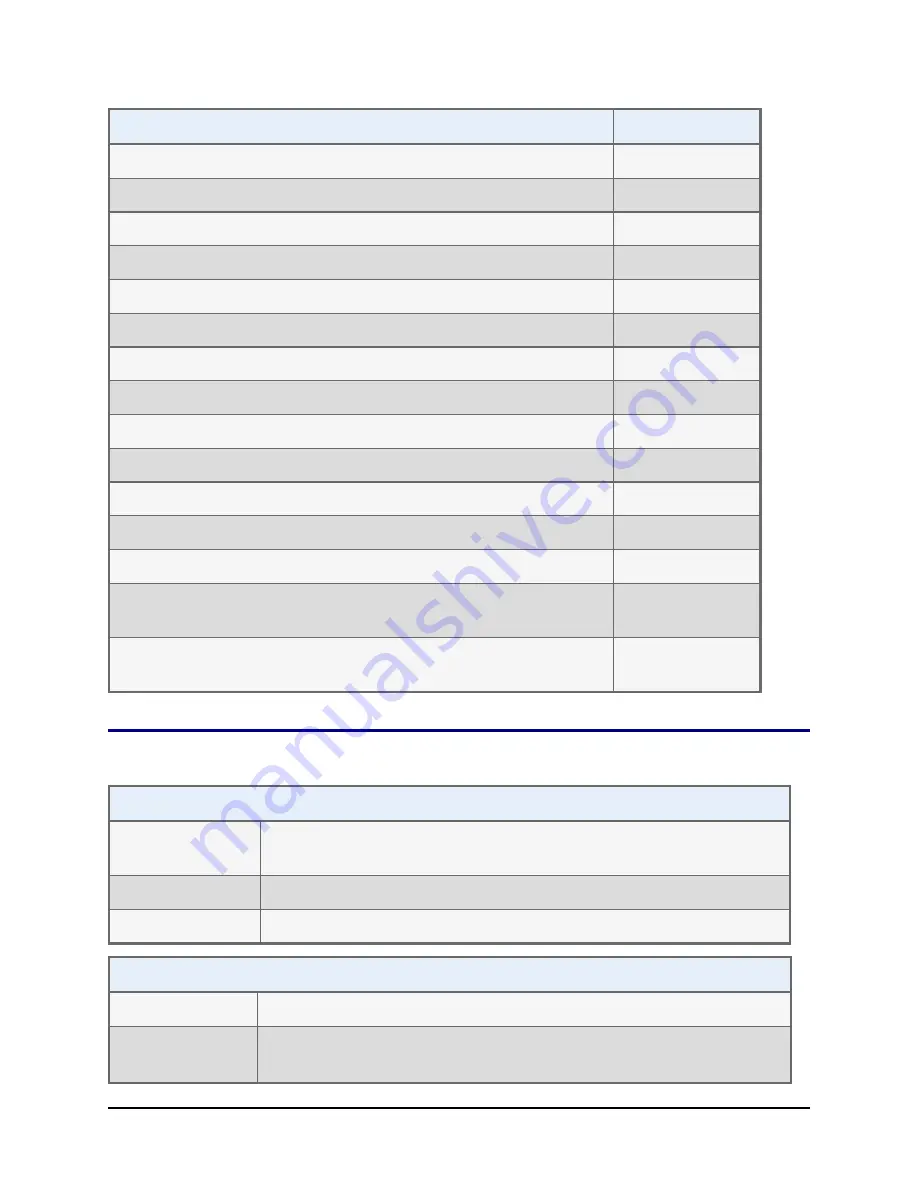
Physical Specifications | 9
Description
PN
10L Dispense Bottle w/filter
1173000
Cap for 10L Dispense Bottle w/filter
1173002
Dispense Tubing Set - 1 Buffer
7100538
Dispense Tubing Set - 4 Buffers (For Buffer Switching models.)
7100537
4L Waste Bottle
7100534
Cap for Waste Bottle, 4L (Also fits 10L and 20L bottles.)
7100531
Waste Bottle with Level Sensing, 4L
7100542
Cap for Waste Bottle with Level Sensing, 4L
7100544
10L Waste Bottle and Tubing
7100557
20L Waste Bottle and Tubing
7100556
Waste Tubing Set
7100533
Vacuum Line Filter for Waste Tubing
48294
Vacuum Gauge/Regulator (For use with house vacuum.)
4030551
Silencing Muffler for Vacuum Pump (For use with P/N 7103024
pump.)
01113
Fluid filter for dispense bottles (does not include stainless steel
adaptor 1172031)
01310
Physical Specifications
Labware
Microplates
96-well, 384-well that comply with SBS microplate standards 1-
2004, 2-2004, 3-2004, and 4-2004.
Microstrips
1 x 8, 1 x 12
Microwells
Flat, round, "V” bottom
Hardware & Environmental
User Interface
2-line x 24 character LCD screen, 26 alphanumeric soft keys
Power Supply
The instrument uses two internal power supplies: 24-volt 60 watt and
48-volt 60 watt. These supplies are compatible with 100-240 V~; 50-
BioTek Instruments, Inc.
Summary of Contents for 405 LS
Page 1: ...Operator s Manual Microplate Washer 405 LS ...
Page 2: ......
Page 56: ...36 Chapter 2 Installation 405 Microplate Washer LS ...
Page 134: ...114 Chapter 3 Operation 405 Microplate Washer LS ...
Page 190: ...170 Chapter 5 Qualification 405 Microplate Washer LS ...
Page 210: ...190 Chapter 7 Troubleshooting 405 Microplate Washer LS ...
Page 238: ......