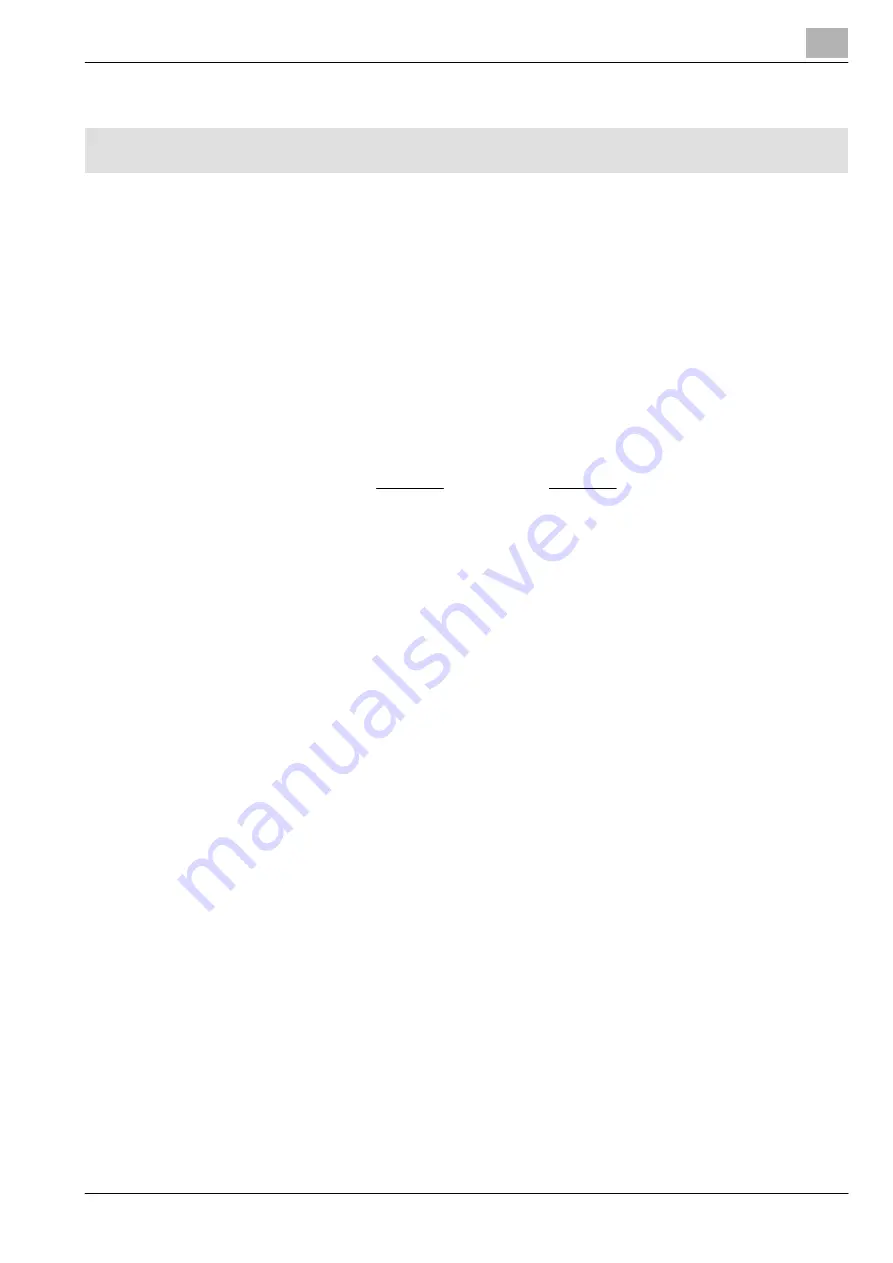
POWER TAKE OFFS
4-3
D
AILY
Printed 603.95.241
Base - 02/2012
General specifications
44444.
General specifications
4.1
General specifications
Different types of Power Take Offs (PTO) for motion withdrawal can be mounted to control of the ancillary control units.
According to the type of use and the performances required, the application can be performed as follows:
-
the gearbox;
-
transmission;
-
the front of the engine.
The characteristics and performances are given in the paragraphs which follow and in the relevant documentation which will be
supplied upon request.
For the definition of the power necessary for the apparatus to be controlled, particularly when the values requested are high, the
absorbed power should also be considered during the drive transmission phase (5 to 10% for the mechanical transmissions, belts
and gears, and greater values for the hydraulic controls).
Choose the Power Take Off transmission ratio to ensure that power uptake occurs within the flexible engine operating range; avoid
low speeds (lower than 1000 rpm) to rule out unevenness and jerkiness in vehicle operation.
The power taken in relation to the number of revolutions of the Power Take Off at the required torque.
P(PS)
=
M
⋅
n
⋅
i
7023
P(kW)
=
M
⋅
n
⋅
i
9550
P = Useable power
M = Torque permitted for the Power Take Off (Nm)
n = Power Take Off rpm.
i = Transmission ratio = PTO output rpm/ engine rpm
Type of use
Applications may be sporadic or continuous.
In sporadic applications, the duration of Power Take Off operations does not exceed 30 minutes.
In continuous use this is significantly longer; however whenever the use is comparable to that of a stationary engine, it is necessary
to evaluate the opportunity to reduce take off of torque also on the basis of the surrounding conditions (engine cooling, gearbox
etc.).
Take off of torque is possible without problems if the type of use does not result in significant variations of torque in terms of
frequency and amplitude.
Should this not be the case (e.g. hydraulic pumps, compressors), clutches or safety valves may be necessary to avoid overloading.
Summary of Contents for DAILY M.Y. 2012
Page 1: ...DAILY M Y 2012 BODYBUILDERS INSTRUCTIONS L I G H T R A N G E ISSUE 2012 ...
Page 4: ...Base 02 2012 Printed 603 95 241 Update data ...
Page 8: ...Index of section Base 02 2012 Printed 603 95 241 ...
Page 10: ...1 2 GENERAL SPECIFICATIONS DAILY Base 02 2012 Printed 603 95 241 Index ...
Page 26: ...1 18 GENERAL SPECIFICATIONS DAILY Base 02 2012 Printed 603 95 241 Convention ...
Page 30: ...2 4 CHASSIS MODIFICATIONS DAILY Base 02 2012 Printed 603 95 241 Index ...
Page 98: ...2 72 CHASSIS MODIFICATIONS DAILY Base 02 2012 Printed 603 95 241 Chocks ...
Page 140: ...4 2 POWER TAKE OFFS DAILY Base 02 2012 Printed 603 95 241 Index ...
Page 214: ...A 2 APPENDIX A DAILY PASSENGER TRANSPORT DAILY Base 02 2012 Printed 603 95 241 Index ...