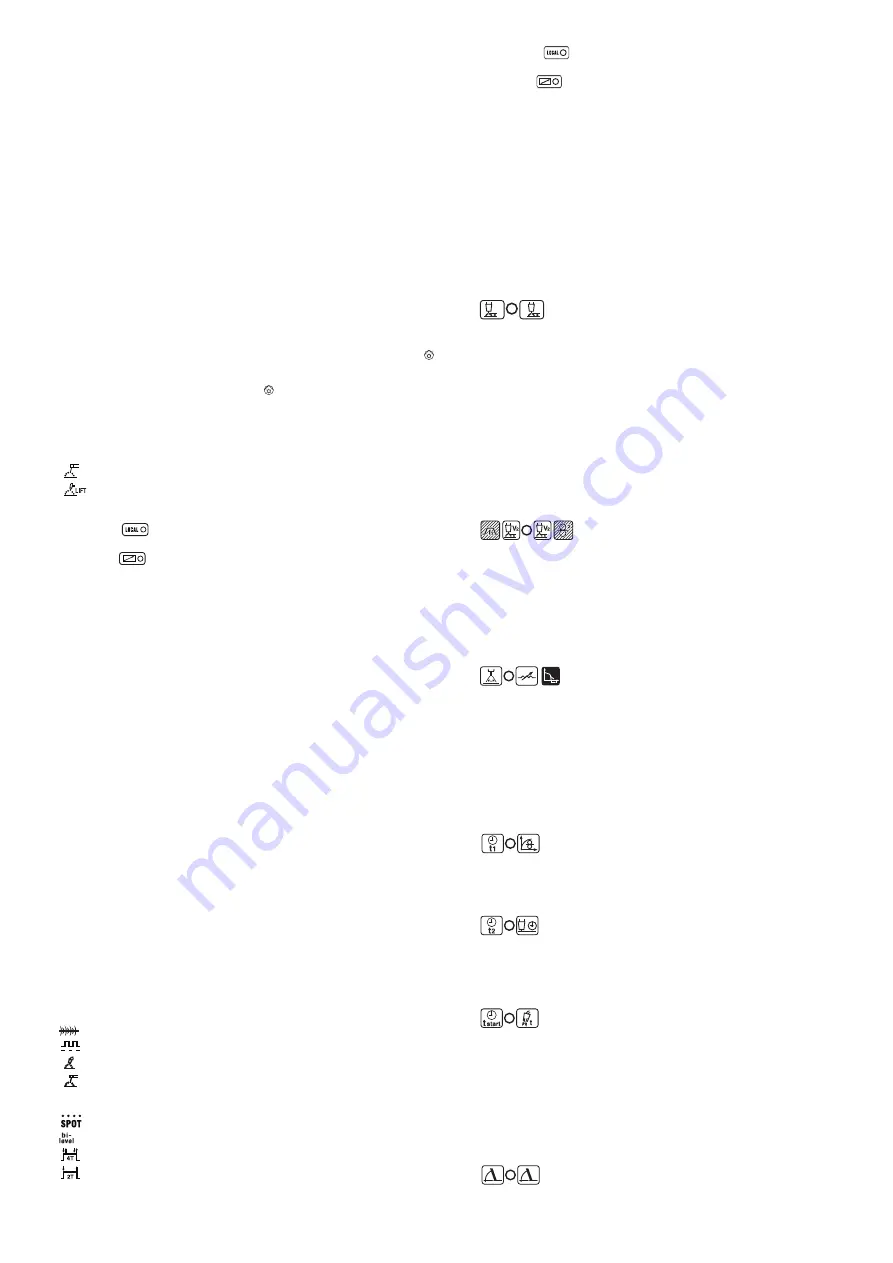
6-
14p connector for control cable towards the generator.
7-
Fast positive socket (+) for welding power cable towards the generator.
8-
Gas tube connection (bottle).
9-
Fast links for connecting tubes for the delivery and return of water.
4.2 WELDING MACHINE CONTROL PANEL (FIG. D)
The control panel is available (in other words, the controls and signals are active) only if
the generator is NOT CONNECTED to the wire feeder. Otherwise, the control modes
automatically pass to the wire feeding panel, and the word "feed" will be appear on the
source display
(4)
.
(machine output is blocked). An alarm message will appear
on the display
(4)
.
The machine will automatically be restored when the cause for the alarm has
ceased.
3- LED phase
of the power line is missing.
4- 4-digit alphanumeric display .
Directions:
a)
Welding current in amperes.
- AL 1:
intervention for thermal protection of magnetic components.
6- Key for selecting welding procedure
-
: "MMA" coated electrode.
-
: TIG (Direct Current) with contact arc inserted .
- With LED
on, controls are activated on the welding machine control
panel.
- With LED
on, adjustment can only be made using the remote control and
in detail as follows:
a) single potentiometer control
:
replaces the encoder knob
(14)
function
.
b) dual potentiometer control:
replaces the functions of encoder knobs
(14)
and
(13).
c) pedal control
:
replaces the encoder knob
(14)
function.
1- LED indicating alarm
NOTE: It is only possible to select REMOTE if a remote control device is actually
connected to its socket.
2- LED indicating power present at output
(output on).
The display (4) will show an alarm message.
The value shown is the set value if the welding machine is loadless, while it is the
actual value during operation.
b)
an alarm message with the following code:
7- Key for switching on remote control.
- With LED
on, the controls on the welding machine panel are activated.
- With LED
on, adjustment can only be carried out by remote control:
a) single potentiometer control:
replaces the encoder
(5)
function
.
b) dual potentiometer control:
replaces the encoder
(5)
and potentiometer
(8)
function
.
c) pedal control:
replaces the encoder
(5)
function and in TIG is used to switch the
arc on and off as an alternative to the torch button.
NOTE: Selecting ”REMOTE” is only possible if a remote control device is actually
connected to its socket.
8- Potentiometer for adjusting arc functions.
This has different functions depending
on the selected procedure:
- MMA:
adjusts ”Arc Force” dynamic overcurrent (adjustment 0-100%) with a brief
indication on the display of the percentage increase in the value of the pre-
selected welding current. This adjustment is used to improve welding fluidity
and prevent the electrode from sticking to the piece being welded.
- TIG:
adjusts the welding current downslope (adjustment 0-100%) when the torch
button is released (SLOPE DOWN), with a brief indication on the display.
This adjustment is used to prevent the formation of craters at the end of
welding.
NOTE: ”POST-GAS” is adjusted automatically, using a time that is
proportional to the welding current setting.
4.3 WIRE FEEDER CONTROL PANEL (FIG. E)
1- Alarm indicator LED (machine output blocked).
Reset is automatic when the cause of alarm ceases.
Alarm messages shown on displays
(15)
and
(16)
:
- from
AL1
to
AL5
: see power source control panel (par. 4.2).
-
AL7
: safeguard triggered due to overcurrent in MIG/MAG welding.
-
AL8
and
AL9
: fault in serial data transmission line.
-
2- Indicator LED for PRESENCE OF POWER IN TORCH OR ON ELECTRODE.
3- Indicator LED for PROGRAMMING WELDING MACHINE.
4- Key for recalling (LOAD) customised welding programs
(see par. 4.4.2.4).
5- Key for storing (STORE) customised welding programs
(see par. 4.4.2.3).
6- Key for selecting welding program and 2-digit display.
If the key is pressed repeatedly, the display will show the numbers between “0” and
“36”. Each number between “1” and “36” is associated with a synergic welding
program
(see TAB.4)
while the number “0” is associated with manual welding
machine operation, when all parameters can be set by the operator.
7- Key for selecting welding procedure.
When the key is pressed the LED lights up corresponding to the welding procedure
to be used:
: MIG/MAG in PULSE ARC.
: MIG/MAG in SHORT/SPRAY ARC.
: MMA electrode.
8- Key for selecting control mode for MIG/MAG torch button.
When the key is pressed the LED lights up corresponding to:
: MIG/MAG spot welding operation (SPOT).
: 4-stroke operation, ON-OFF with button released.
: 2-stroke operation, ON-OFF with button pressed.
9- Key for switching on remote control
.
(only MMA)
(only MMA)
10- Key for selecting welding parameters.
Pressing the key repeatedly will light up one of the LED's from (10a) to (10h)
associated with a specific parameter. The setting for each activated parameter is
made using the knob (13) and is shown on the display (15). While making these
settings knob (14) adjusts the value of the main welding level shown on the display
(16), either current or wire feed rate (see the explanation at point (14)).
Knob (14) will only allow adjustment of the secondary level if LED (10b) is ON (see
the description of LED (10b)).
Note: Parameters that cannot be modified by the operator, depending on whether
you are working with a synergy programme or in manual mode (“PRG 0”), are
automatically excluded from the selection; the corresponding LED will not light up.
-
AL 1
: primary circuit thermal safeguard triggered
-
AL 2
: secondary circuit thermal safeguard triggered.
10a-
Arc length (main level).
-
AL 3
: overvoltage safeguard on power line triggered.
This parameter is automatically displayed during MIG/MAG welding operations
-
AL 4
: undervoltage safeguard on power line triggered.
and indicates the actual arc voltage (LED (15a) ON).
-
AL 5
: safeguard triggered due to insufficient pressure in the water-cooled circuit
When setting a MIG/MAG Pulse arc synergic programme this parameter is used to
in the torch, if the cooling system is connected to the power supply outlet ( )
adjust the correction to be made to arc length calculated in synergy (range from -
available on the welding machine. WARNING: In this case it is necessary to
5% to +5%) (LED (15c) ON).
switch off the welding machine to restore the system.
In the same mode, setting the bi-level, pulse-on-pulse or Tstart function will cause
N.B. When the power supply outlet ( ) for the cooling system is not used
the parameter to take the value of arc length correction at the main welding level,
insert the corresponding plug supplied with the welding machine.
calculated in synergy as above (range from -5% to +5%) (LED (15c) ON).
-
AL 11
: safeguard triggered due to phase failure in the power supply line (see LED (
When setting a MIG/MAG Short arc synergic programme this parameter is used to
3)), or triggering of thermal safeguard for magnetic components.
adjust the correction to be made to arc length calculated in synergy (range from -
5- Encoder control knob.
5% to +5%) (LED (15c) ON).
Used to regulate the welding current (from 10A minimum to 350A maximum).
In the same mode, setting the bi-level function will cause the parameter to take the
value of arc length correction at the main welding level, calculated in synergy as
above (range from -5% to +5%) (LED (15c) ON).
Also in MIG/MAG Short arc mode, manual programming (“PRG 0”) is used to set
the actual arc voltage (range 10-40) (LED (15a) on)
In the same mode, setting the bi-level function will cause the parameter to take the
value of actual arc voltage at the main welding level (range 10-40) (LED (15a) ON).
10b-
Arc length (secondary level).
In MIG/MAG pulse arc mode, setting the bi-level, pulse-on-pulse or Tstart function
makes it possible to adjust current I2 (using knob (14)) and arc length correction
(using knob (13)) for the secondary welding level, calculated in synergy (range
from -5% to +5%) (LED (15c) ON).
In MIG/MAG short arc synergic programmes, setting the bi-level function makes it
possible to adjust wire feed rate (using knob (14)) and arc length correction (using
knob (13)) for the secondary welding level, calculated in synergy (range from -5%
to +5%) (LED (15c) ON).
If manual programming is selected (“PRG 0”) with the bi-level function it is possible
to adjust wire feed rate (using knob (14)) and actual arc voltage (using knob (13))
for the secondary welding level, (range 10-40) (LED (15a) ON).
10c-
MIG/MAG Pulse arc pinch-off, MIG/MAG short arc electronic
reactance or MMA Arc force.
In MIG/MAG pulse arc mode the parameter determines arc pinch-off. The higher
the value the more concentrated will be the arc during welding. In a welding mode
using two current levels (bi-level, pulse-on-pulse or Tstart) arc pinch-off has the
same setting for both levels.
In MIG/MAG manual mode (“PRG 0”) the parameter is used to adjust electronic
reactance (adjustment 20-80% and LED (15c) ON). A higher value will cause a
hotter weld pool. In bi-level mode electronic reactance has the same setting for
both levels.
In MMA electrode mode, the parameter takes on the meaning “Arc force” allowing
a dynamic overcurrent setting (0-100% adjustment and LED (15c) ON). During
MMA welding the display (15) shows the actual arc voltage (LED (15a) on), LED
(10c) also stays on to allow Arc force adjustment even during welding.
10d-
Main level time in MIG/MAG Pulse-on-Pulse mode or wire feed
rate slope up.
AL11
: safeguard triggered due to phase failure in the power supply line
,
or
In MIG/MAG Pulse-on-pulse mode this parameter can be used to regulate main
triggering of thermal safeguard for magnetic components.
welding current time (regulation 0.1-10 seconds and LED (15b) ON).
In manual mode (“PRG 0”) it is used to adjust wire feed rate as welding starts so as
to optimise arc strike (1-100% adjustment and LED (15c) ON).
10e-
Secondary level time in MIG/MAG Pulse-on-Pulse mode or wire
burn-back when welding stops.
In MIG/MAG Pulse-on-pulse mode this parameter can be used to regulate
secondary welding current time (regulation 0.1-10 seconds and LED (15b) ON).
In MIG-MAG short arc manual mode (“PRG 0”) it takes the value of burn-back time.
That is, it is used to prevent the wire sticking to the piece when welding stops
(adjustment 0.01-1 seconds and LED (15b) ON).
10f-
MIG/MAG Pulse arc start current time (TStart) or MIG/MAG Short
: MIG/MAG in PULSE ON PULSE.
arc Post-gas time.
In MIG-MAG Pulse arc 2-STROKE mode it is used to regulate start current time
(Tstart). If the parameter is set to zero the function is disabled, while with any other
setting greater than zero (adjustment 0.1-3 seconds) it is possible to select LED
(10b) to regulate the arc voltage correction and start current value (secondary
level). The start current can have either a higher or lower setting than the main
welding current; a higher start current is very useful especially when welding
aluminium and its alloys, and this actually makes it possible to heat the piece more
quickly (“Hot start”).
In any MIG-MAG Short arc mode the parameter corresponds to “Post-gas” time,
: MIG/MAG bi-level operation.
making it possible to adjust the time for which protective gas will flow after welding
stops (adjustment 0.1-10 seconds and LED (15c) ON).
10g-
Welding current SLOPE DOWN.
This is enabled only and exclusively when using MIG/MAG Pulse arc or Short arc
- 6 -