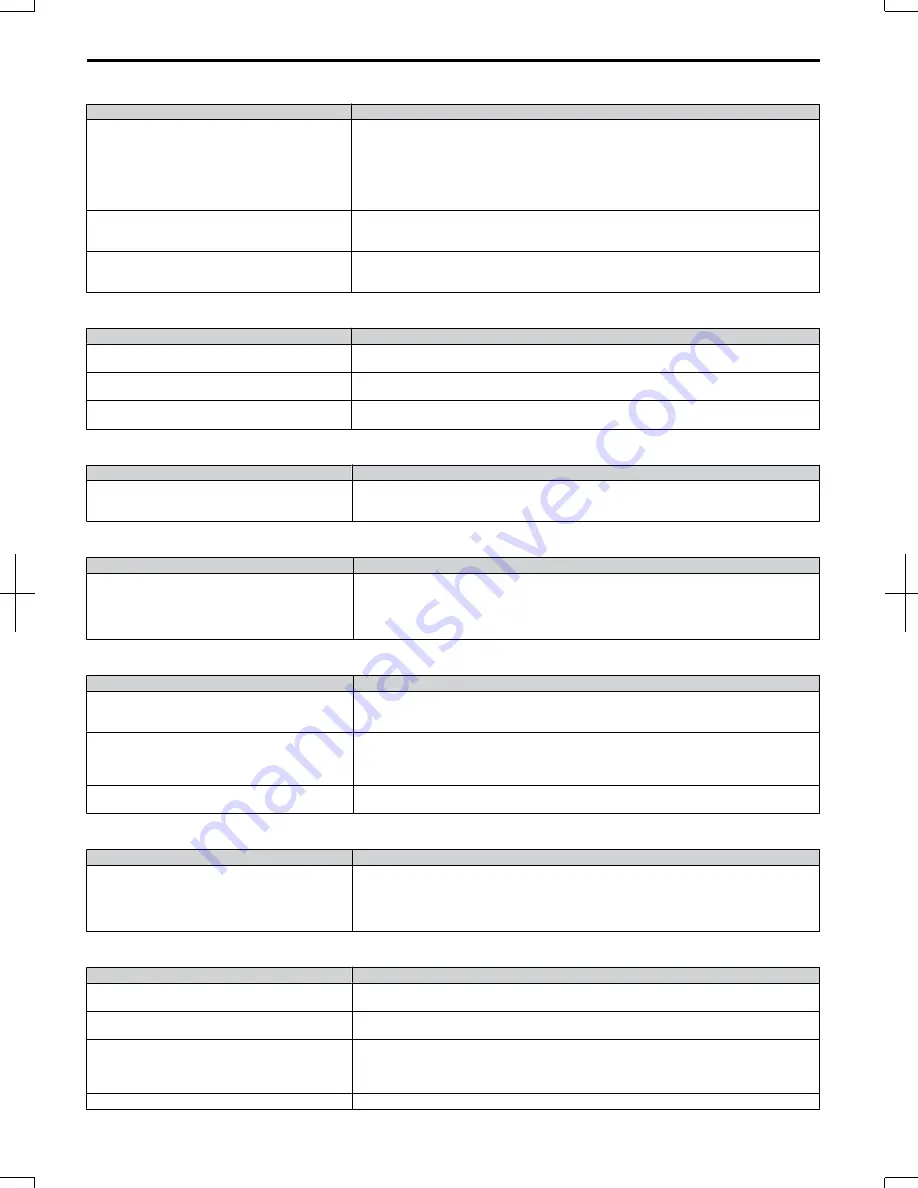
n
PID output fault
Cause
Possible Solutions
No PID feedback input.
• Check the multi-function analog input terminal settings.
• Set multi-function analog input terminal A1 or A2 for PID feedback (H3-02 or H3-10 = “B”).
• A signal input to the terminal selection for PID feedback is necessary.
• Check the connection of the feedback signal.
• Check the various PID-related parameter settings.
• No PID feedback input to the terminal causes the value detected to be 0, causing a PID fault
and the drive to operate at max frequency.
The level of detection and the target value do not
correspond with each other.
• PID control keeps the difference between target and detection values at 0. Set the input level
for the values relative to one another.
• Use analog input gains H3-03/11 to adjust PID target and feedback signal scaling.
Reverse drive output frequency and speed detection.
When output frequency rises, the sensor detects a
speed decrease.
Set PID output for reverse characteristics (b5-09 = “1”).
n
Insufficient Motor Torque
Cause
Possible Solutions
Auto-Tuning has not yet been performed (required for
OLV Control).
Perform Auto-Tuning.
The control mode was changed after performing
Auto-Tuning.
Perform Auto-Tuning again.
Only Line-to-Line Resistance Auto-Tuning was
performed.
Perform Rotational Auto-Tuning.
n
Motor Rotates After the Drive Output is Shut Off
Cause
Possible Solutions
Low DC Injection Braking and the drive cannot
decelerate properly.
• Adjust the DC Injection braking settings.
• Increase the value of b2-02 (DC Injection Braking Current).
• Increase the b2-04 (DC Injection Braking Time at Stop).
n
ov or Speed Loss Occurs When Starting into a Rotating Load
Cause
Possible Solutions
The load is already rotating when the drive is trying
to start it.
• Stop the motor using DC Injection braking. Restart the motor.
• Increase the value of b2-03 (DC Injection Braking Time at start).
• Enable Speed Search at start (b3-01 = “1”).
• Set a multi-function input terminal for external Speed Search command (H1-
=“61” or
“62” during restart).
n
Output Frequency is not as High as Frequency Reference
Cause
Possible Solutions
Frequency reference is set within the range of the
Jump Frequency.
• Adjust the parameters used for the Jump Frequency function (d3-01, d3-02, d3-03).
• Enabling the Jump Frequency prevents the drive from outputting the frequencies specified
in the Jump Frequency range.
Upper limit for the frequency reference has been
exceeded.
• Set the maximum output frequency and the upper limit for the frequency reference to more
appropriate values (E1-04, d2-01).
• The following calculation yields the upper value for the output frequency = E1-04 x d2-01 /
100
Large load triggered Stall Prevention function during
acceleration.
• Reduce the load.
• Adjust the Stall Prevention level during acceleration (L3-02).
n
Buzzing Sound from Motor at 2 kHz
Cause
Possible Solutions
Exceeded 110% of the rated output current of the
drive while operating at low speeds.
• If the output current rises too high at low speeds, the carrier frequency automatically reduces
and causes a whining or buzzing sound.
• If the sound is coming from the motor, disable carrier frequency derating (L8-38 = “0”).
• Disabling the automatic carrier frequency derating increases the chances of an overload fault
(oL2). Switch to a larger capacity motor if oL2 faults occur too frequently.
n
Unstable Motor Speed when Using PM or IPM
Cause
Possible Solutions
The motor code for PM (E5-01) is set incorrectly.
(Yaskawa motors only)
Set parameter E5-01 in accordance with the motor being used.
The drive is operating at less than 10% of the speed
reference.
Consult with OYMC about using a different type of motor when attempting to operate at 10%
of the speed reference.
Motor hunting occurs.
Set and carefully adjust the following parameters in the order listed:
• n8-45 (Speed Feedback Detection Suppression Gain)
• n8-55 (Load Inertia for PM Motors)
• C4-02 (Torque Compensation Primary Delay Time)
Hunting occurs at start.
Increase the S-curve time at the start of acceleration (C2-01).
6.9 Troubleshooting without Fault Display
258
SIEP C710606 20 OYMC AC Drive - V1000 User Manual
7/16/2008-13:23
Содержание V1000
Страница 11: ...Table of Contents This Page Intentionally Blank 10 SIEP C710606 20 OYMC AC Drive V1000 User Manual ...
Страница 27: ...1 4 Component Names This Page Intentionally Blank 26 SIEP C710606 20 OYMC AC Drive V1000 User Manual ...
Страница 37: ...2 2 Mechanical Installation This Page Intentionally Blank 36 SIEP C710606 20 OYMC AC Drive V1000 User Manual ...
Страница 63: ...3 12 Wiring Checklist This Page Intentionally Blank 62 SIEP C710606 20 OYMC AC Drive V1000 User Manual ...
Страница 221: ...5 11 U Monitor Parameters This Page Intentionally Blank 220 SIEP C710606 20 OYMC AC Drive V1000 User Manual ...
Страница 273: ...7 5 Drive Replacement This Page Intentionally Blank 272 SIEP C710606 20 OYMC AC Drive V1000 User Manual ...
Страница 287: ...8 6 Connecting an Option Card This Page Intentionally Blank 286 SIEP C710606 20 OYMC AC Drive V1000 User Manual ...
Страница 297: ...A 6 Drive Derating Data This Page Intentionally Blank 296 SIEP C710606 20 OYMC AC Drive V1000 User Manual ...
Страница 379: ...C 13 Self Diagnostics This Page Intentionally Blank 378 SIEP C710606 20 OYMC AC Drive V1000 User Manual ...
Страница 409: ...Index This Page Intentionally Blank 408 SIEP C710606 20 OYMC AC Drive V1000 User Manual ...
Страница 410: ...This Page Intentionally Blank SIEP C710606 20 OYMC AC Drive V1000 User Manual 409 ...