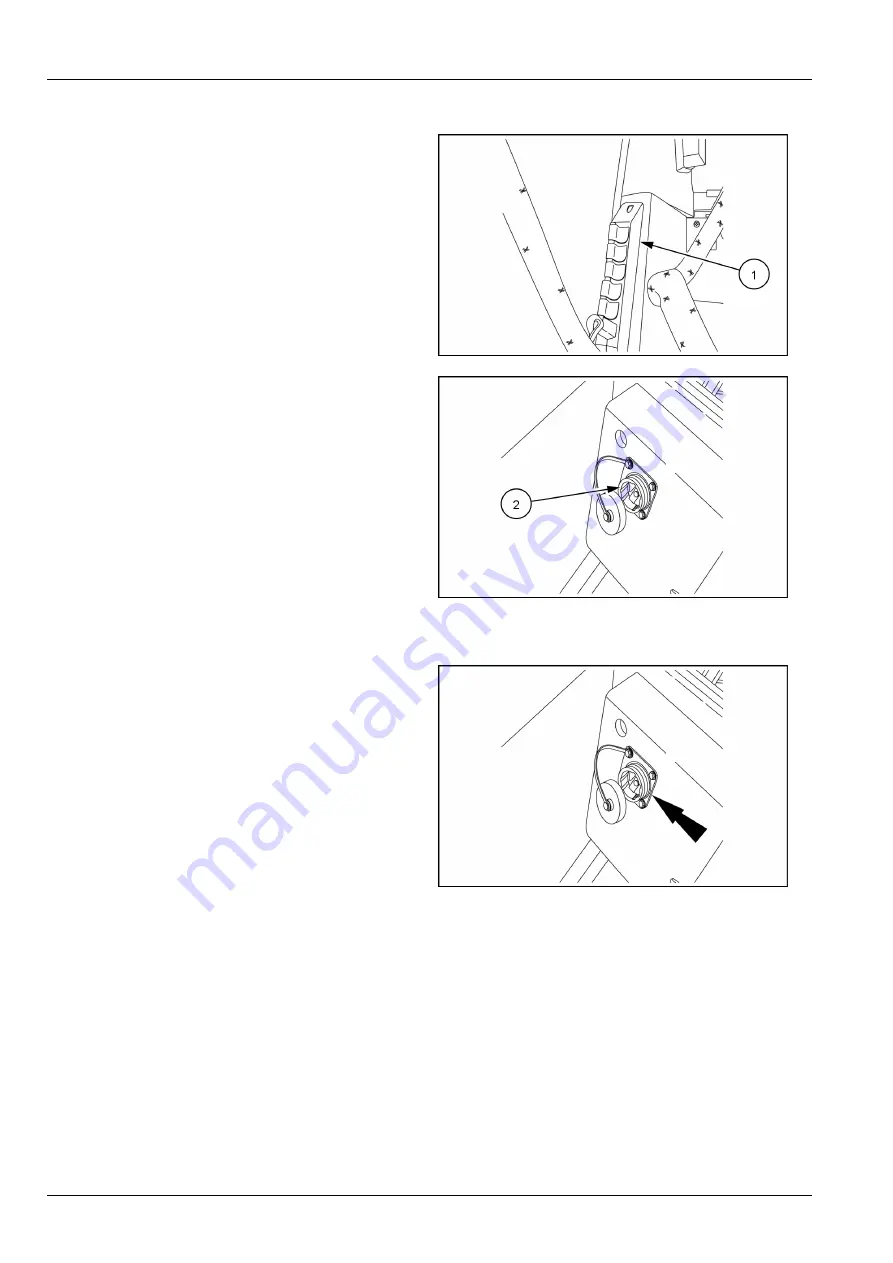
3 - CONTROLS AND INSTRUMENTS
Power strip electrical outlets
A
30 A
power strip
(1)
provides six additional electrical
key switched or unswitched outlets. The power strip is
fed with two
30 A
breaker feeds, one live all the time and
one key switch controlled. The breakers and relay are
located in the right rear corner of the cab below the aux-
iliary power outlet.
(2)
It can be used to provide power
for radios, cell phones, GPS and other electrical devices.
Optional power cords that plug directly into the power strip
are available with either cigarette lighter style adapters or
individual key switched or unswitched power wires. See
your dealer for ordering. Available plug can be ordered
from your dealer. The power strip is located to the right of
the operators seat next to the side window.
RAIL16GEN0080AA
3
RAIL16GEN0081AA
4
Auxiliary power outlet
The auxiliary power outlet located on the rear cab wall be-
hind the right side console provides two
30 A
terminals.
When connected, one power terminal provides a contin-
uous power source, the other provides power only when
the ignition key is turned to the accessory or run position.
Available plug can be ordered from your dealer.
RAIL16GEN0081AA
5
3-46
Summary of Contents for LX1214
Page 8: ......
Page 11: ...1 GENERAL INFORMATION Your machine RAIL16SP00177FA 1 Ag Bag silage bagger 1 3 ...
Page 28: ...2 SAFETY INFORMATION California proposition 65 warning BT09A213 1 2 10 ...
Page 32: ...2 SAFETY INFORMATION RAIL16SP00182FA 3 RAIL16SP00183FA 4 2 14 ...
Page 94: ...4 OPERATING INSTRUCTIONS 4 10 ...
Page 158: ...6 WORKING OPERATIONS 6 52 ...
Page 260: ...7 MAINTENANCE 7 102 ...
Page 270: ...8 TROUBLESHOOTING 8 10 ...
Page 272: ...9 SPECIFICATIONS 9 2 ...