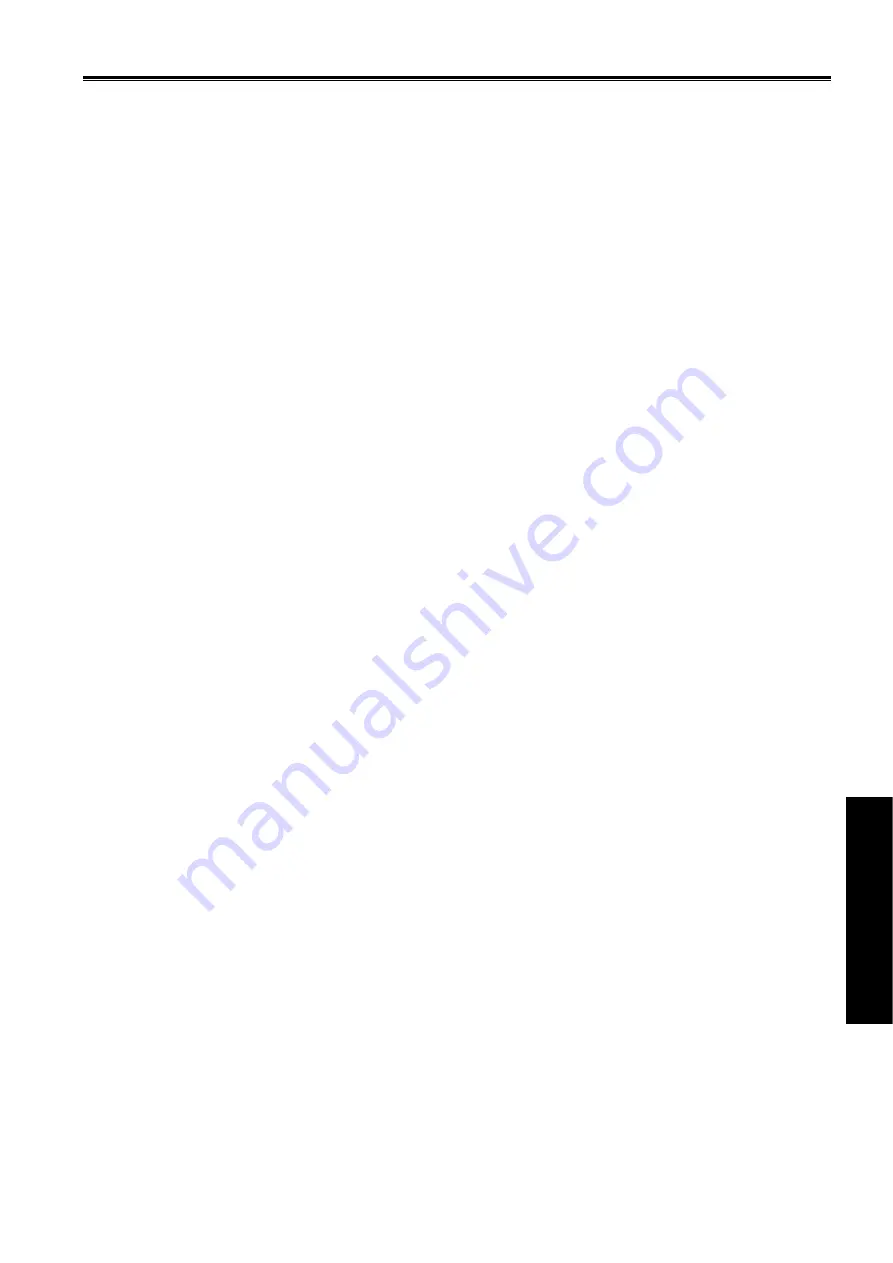
Appendix
451
Appendix
In the mode of MPG, STEP or MANUAL, press the release/clamp tool key in the machine spindle.
Press and do not release which means asking spindle to release the tool, air pressure outputted.
Release the key means asking spindle to clamp the tool. When the releasing/clamping tool does not
work:
1: make sure K11.5 spindle releasing/clamping tool parameter set to1
2: when spindle clamping tool, observe X1.5 is changing or not in Ladder->PLC. If it is not
changed, check the machine tools electric.
3: if X1.5 changed, please observe Y2.0 has an output or not in Ladder->PLC. If it do has, check
the machine tools electric, and the motor controlling spindle releasing/clamping tool is started or not.
4: when there is an overtime alarm when releasing/clamping tool, please observe X2.0 or X1.7 in
Ladder->PLC is in position or not. If not, please check the machine tools electric.
5: when there is a releasing/clamping tool key in system panel, please open there switch of K12.0
parameter. The release/clamp tool keys in system panel and in machine should not be used at the
same time, for only one of them is valid, to avoid disoperation.
Auto spindle releasing/clamping tool
Please make sure there is no tool in spindle when test the degree of tightness of the
spindle to avoid tool damage
.
In AUTO, or MDI mode, when the spindle is still, input M54 (spindle releasing tool), or M55
(spindle clamping tool) function, press CYCLE START key. When the spindle does not work out:
1: when illegal M code alarm exists, please make sure K11.5 parameter is open;
2: when after being inputted, the releasing/clamping tool has no output, please observe Y2.0 has an
output or not in Ladder->PLC. If it do has, please check the machine tools electric, and make sure the
motor starts the spindle releasing/clamping tool or not.
3: when there is an overtime alarm when releasing/clamping tool, please observe X2.0 or X1.7 in
Ladder->PLC is in position or not. If not, please check the machine tools electric.
Spindle orientation accomplishment
In MDI or AUTO mode, starting M19 stands for spindle orientation accomplished. When M19
cannot work out:
1: make sure Y3.0 has an output in Ladder->PLC. If there is an output, please check the servo spindle
is accomplishing the spindle orientation.
2: when there is an alarm when spindle orientating, please check in Ladder->PLC that X5.2 signal is in
position. If it is not in position, please check the machine tools electric or connections to the servo
spindle.
3: when the orient position is not exact, please set the parameter corresponding to the servo
spindle. For details, please see to the operations of the servo spindle.
Reference point setting
There are two reference points needed to be set in 980MDc turret tool magazine, that is, the 2nd
reference point and the 3rd reference point (data parameter No.1241an data parameter N0.1242).
The main aim of setting these two reference points is that G28 is not needed to impact the zero block
every time. When the distance of the travel is long enough (the spindle moves to not higher than the
block of the toolpot). That the 3rd reference point is set at a safe and not block hitting position when
the tools are changed is suggested. When the distance of the travel is not long enough, then there is
no need to set the 3rd reference point. In this situation the 3rd reference point is 0, the machine zero.
To set the 2nd reference point, first raise the spindle to safe place, push the manipulator to the right,
and move the Z axis slowly to the place where the manipulator can reach by hand wheel or in
Содержание 980MDc
Страница 19: ...GSK980MDc Milling CNC User Manual XVIII ...
Страница 20: ...1 I Programming Programming Ⅰ ...
Страница 21: ...GSK980MDc Milling CNC System User Manual 2 I Programming ...
Страница 139: ...GSK980MDc Milling CNC System User Manual 120 I Programming ...
Страница 191: ...GSK980MDc Milling CNC System User Manual 172 I Programming ...
Страница 192: ...173 Ⅱ Operation Ⅱ Operation ...
Страница 193: ...GSK980MDc Milling CNC System User Manual 174 Ⅱ Operation ...
Страница 200: ...Chapter 1 Operation Mode and Display 181 Ⅱ Operation ...
Страница 201: ...GSK980MDc Milling CNC System User Manual 182 Ⅱ Operation ...
Страница 249: ...GSK980MDc Milling CNC System User Manual 230 Ⅱ Operation ...
Страница 253: ...GSK980MDc Milling CNC System User Manual 234 Ⅱ Operation ...
Страница 259: ...GSK980MDc Milling CNC System User Manual 240 Ⅱ Operation ...
Страница 265: ...GSK980MDc Milling CNC System User Manual 246 Ⅱ Operation ...
Страница 293: ...GSK980MDc Milling CNC System User Manual 274 Ⅱ Operation ...
Страница 295: ...GSK980MDc Milling CNC System User Manual 276 Ⅱ Operation ...
Страница 319: ...GSK980MDc Milling CNC System User Manual 300 Ⅱ Operation ...
Страница 320: ...301 Ⅲ Installation Ⅲ Installation ...
Страница 321: ...GSK980MDc Milling CNC System User Manual 302 Ⅲ Installation ...
Страница 345: ...GSK980MDc Milling CNC System User Manual 326 Ⅲ Installation ...
Страница 391: ...GSK980MDc Milling CNC System User Manual 372 Ⅲ Installation ...
Страница 392: ...Appendix 373 Appendix Appendix ...
Страница 393: ...GSK980MDc Milling CNC System User Manual 374 Appendix ...
Страница 394: ...Appendix 375 Appendix Appendix 1 Outline Dimension of GSK980MDc L N ...