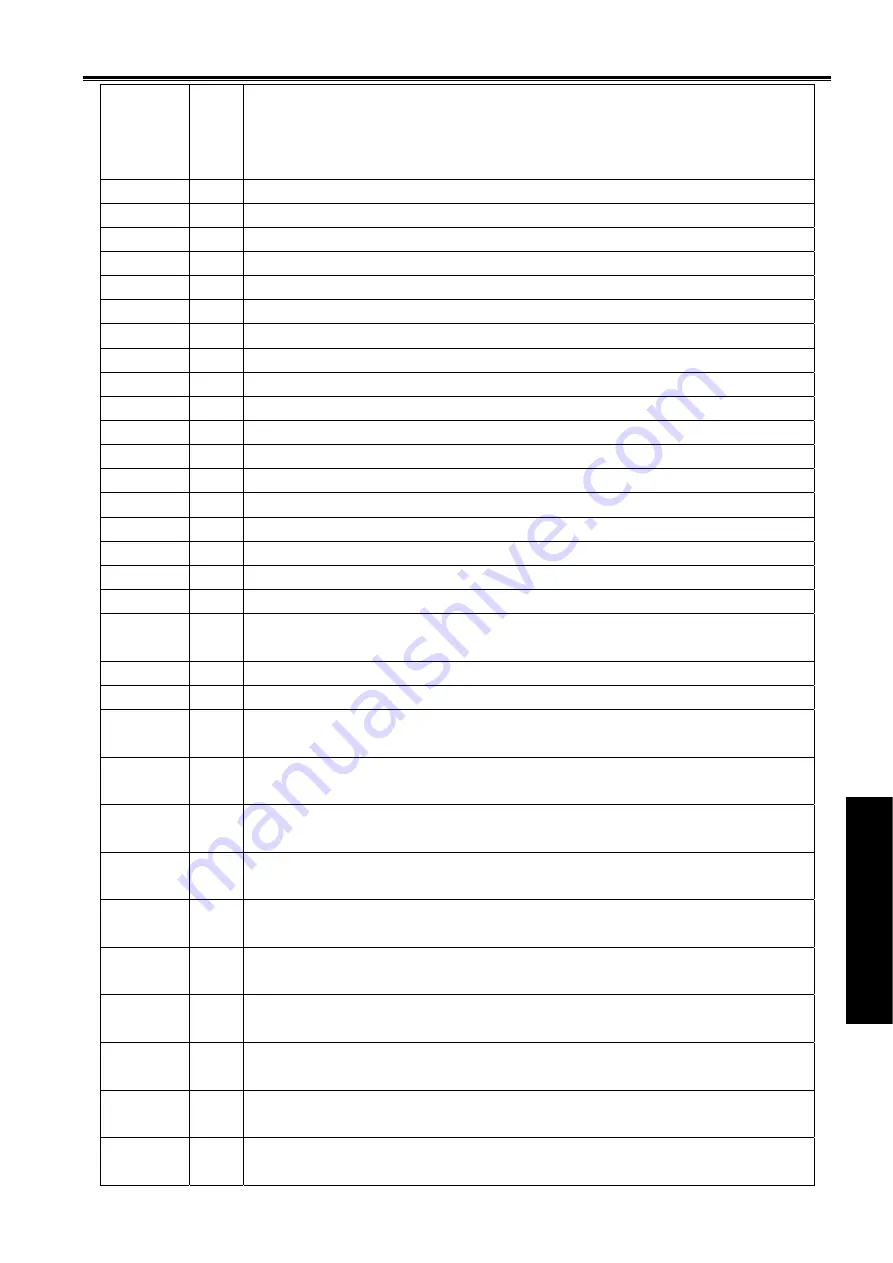
Appendix
393
Appendix
Alarm
No.,
TYPE
CLR
WAY
Alarm Message
213,0
0
U value is less than tool radius
214,0
0
I, J is too small or K is too big, this resule in overcut.
215,0
0
no J or no rectangle for end and start points coincide
216,0 0
no drill (G73
~
G89) for G140~G143 continuous drilling
217,0
0
drill holes can't less than 2
218,0
0
pitch F not specified in G74, G84
219,0
0
drill interval too small in canned cycle
230,0
0
S is 0. Spindle disabled.
231,0
0
S value is over top by rigid tapping
232,0
0
other axis move specified between M29 and G74/G84
233,0
0
G61.0 signal abnormal in rigid tapping
234,0 0
M29
repeated
235,0
0
M29 with G74,G84 in a block disabled in positioning
236,0
0
5th axis for ratory needed before rigid tapping
237,0
0
Specified data in G10 abnormal
238,0
0
P value specified by G10 is not within 0~6
239,0 0
P value specified by G10 is not within 1
~
48
240,0 0 P value is not within 1
~
48 when an additional coordinate system is specified
250,0
0
Cutter compensation C will not be founded, because compensation start
position is different from circle start position
251,0
0
Error programming has led to error operation in C tool compensation
252,0
0
Error programming has led to error end point of arc in C tool compensation
253,0
0
The same coordinate of two adjacent point in the machining track has led to no
effective C tool compensation
254,0
0
Superposition of the centre and start point of the arc has led to no effective C
tool compensation
255,0
0
Superposition of the centre and end point of the arc has led to no effective C tool
compensation
256,0
0
That arc radius beng less than tool nose radius has led to noneffective tool
compensation
257,0
0
Error programming led to no point of intersection between two arcs with the
current tool in C tool compensation
258,0
0
Error programming:G02,G03 is commanded in establishing the C tool
compensation
259,0
0
Error programming:G02,G03 is commanded in cancelling the C tool
compensation with G40
260,0
0
Over cutting has been found in the interference checking for the C tool
compensation
261,0
0
Error programming led to no point of with intersection between the line and arc
the current tool in C tool compensation
262,0
0
Error programming led to no point of intersection between the arc and line with
the current tool in C tool compensation
Содержание 980MDc
Страница 19: ...GSK980MDc Milling CNC User Manual XVIII ...
Страница 20: ...1 I Programming Programming Ⅰ ...
Страница 21: ...GSK980MDc Milling CNC System User Manual 2 I Programming ...
Страница 139: ...GSK980MDc Milling CNC System User Manual 120 I Programming ...
Страница 191: ...GSK980MDc Milling CNC System User Manual 172 I Programming ...
Страница 192: ...173 Ⅱ Operation Ⅱ Operation ...
Страница 193: ...GSK980MDc Milling CNC System User Manual 174 Ⅱ Operation ...
Страница 200: ...Chapter 1 Operation Mode and Display 181 Ⅱ Operation ...
Страница 201: ...GSK980MDc Milling CNC System User Manual 182 Ⅱ Operation ...
Страница 249: ...GSK980MDc Milling CNC System User Manual 230 Ⅱ Operation ...
Страница 253: ...GSK980MDc Milling CNC System User Manual 234 Ⅱ Operation ...
Страница 259: ...GSK980MDc Milling CNC System User Manual 240 Ⅱ Operation ...
Страница 265: ...GSK980MDc Milling CNC System User Manual 246 Ⅱ Operation ...
Страница 293: ...GSK980MDc Milling CNC System User Manual 274 Ⅱ Operation ...
Страница 295: ...GSK980MDc Milling CNC System User Manual 276 Ⅱ Operation ...
Страница 319: ...GSK980MDc Milling CNC System User Manual 300 Ⅱ Operation ...
Страница 320: ...301 Ⅲ Installation Ⅲ Installation ...
Страница 321: ...GSK980MDc Milling CNC System User Manual 302 Ⅲ Installation ...
Страница 345: ...GSK980MDc Milling CNC System User Manual 326 Ⅲ Installation ...
Страница 391: ...GSK980MDc Milling CNC System User Manual 372 Ⅲ Installation ...
Страница 392: ...Appendix 373 Appendix Appendix ...
Страница 393: ...GSK980MDc Milling CNC System User Manual 374 Appendix ...
Страница 394: ...Appendix 375 Appendix Appendix 1 Outline Dimension of GSK980MDc L N ...