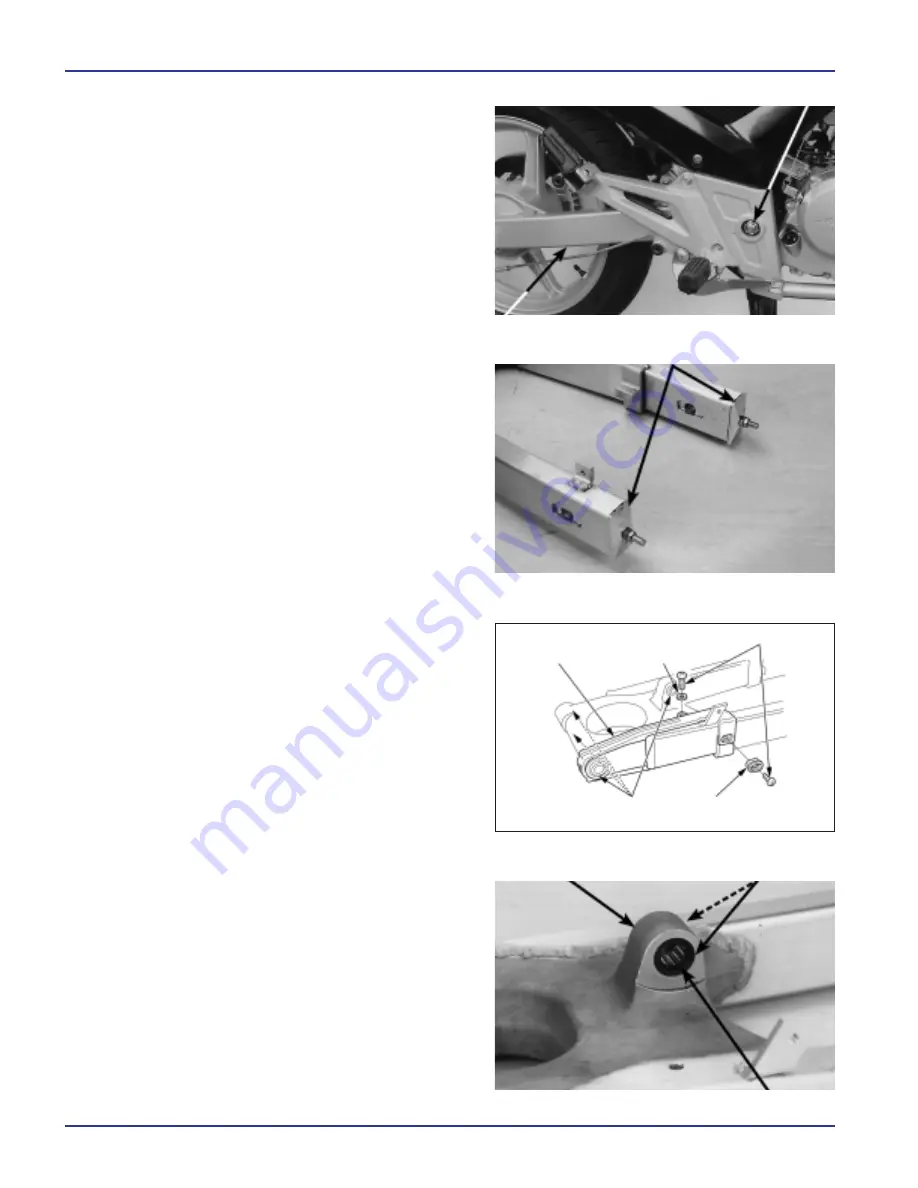
REAR WHEEL/BRAKE/SUSPENSION
14-14
SWING ARM
DISMANTLING
Remove the following components: Silencer (page 2-5)
Rear wheel (page 14-3)
Bolt and nut lower damper (page 14-12)
Remove the nut pivot swing arm.
From the left side, remove the bolt pivot and swing arm.
DISMANTLED
Inspect the guide to the drive chain with regard to
wear or damage.
Remove the adjusters in the drive chain.
SWING ARM
BOLT/NUT PIVOT
Remove the two screws, the spacer of the guide and the
guide to the drive chain.
Remove the spacers of pivots swing arm.
Remove the coveralls and the bearing of needles of the
articulation of the damper.
BALL NEEDLES
ARTICULATION OF
THE DAMPER
DUST COVERS
ADJUSTERS IN THE DRIVE CHAIN
CBX250
CHAIN
GUIDE
WASHER
BOLTS
SPACERS joints
SPACER OF
THE GUIDE
Summary of Contents for 2010 CBF 250
Page 1: ...WORKSHOP MANUAL...
Page 33: ...Chassis FAIRING EXHAUST SYSTEM 2 6 CBX250 NOTES...
Page 58: ...MAINTENANCE CBX250 NOTES...
Page 60: ...4 0 LUBRICATION SYSTEM CBX250 DIAGRAM OF LUBRICATION SYSTEM...
Page 70: ...5 0 FUEL SYSTEM CBX250...
Page 92: ...DISMANTLING AND INSTALLING THE ENGINE CBX250 NOTES...
Page 118: ...8 0 PISTON CYLINDER CBX250...
Page 126: ...PISTON CYLINDER CBX250 NOTES...
Page 128: ...9 0 CLUTCH GEAR SELECTOR CBX250 108 N m 10 8 kg m 12 N m 1 2 kg m 108 N m 10 8 kg m...
Page 142: ...10 0 ALTERNATOR CBX250 103 N m 10 3 kg m...
Page 152: ...11 0 TRANSMISSION CBX250...
Page 166: ...12 0 CRANKSHAFT FLYWHEEL CBX250...
Page 200: ...FRONT WHEEL SUSPENSION STEERING CBX250 NOTES...
Page 222: ...REAR WHEEL BRAKE SUSPENSION CBX250 NOTES...
Page 246: ...BATTERY CHARGING SYSTEM CBX250 NOTES...
Page 256: ...IGNITION SYSTEM CBX250 NOTES...
Page 270: ...ELECTRIC STARTING SYSTEM CBX250 NOTES...