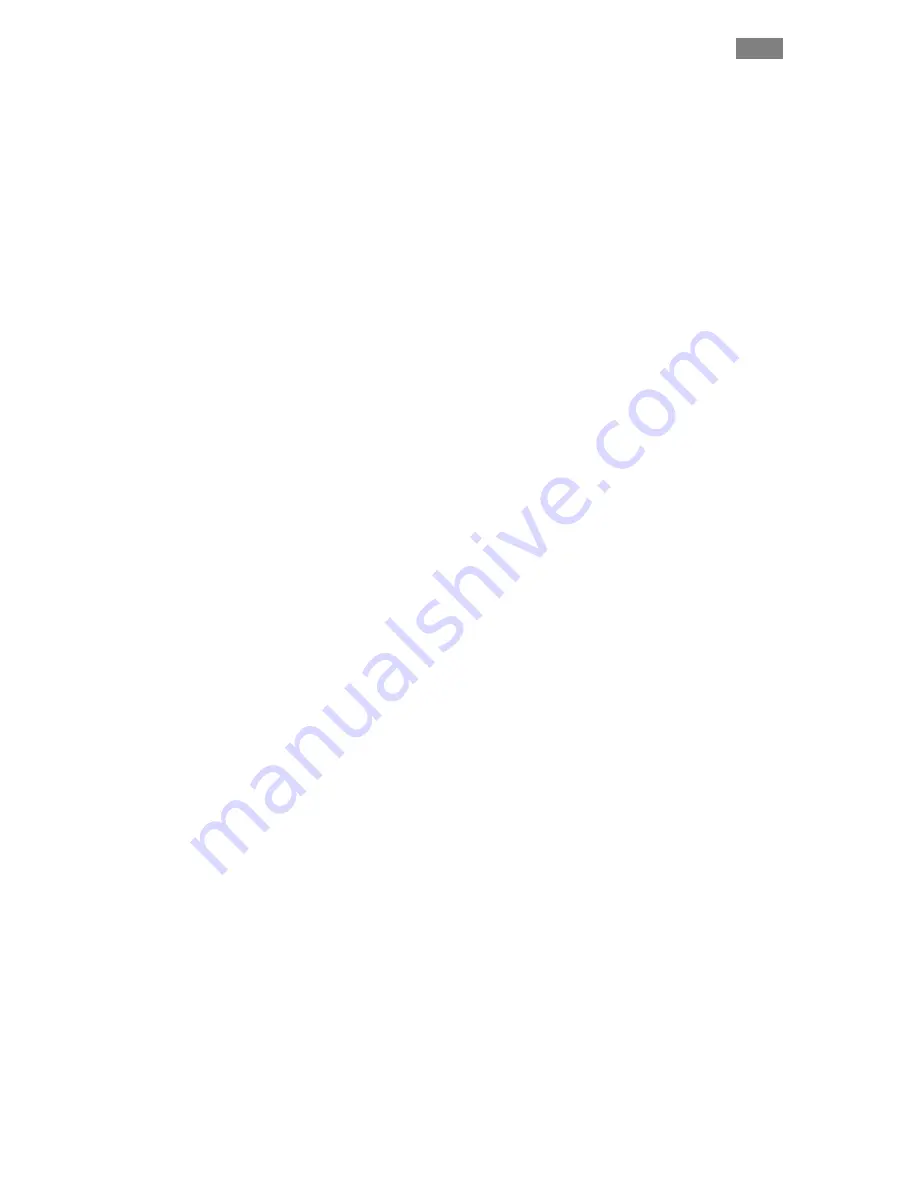
C
L E A R
P
A T H
M C / S D
U
S E R
M
A N U A L
R
E V
.
3 . 0 9
1 6 4
T
EKNIC
,
I
NC
. T
EL
.
(585)
784-7454
•
Use lightweight components.
Aluminum couplings,
pinions, and pulleys add significantly less inertia to the motion
system than steel parts of the same size. In most applications,
lower inertia is preferable because it allows the motor (and
attached mechanics) to accelerate harder and move and settle
faster.
•
Avoid using set screws.
Coupling devices with
set screws are
prone to failure and often become the weak link when joining a
motor to a load. Set screws deform the metal around the screw’s
point of contact, often resulting in a raised bur on the shaft that
can make it hard to remove and replace the coupling element.
Set screws also tend to slip and score the shaft.
•
Tip:
Couplings, pulleys and pinions with circumferential
clamping mechanisms tend not to damage motor shaft, hold
better, and are easier to replace than those that use set screws.
•
Clamp close to the motor.
For maximum performance,
secure pulleys and pinions as close to the motor face as is
practical. This effectively reduces the lever arm (and associated
bearing load) for applications with a side load.
•
Don’t over tighten belts.
Always read the belt
manufacturer’s guidelines for proper belt tension, but never
exceed the ClearPath specification for maximum side load.
Overly tight belts put undue stress on the motor shaft and
bearing systems that can result in premature bearing and shaft
failure.
•
Avoid using shaft keys when possible.
Although ClearPath
includes a keyway feature on the shaft, Teknic does not
generally recommend the use of keys. Keys tend to cause run-
out and backlash errors, particularly in reciprocating, precision
positioning motion applications.
However, keys should be considered
for use in
applications where coupling slip could result in a dangerous or
hazardous condition. Also, key use may be appropriate for
unidirectional applications (where the motor always spins in the
same direction) as these applications are less prone to key-
related lash problems.
•
Avoid direct loads.
In general, ClearPath motors are not
designed for connection to direct loads (e.g. direct connection to
a grinding wheel). However, direct connection may make sense
if the load is of low-mass and balanced, as with small mirrors
for laser applications.