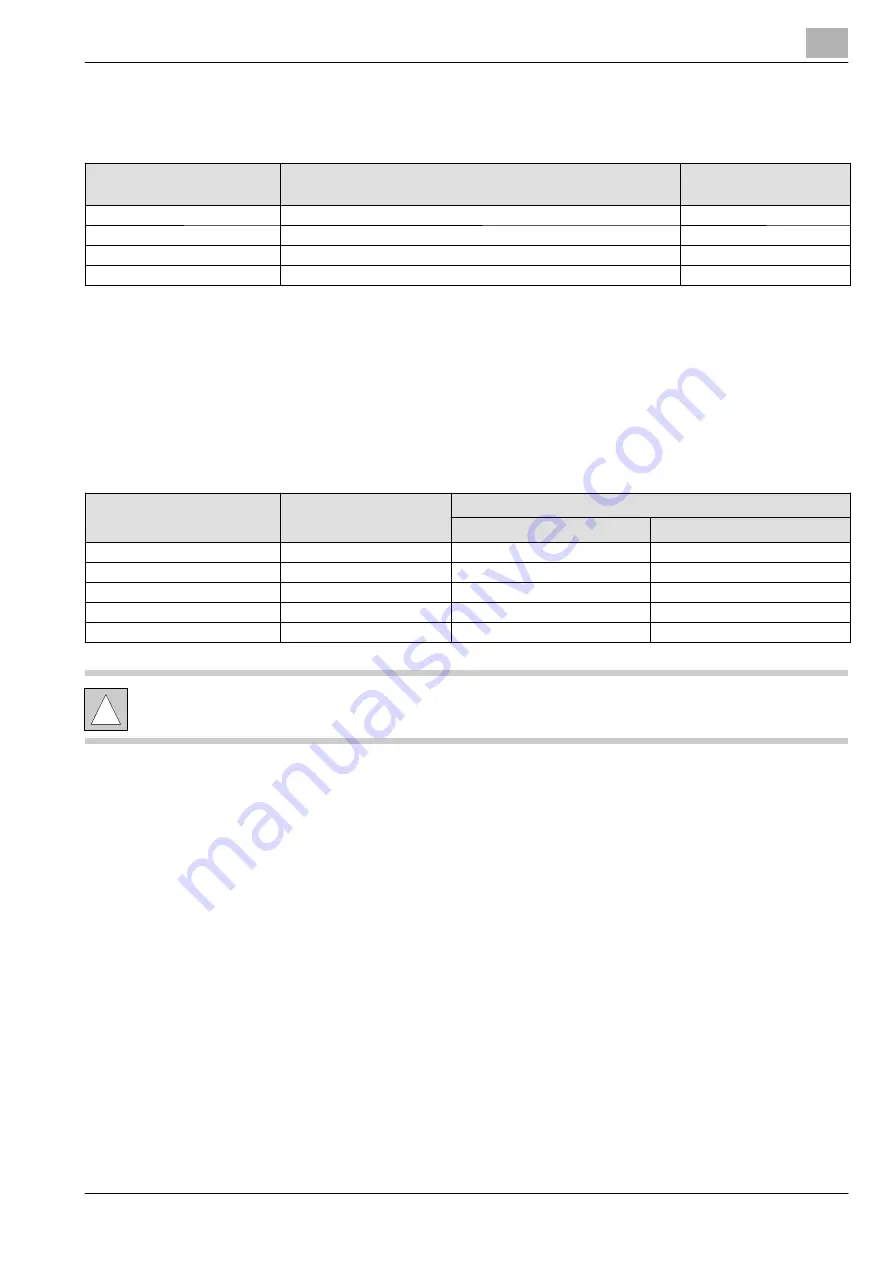
CHASSIS MODIFICATIONS
2-19
D
AILY
Printed 603.95.241
Base — 02/2012
Modification of the wheelbase
Table 2.10 - Maximum permitted wheelbase elongation
Model
Front suspension
Maximum wheelbase
(mm)
29L, 35S
Transverse
4100
35C, 40C, 45C, 50C
Transverse (maximum permitted 1800 kg)
4100
35C, 40C, 45C, 50C
Torsion bar (maximum permitted 1900 kg)
4750
60C, 65C, 70C
Torsion bar
4750
2.4.4
Influence on braking
In general, shortening the wheelbase has a negative influence on braking characteristics.
Table 2.11 shows the limits for wheelbase modification. Check with the IVECO - Homologation & Technical Application department
about the conditions (brake cylinders, minimum tares, technically permissible weights, tyres, height of the centre of gravity) with
which these values are permitted.
Table 2.11 - Braking, limits for wheelbase modification
Model
Version
Wheelbase
Minimum (mm)
Maximum (mm)
29L, 35S
Truck, van
3000
3950
35C, 40C
Truck, van
3000
4100
45C, 50C
Van
3000
4750
45C, 50C
Truck
3450
4750
60C, 65C, 70C
Truck, van
3300
4750
!
In the case of vehicles equipped with an ASR system, the setting data must be updated.
2.4.5
Procedure
To obtain a good result, proceed as follows:
-
position the vehicle so that the chassis is perfectly flat, using suitable stands;
-
disconnect the propeller shafts, the brake system pipes, wiring and anything else that could prevent the work from being
performed correctly;
-
identify the reference points on the chassis (e.g. pilot holes, suspension mounts);
-
mark the reference points with a light punching line on the upper wings of both side members, after checking that the connecting
one is perfectly perpendicular to the vehicle’s longitudinal axis;
-
if moving the suspension mounts, identify the new position using the previously determined references;
-
check that the new dimensions are identical on the left and right sides; the diagonal check, for minimum lengths of 1500 mm,
must not detect deviations greater than 2 mm;
-
make the new drill holes using the mounts and cross member plates as a mask if other equipment is not available;
-
fasten the mounts and the cross members using rivets or screws; if screws are used, ream the holes and use calibrated screws,
class 10.9, with nuts with loosening prevention systems; if their dimensions permit it, flanged head screws and nuts can be used;
-
if cutting the chassis (to be carried out according to the instructions on page 2-11, point b) determine a second line of reference
points so that the area to be worked on is contained between these and the previous ones (ensure a minimum distance of 1500
mm after the operation is complete). Move the points relative to the cutting area inside the two lines of reference, proceeding
according to the instructions in paragraph 2.2.3;
Summary of Contents for DAILY M.Y. 2012
Page 1: ...DAILY M Y 2012 BODYBUILDERS INSTRUCTIONS L I G H T R A N G E ISSUE 2012 ...
Page 4: ...Base 02 2012 Printed 603 95 241 Update data ...
Page 8: ...Index of section Base 02 2012 Printed 603 95 241 ...
Page 10: ...1 2 GENERAL SPECIFICATIONS DAILY Base 02 2012 Printed 603 95 241 Index ...
Page 26: ...1 18 GENERAL SPECIFICATIONS DAILY Base 02 2012 Printed 603 95 241 Convention ...
Page 30: ...2 4 CHASSIS MODIFICATIONS DAILY Base 02 2012 Printed 603 95 241 Index ...
Page 98: ...2 72 CHASSIS MODIFICATIONS DAILY Base 02 2012 Printed 603 95 241 Chocks ...
Page 140: ...4 2 POWER TAKE OFFS DAILY Base 02 2012 Printed 603 95 241 Index ...
Page 214: ...A 2 APPENDIX A DAILY PASSENGER TRANSPORT DAILY Base 02 2012 Printed 603 95 241 Index ...