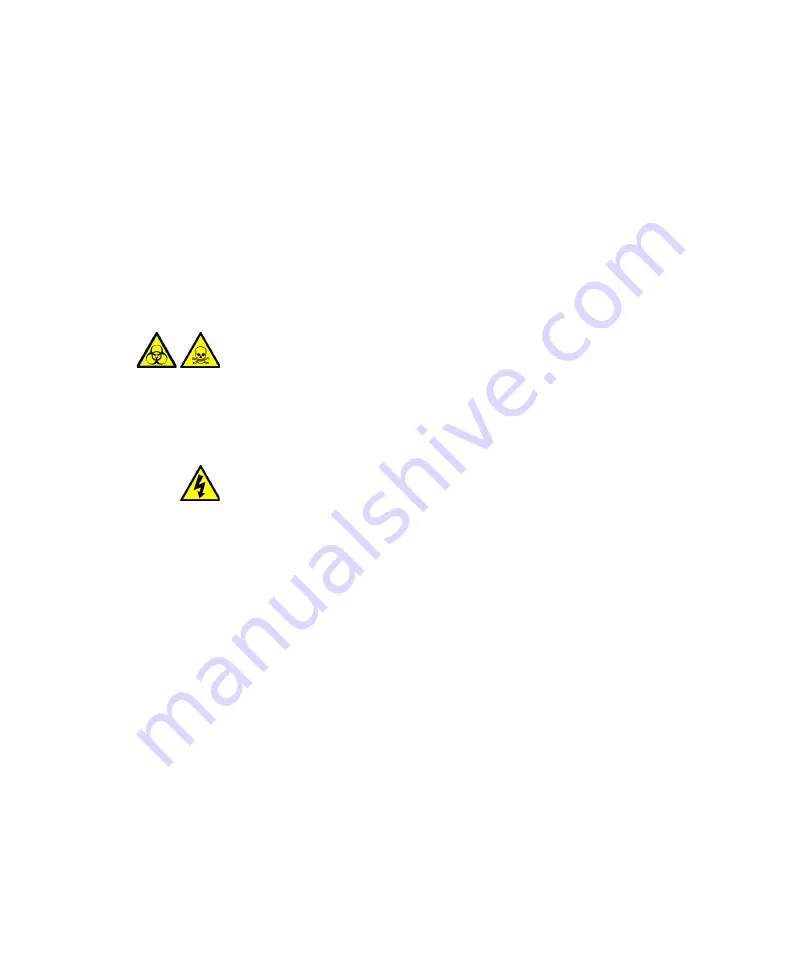
APCI mode
March 14, 2014, 715004387 Rev. B
63
discharge to produce stable reagent ions. Analyte molecules introduced into
the mobile phase react with the reagent ions at atmospheric pressure and
typically become protonated (in the positive ion mode) or deprotonated (in the
negative ion mode). The sample and reagent ions then pass through the
sample cone and into the mass spectrometer.
Installing the IonSABRE II probe
Required materials
•
Chemical-resistant, powder-free gloves
•
Sharp knife or PEEK tubing cutter
To install the IonSABRE II probe:
1. Prepare the instrument for working on the source (see
).
2. With the probe label facing toward you, carefully slide the IonSABRE II
probe into the hole in the probe adjuster assembly, ensuring that the
probe location dowel aligns with the probe adjuster assembly location
hole.
Warning:
To avoid personal contamination with biohazards or
toxic materials, and to avoid spreading contamination to
uncontaminated surfaces, wear clean, chemical-resistant,
powder-free gloves while performing this procedure. The LC
system connections, IonSABRE II probe, and source can be
contaminated.
Warning:
To avoid electric shock, before beginning this procedure,
prepare the instrument according to the procedure on
,
“Preparing the instrument for operations on or inside its source”
.
Summary of Contents for Xevo TQD
Page 2: ...ii March 14 2014 715004387 Rev B...
Page 22: ...xxii March 14 2014 715004387 Rev B...
Page 56: ...2 Preparing for Operation 56 March 14 2014 715004387 Rev B...
Page 200: ...4 Maintenance Procedures 200 March 14 2014 715004387 Rev B...
Page 216: ...A Safety Advisories 216 March 14 2014 715004387 Rev B...
Page 242: ...B External Connections 242 March 14 2014 715004387 Rev B...
Page 246: ...C Materials of Construction and Compliant Solvents 246 March 14 2014 715004387 Rev B...