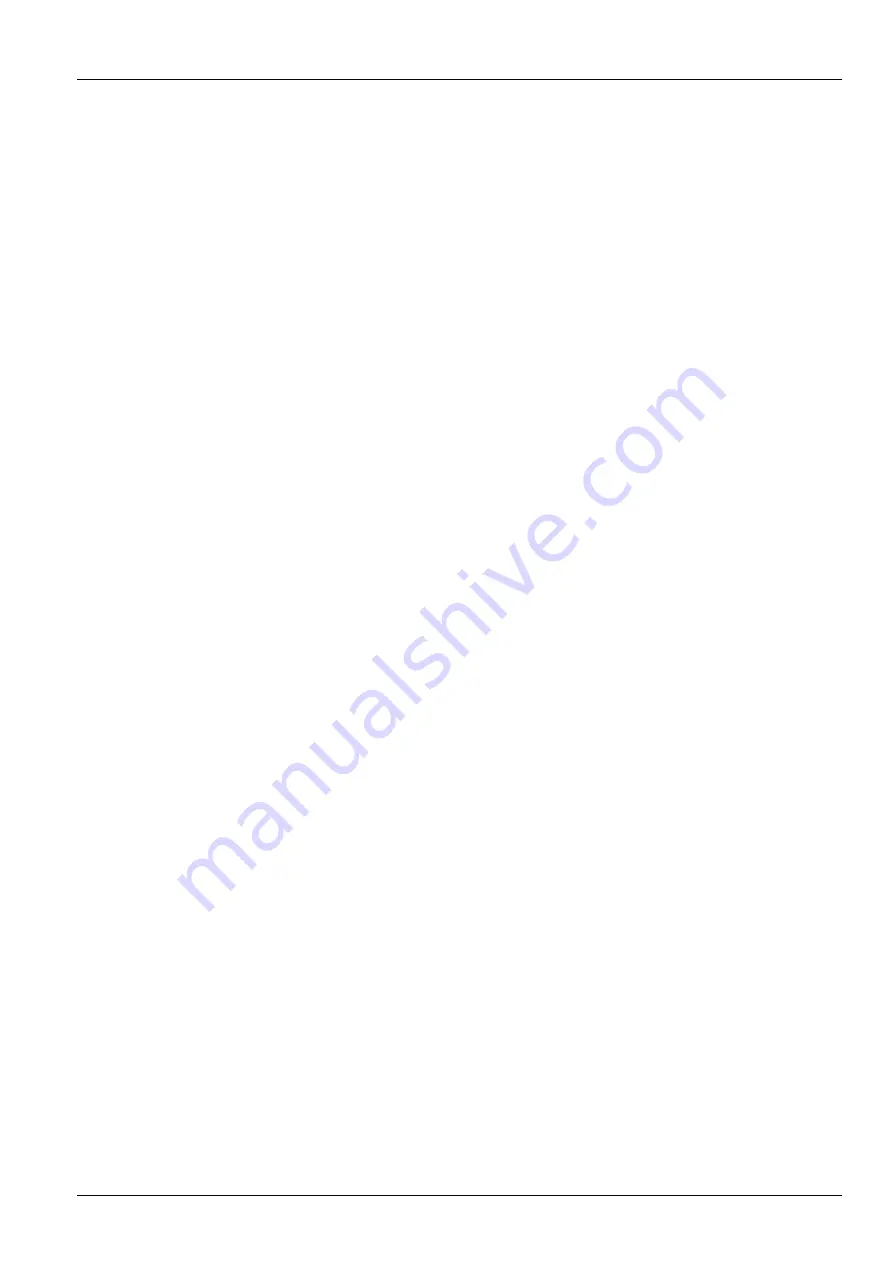
6 - WORKING OPERATIONS
Anchor out /Anchor in method: You can control the
stretch in the bag by either letting out the anchor or
pulling it in.
1. Anchor Out: The further out the anchors extend, the
more pressure will be exerted, meaning the bag will
have higher compaction. Watch the anchor gauge so
you will know how much cable is out. This will cause
the stretch bars on the bag to lengthen. You can let
more cable out by using the anchor float switch on the
right side console. Do not use the anchor cable in/out
switch to let the anchor cable out while bagging, this
can create slack in the anchor cables
2. Anchor In: By pulling the anchors back toward the tun-
nel you will lessen the amount of pressure and cause
the stretch bars to become smaller. Use the anchor
cable in switch on the right side console to pull the an-
chors in. Watch the anchor pressure on the System
Monitor display and keep it in the correct range.
Sealing and venting
As soon as the bag is filled, seal the finished end of the bag as outlined with the Master Seal instructions or using
the double knot method. The sooner oxygen is sealed out, the sooner the fermentation process can begin. It is very
important to vent the bag after sealing. Refer to
6-40
for proper venting procedure. Order Master seal and reusable
vents from your local Ag-Bag dealer. Refer to the list that follows for specific part numbers:
Part Number 42.1500272 -
76 m
(
250 ft
) Roll of Master Seal
Part Number 42.1500893 - Reusable bag vent
Part Number 42.1500568 - Vent installation tool
Protecting the Bag From Wind Damage
Wind damage can be caused by the wind whipping the loose end of the bag. To prevent damage, the loose bag end
needs to be secured by placing tires or other soft material on the end of the bag. Wind damage can cause small
cracks and eventually wear a hole that allows air to penetrate, causing feed damage. A tightly secured bag will add
to the life of the bag.
Bag Management and Inspection
Periodic inspection of the bag is essential to maintain the oxygen free environment inside the bag. It is recommended
that repairs be made with Ag-Bag mending tape as soon as they are discovered. Repair tape can be ordered from
your local Miller Ag-Bag dealer using the following part numbers:
Part Number 42.1500523
5 cm
(
2 in
) x
33 m
(
36 yd
) roll, 18 rolls per case
Part Number 42.1500525
8 cm
(
3 in
) x
33 m
(
36 yd
) roll, 24 rolls per case
Part Number 42.1501331
10 cm
(
4 in
) x
33 m
(
36 yd
) roll, 18 rolls per case
Bagging surface
Do not bag on a hillside, tip over or bag roll could result. Bag up hill rather than down hill. Avoid bagging on a hillside.
The bagger can drift and the bag may roll.
Surface conditions may affect bagging quality and ability. Soft ground conditions will act as a brake and may cause
the bagger to sink. A hard clean and level surface is best to bag on. By cleaning the area, rodent problems can be
reduced or eliminated.
Bad weather bags
Consider the surface conditions during the seasons when product will be removed from the bags. If you expect a lot
of mud, you may want to put some bags on a solid surface. Have enough accessible bags to last until good weather
conditions can be expected.
NOTE:
Remember to place bags in a location that feed out can be done when you need the feed.
6-3
Summary of Contents for LX1214
Page 8: ......
Page 11: ...1 GENERAL INFORMATION Your machine RAIL16SP00177FA 1 Ag Bag silage bagger 1 3 ...
Page 28: ...2 SAFETY INFORMATION California proposition 65 warning BT09A213 1 2 10 ...
Page 32: ...2 SAFETY INFORMATION RAIL16SP00182FA 3 RAIL16SP00183FA 4 2 14 ...
Page 94: ...4 OPERATING INSTRUCTIONS 4 10 ...
Page 158: ...6 WORKING OPERATIONS 6 52 ...
Page 260: ...7 MAINTENANCE 7 102 ...
Page 270: ...8 TROUBLESHOOTING 8 10 ...
Page 272: ...9 SPECIFICATIONS 9 2 ...