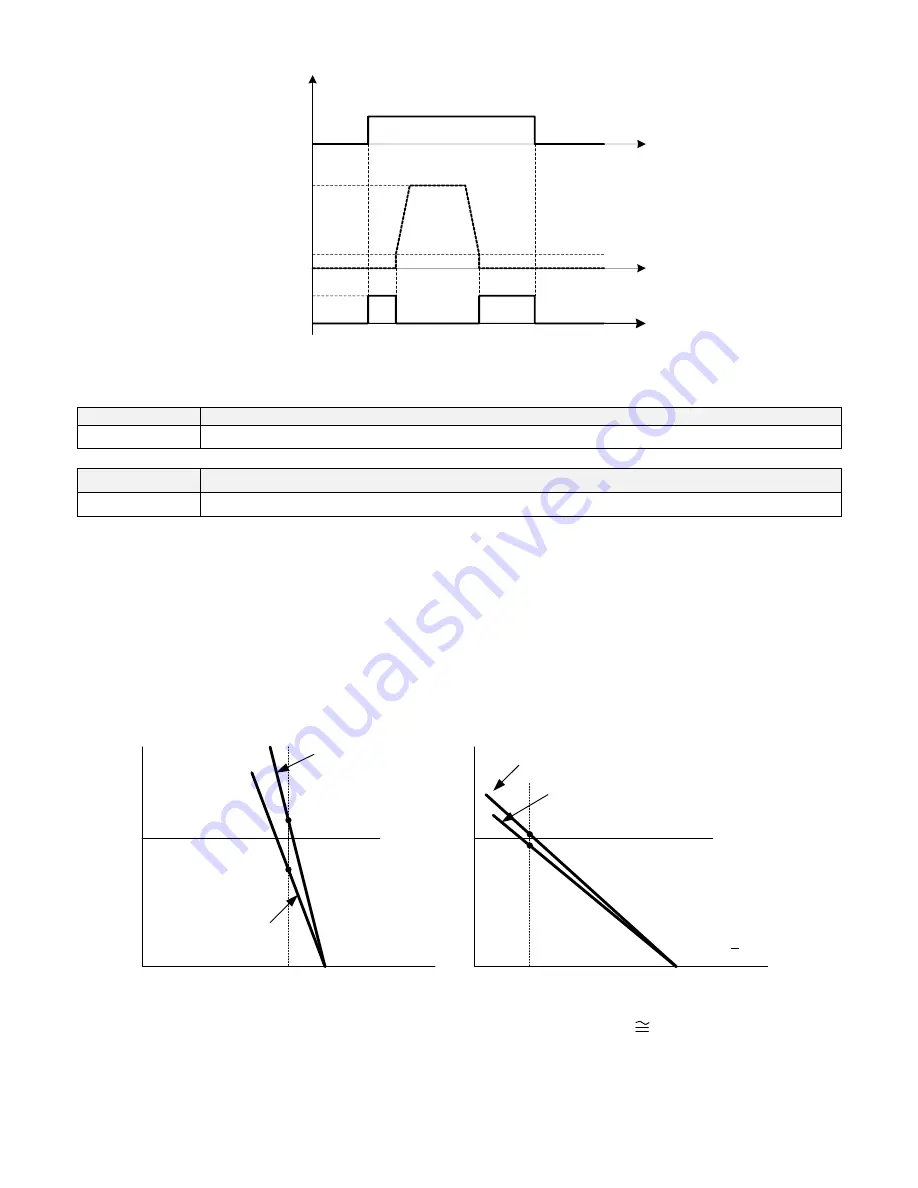
4-243
R
u
n
c
o
m
m
a
n
d
F
r
e
q
u
e
n
c
y
R
e
f
e
r
e
n
c
e
D
C
I
n
j
e
c
t
i
o
n
B
r
a
k
i
n
g
(
2
0
%
m
a
x
.
)
Z
e
r
o
s
p
e
e
d
l
e
v
e
l
(
T
H
e
l
a
r
g
e
r
o
f
0
1
-
0
8
o
r
0
7
-
0
6
)
t
t
t
Figure 4.4.97 Zero-speed braking operation
11-52
Droop control level
Range
0.0~100.0%
11-53
Droop control delay
Range
0.00~2.00 Sec
Droop control is used for load balancing when using two standard AC motors to drive the load in applications such
as cranes and conveyors. When droop control is active the inverter reduces the speed when the torque reference
rises and increases the speed when the torque reference drops.
(a) Load balancing using the standard AC motors.
The load torque of motor A, TA > The load torque of motor B ,TB.
(b) Load balancing using high slippage AC motors.
The load torque of motor A ,TA is very close to the load torque of motor B ,TB.
Motor A
,
s torque characteristics
Motor B
,
s torque characteristics
T
A
T
B
T
A
-T
B
~ 0
Speed
Reference
Speed
Load torque
Torque
Torque
Motor A
,
s torque
characteristics
Load torque
Motor B
,
s torque
characteristics
T
A
-T
B
> > 0
Reference
Speed
Speed
(a) T
A
> T
B
(b) T
A
T
B
- Droop function can be used to approximate the characteristic of a high slippage motor. Set 11-52 to the
percentage of the speed reduction that amounts to 100% of motor torque based on the maximum frequency
(01-02).