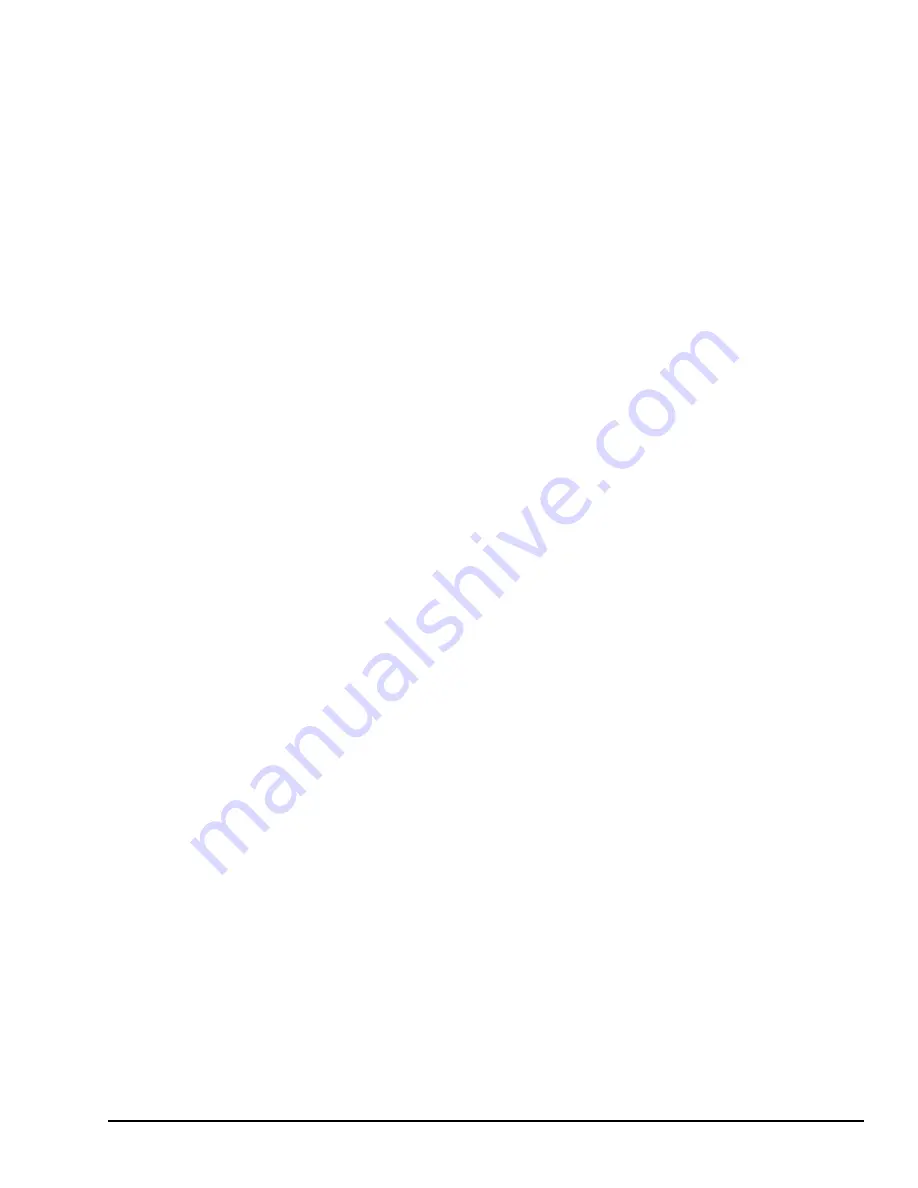
360
Description
Internal Runtime error - Sequencer frame period out-of-bounds (±15%)
Possible Cause
Possible hardware malfunction. Frame period greater than ±15% of nominal. This alarm occurs
following frame period out-of-bounds condition occurring three frames in a row. After five frames in a row, the I/O module is
put into FAILURE control state.
Solution
•
Ignore this alarm if it occurs during a restart of the I/O module.
•
Replace the I/O module, if the alarm occurs during normal operation.
361
Description
Internal Runtime error - Sequencer frame state timeout out-of-bounds (±15%)
Possible Cause
Possible hardware malfunction. Sequencer frame state timeout greater than ±15% of nominal. This alarm
occurs following a sequencer frame state timeout being out-of-bounds for three frames in row. After five frames in a row, the
I/O module is put into FAILURE control state.
Solution
•
Ignore this alarm if it occurs during a restart of the I/O module.
•
Replace the I/O module if the alarm occurs during normal operation.
362
Description
Internal Runtime error - Sequencer frame number skip detected
Possible Cause
Possible hardware or IONet malfunction. Frame number skips detected. Frame number should
monotonically increase until rollover. This alarm occurs following three skips in a row. After five skips in a row, the I/O
module is put into FAILURE control state.
Solution
•
Ignore alarm if it occurs during a restart of the I/O module.
During normal operation:
•
Check for hardware or network switch malfunction.
•
Check for loose or defective network cables.
•
Replace the I/O module.
363
Description
Memory Validation failed - Sequencer data structures
Possible Cause
Hardware memory failure (sequencer process data that should not change after the I/O module is online
was modified).
Solution
Replace the I/O module.
Common I/O Module Functionality
GEH-6855_Vol_II System Guide 467
Public Information