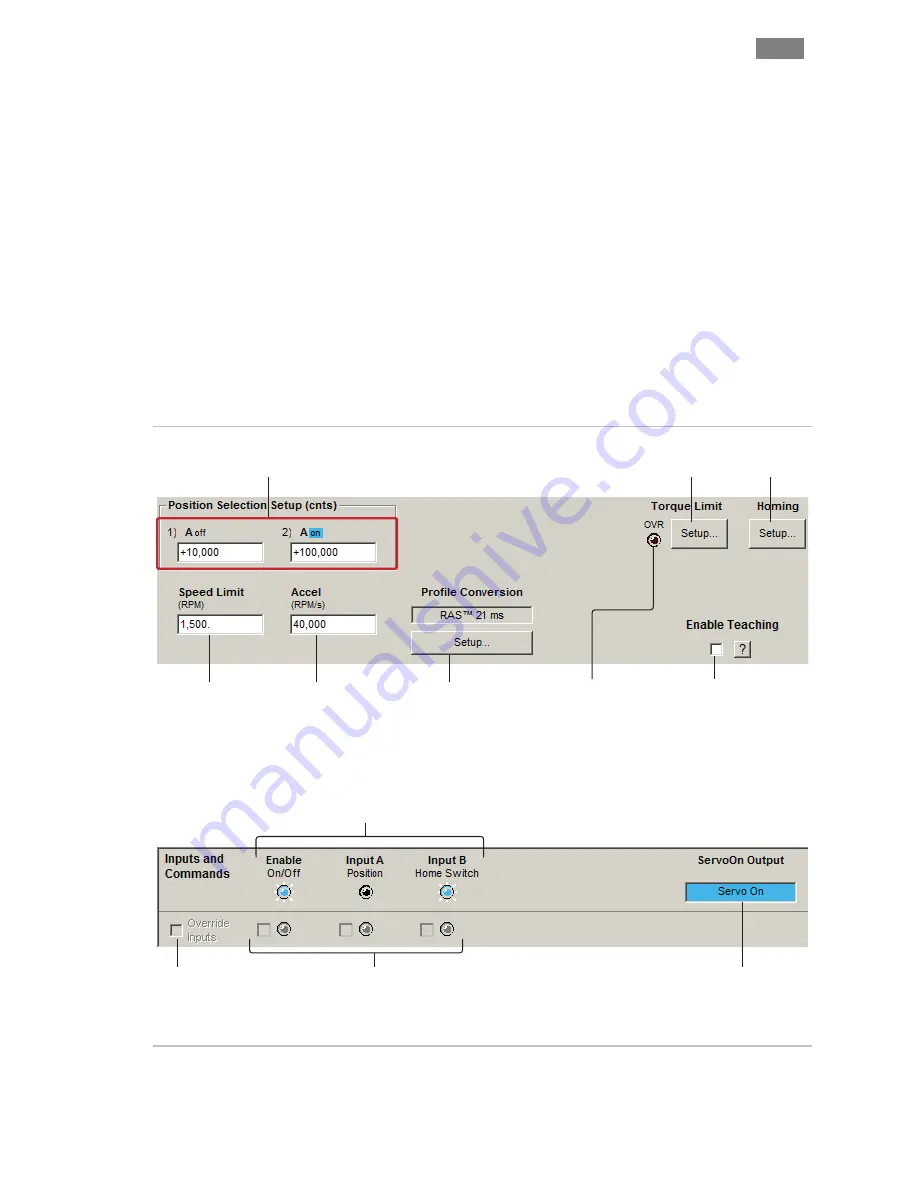
C
L E A R
P
A T H
M C / S D
U
S E R
M
A N U A L
R
E V
.
3 . 0 9
1 2 3
T
EKNIC
,
I
NC
. T
EL
.
(585)
784-7454
•
The user-defined positions can be 'taught' instead of entered
numerically through MSP. To do this, the motor must be in a
Logic Backup Power (LBP) state (using a ClearPath POWER4-
HUB board). The main bus power must be off.
To teach a
position
, deassert the Enable input with the motor in the
position you want to teach (or deassert the Enable and then
move the axis by hand to the desired spot). Set input A to the
binary state you want to teach, and assert the Enable input. The
current location will then be linked to the current input A state.
Deassert Enable and repeat as desired with the other A state.
•
Input B switch polarity can be inverted via a checkbox in the
Homing Setup dialog. When home switch polarity is inverted,
ClearPath interprets Input B-low as “in the home switch”, and
Input B-high as “not in the home switch”.
•
Disable time = 10 mS
M
ODE
C
ONTROLS
Hardware Input Status LEDs
Light = Input asserted (on)
Dark = Input de-asserted (off)
Soft Inputs and LEDs
emulate
hardware inputs. For use only
when Soft Controls are active.
Caution: motor may spin when
enabled.
Check to turn on Soft
Controls. Override cannot
be activated when ClearPath
is hardware enabled.
Displays HLFB
output status.
Enter max. desired
motor speed.
Enter max. desired
acceleration rate.
Click to open
Homing
Setup dialog.
Set Target Positions
Enter move distance (from
home) for each input state.
Click to open
Torque Limit
Setup dialog.
Adjust settings for
RAS
TM
(or
optional
g-Stop
TM
) to convert
standard trapezoidal move
profiles into profiles that reduce
noise, resonance, and vibration.
Torque Override Indicator
When lit, the main torque limit
is being overridden by a
secondary, user-set torque limit
(e.g., when an axis is homing,
the main torque limit may be
overridden by the separate
homing torque limit setting).
Enable teaching mode.
This allows the user to
physically move a motor to
a desired target position
and save that position to
the motor’s memory (as
opposed to keying in
numerical values.