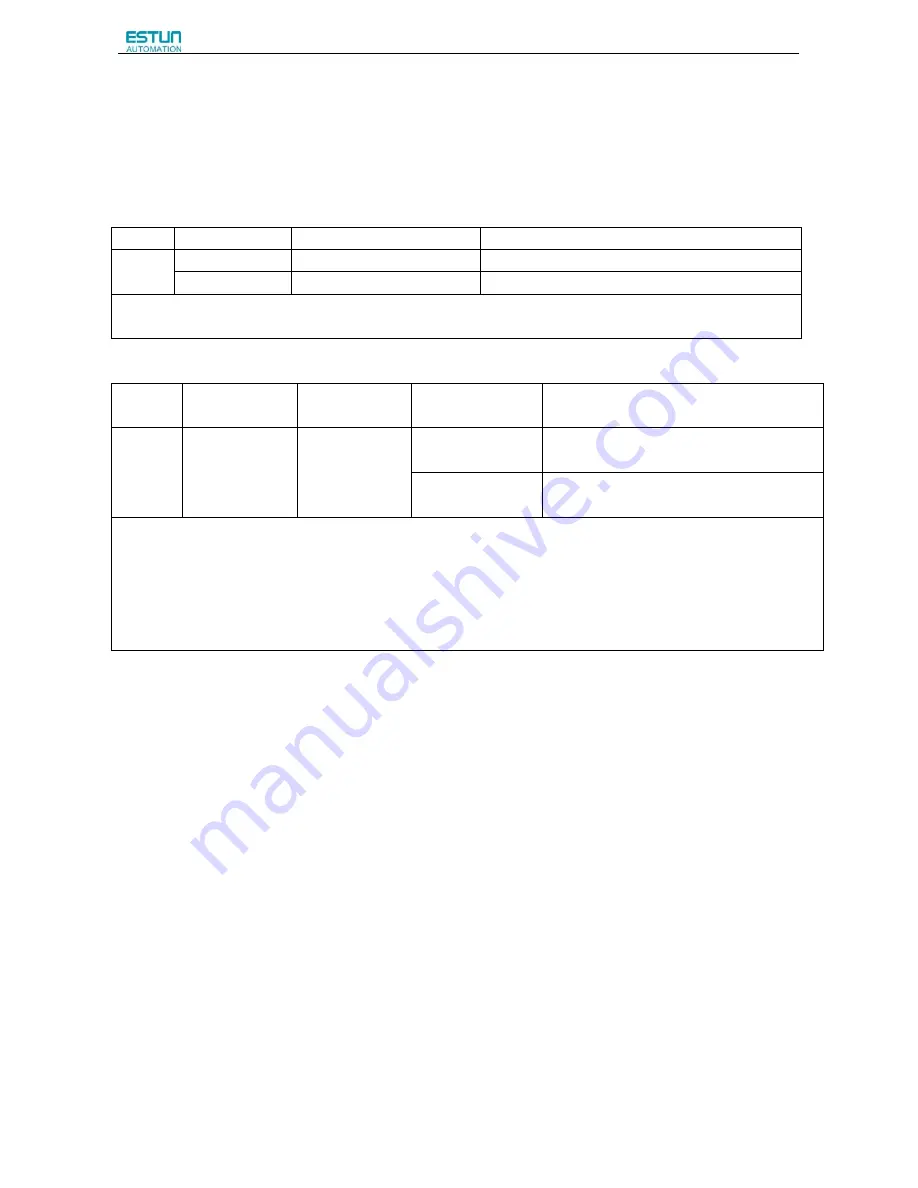
ProNet
Series
AC Servo User's Manual
- 83 -
4.5.2 Setting Input Signals
(
1
)
Speed Reference Input
Input the speed reference to the servo drive using the analog voltage reference to control the servomotor speed in
proportion to the input voltage.
Type
Signal Name
Connector Pin Number
Name
Input
V-Ref+
CN1-1
Speed Reference Input
V-Ref-
CN1-2
Speed Reference Input
The above inputs are used for speed control(analog voltage reference). (Pn005.1=0
,
4
,
7
,
9
,
A) Pn300 is used to set the
speed reference input gain.Refer to
4.5.1 Setting Parameters
.
(
2
)
Proportional Control Reference (/P-CON)
Tpye Signal
Connector Pin
Number
Setting Meaning
Input /P-CON CN1-15
ON(low level)
Operates the servo drive with proportional
control
OFF(high level)
Operates the servo drive with proportional
integral control.
/P-CON signal selects either the PI(proportional integral) or P(proportional) Speed Control Mode.
Switching to P control reduces servomotor rotation and minute vibrations due to speed reference input drift.
Input reference: At 0V, the servomotor rotation due to drift will be reduced, but servomotor rigidity (holding force) drops when
the servomotor is stopped.
Note: A parameter can be used to reallocate the input connector number for the /P-CON signal. Refer to
3.2.2 I/O Signal
Names and Functions
.
Summary of Contents for pronet series
Page 1: ...ProNet SeriesAC Servo User s Manual Version V2 10...
Page 13: ...ProNet Series ACServoUser sManual 11 ProNet 1AD 1ED 2BD ProNet 02B ProNet 04B ProNet 08B...
Page 21: ...ProNet Series ACServoUser sManual 19 ProNet 1AD 1ED 2BD ProNet 02B ProNet E 02B...
Page 22: ...ProNet Series ACServoUser sManual 20 ProNet 04B ProNet E 04B ProNet 08B ProNet E 08B...
Page 193: ......