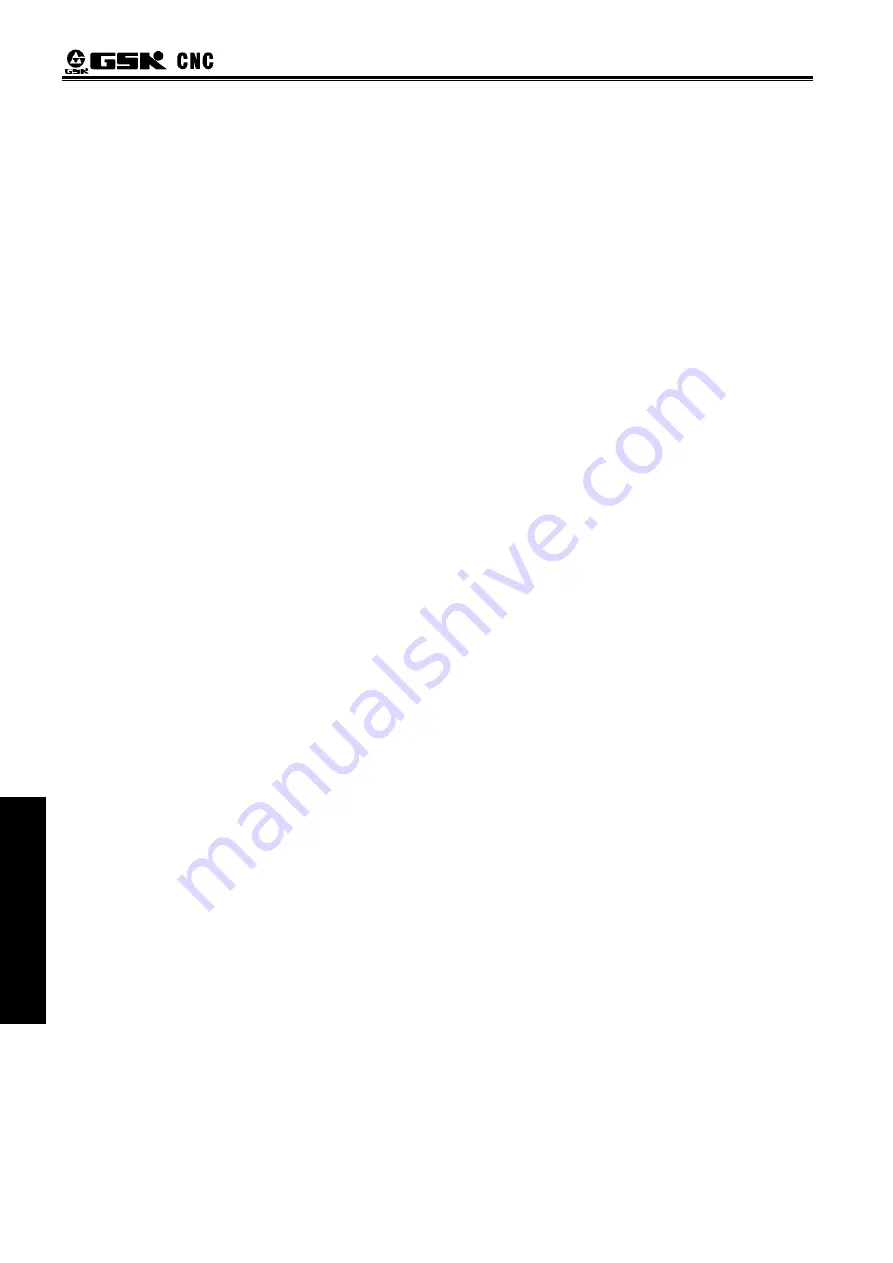
GSK980MDc Milling CNC System User Manual
444
Appendix
a danger. The system has a control of this condition, so when toolcase spinning, the falling or rising
action cannot achieve.
M65 toolcase falls, M66 toolcase raises. If it is not completed:
1: when implementing M65, observe Y1.4 in Ladder->PLC to see whether it is outputted. When
implementing M65, observe Y1.4 in Ladder->PLC to see whether it is outputted. If it is outputted, but
the toolcase does not move, then please check the machine tools electric , the connection to motor
and the motor in good condition or not.
3: If either Y1.4 or Y1.5 has no output, please check the ATC arm is in situ or not. If ATC arm is in
situ, toolcase can not fall because of the falling definitely causes the damage to the ATC arm.
2: If either Y1.4 or Y1.5 has no output, please check the ATC arm is in situ or not, and signal X1.2
is 0 or not. If the signal turns out to be 1 that means the ATC arm is in situ and toolcase actions
forbidden
3: the tool magazine forward and backward keys in 980MDc-V panel can realize the functions of
M65 and M66. To backward and fall down the tool magazine, make sure that toolpot spinning stopped
and the ATC is in situ, or the operation cannot be achieved. If the operations cannot be done even if
the massages mentioned above is ensured, please check according to Step 1 and 2.
Spindle orientation accomplishment
In MDI or AUTO mode, starting M19 stands for spindle orientation accomplished. If M19 cannot be
work out:
1: make sure Y3.0 has an output in Ladder->PLC. If there is an output, please check the servo
spindle is accomplishing the spindle orientation.
2: if there is an alarm when spindle orientating, please check in Ladder->PLC that X5.2 signal is in
position. If it is not in position, please check the machine tools electric or connections to the servo
spindle.
3: if the orient position is not exact, please set the parameter corresponding to the servo spindle.
For details, please see to the operations of the servo spindle.
Start the motor of ATC arm
Before debugging and starting the motor of ATC arm, whether the spindle is in the safe
position or spindle is in the tool change position should be made sure. If the spindle is not
in the safe position, ATC arm will hit against it and be damaged. If there is a tool in the
spindle, first implement spindle orientation function, and make sure that the orientation can
make ATC arm accomplishes clamping the tool, or the tool will be damaged.
The system has a protection mechanism when the ATC arm is started:
1: to let spindle orientate and back to NO.2 reference position, to debug, please set parameter
K11.2 to 0
2: if the current toolcase is fallen, to ensure the tools will not drop, to debug, set K11.4 to 1
3: the ATC arm changes the tool and is back to situ, and if the spindle releasing/clamping tool
detection needed, to debug, please set K11.3 to 1
Conditions permitting, the parameters cannot be changed, but if they changed during the
debugging, please reset them later.
During the debugging, input M68 (tool change motor the 1
st
time catching tool) M69 (tool change
motor the 2
nd
time catching tool) M70 (tool change motor the 3
rd
time catching tool)
1: please check the ATC arm is available and debugging parameter is set correctly when the ATC
arm responds nothing to the start signal.
2: set the parameter, then input M instruction, observe Y2.1 in Ladder->PLC to see whether it
Содержание 980MDc
Страница 19: ...GSK980MDc Milling CNC User Manual XVIII ...
Страница 20: ...1 I Programming Programming Ⅰ ...
Страница 21: ...GSK980MDc Milling CNC System User Manual 2 I Programming ...
Страница 139: ...GSK980MDc Milling CNC System User Manual 120 I Programming ...
Страница 191: ...GSK980MDc Milling CNC System User Manual 172 I Programming ...
Страница 192: ...173 Ⅱ Operation Ⅱ Operation ...
Страница 193: ...GSK980MDc Milling CNC System User Manual 174 Ⅱ Operation ...
Страница 200: ...Chapter 1 Operation Mode and Display 181 Ⅱ Operation ...
Страница 201: ...GSK980MDc Milling CNC System User Manual 182 Ⅱ Operation ...
Страница 249: ...GSK980MDc Milling CNC System User Manual 230 Ⅱ Operation ...
Страница 253: ...GSK980MDc Milling CNC System User Manual 234 Ⅱ Operation ...
Страница 259: ...GSK980MDc Milling CNC System User Manual 240 Ⅱ Operation ...
Страница 265: ...GSK980MDc Milling CNC System User Manual 246 Ⅱ Operation ...
Страница 293: ...GSK980MDc Milling CNC System User Manual 274 Ⅱ Operation ...
Страница 295: ...GSK980MDc Milling CNC System User Manual 276 Ⅱ Operation ...
Страница 319: ...GSK980MDc Milling CNC System User Manual 300 Ⅱ Operation ...
Страница 320: ...301 Ⅲ Installation Ⅲ Installation ...
Страница 321: ...GSK980MDc Milling CNC System User Manual 302 Ⅲ Installation ...
Страница 345: ...GSK980MDc Milling CNC System User Manual 326 Ⅲ Installation ...
Страница 391: ...GSK980MDc Milling CNC System User Manual 372 Ⅲ Installation ...
Страница 392: ...Appendix 373 Appendix Appendix ...
Страница 393: ...GSK980MDc Milling CNC System User Manual 374 Appendix ...
Страница 394: ...Appendix 375 Appendix Appendix 1 Outline Dimension of GSK980MDc L N ...