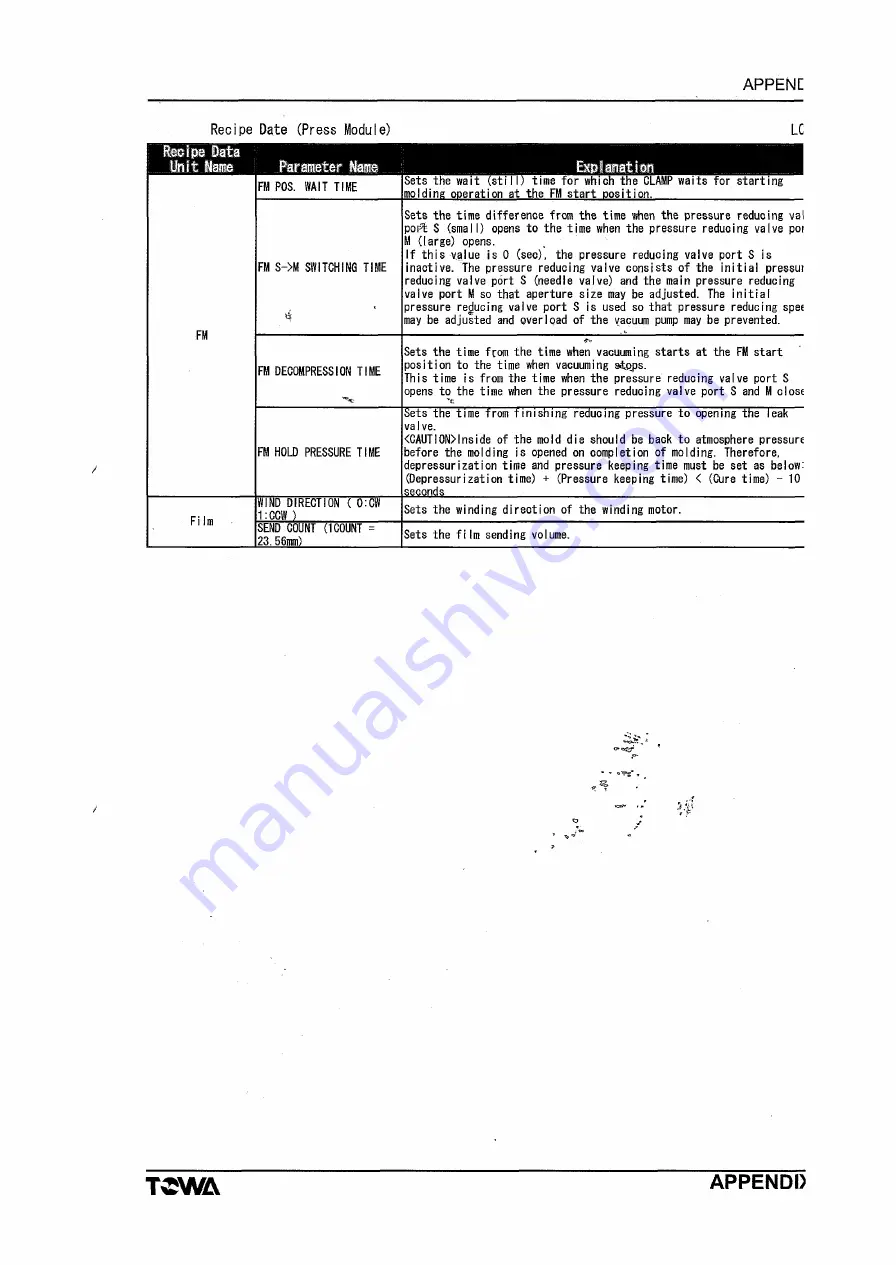
APPENC
Recipe Date (Press Module)
LC
Recipe Data
Unit Name
Parameter Name
Expfanation
FM POS. WAIT TIME
Sets the wait (still) time for which the CLAMP waits for starting
molding operation at the FM start oosition.
FM
FM S->M SWITCHING TIME
Sets the time difference from the time when the pressure reducing val
port S (small) opens to the time when the pressure reducing valve poi
M (large) opens.
If this value is 0 (sec), the pressure reducing valve port S is
inactive. The pressure reducing valve consists of the initial pressui
reducing valve port S (needle valve) and the main pressure reducing
valve port M so that aperture size may be adjusted. The initial
pressure reducing valve port S is used so that pressure reducing spes
may be adjusted and overload of the vacuum pump may be prevented.
FM DECOMPRESSION TIME
■?*
Sets the time from the time when vacuuming starts at the FM start
position to the time when vacuuming stops.
This time is from the time when the pressure reducing valve port S
opens to the time when the pressure reducing valve port S and M close
vt
FM HOLD PRESSURE TIME
Sets the time from finishing reducing pressure to opening the leak
valve.
<CAUTI0N>Inside of the mold die should be back to atmosphere pressure
before the molding is opened on completion of molding. Therefore,
depressurization time and pressure keeping time must be set as below:
(Depressurization time)
+
(Pressure keeping time)
<
(Cure time) - 10
seconds
Pi Im
WIND DIRECTION ( 0:CW
1
:CCW )
Sets the winding direction of the winding motor.
SEND COUNT (1 COUNT =
23
.
56
imi)
Sets the film sending volume.
T£W A
APPENDI)
Содержание LCM1010
Страница 9: ...1 GENERAL INFORMATION LCM 1010 Instruction Manual TCWA...
Страница 86: ...LCM1010 Instruction Manual 5 PREPARATION TCWA 5 5...
Страница 111: ...6 OPERATION LCM 1010 Instruction Manual 6 22 TCWA...
Страница 174: ...LCM1010 Instruction Manual 2 SAFETY NOTE The f gure below is for use with four Press Modules Automatic T WA 2 39...
Страница 191: ...3 OUTLINE OF MACHINE LCM 1010 Instruction Manual 3 12 TSWA...
Страница 193: ...4 OPERATION SWITCHES AND BUTTONS LCM 1010 Instruction Manual T WA...
Страница 211: ...LCM1010 Instruction Manual 5 PREPARATION TSWA 5 5...
Страница 433: ...LCM 1010 Instruction Manual 4 INSTALLATION NOTE The figure below is for use with four Press modules Automatic TCWA 4 5...
Страница 480: ...4 INSTALLATION LCM1010 Instruction Manual Factory facility 1 n il 555l I 4 52 TCWA...
Страница 493: ...hoocividli Mi u r c rtoociviDLi piN mcuftoc u r m MMorum luivi iu iu instruction manual t w a...
Страница 528: ...APPEND APPENDIX 1 4 CHARGE NUMBERLIST TSWA APPENDI...
Страница 533: ...APPENt g APPENDIX 2 3 RedpeDataandConstantData TSWA APPENDI...
Страница 549: ...4...
Страница 551: ...P R E S S M O D U L E I...