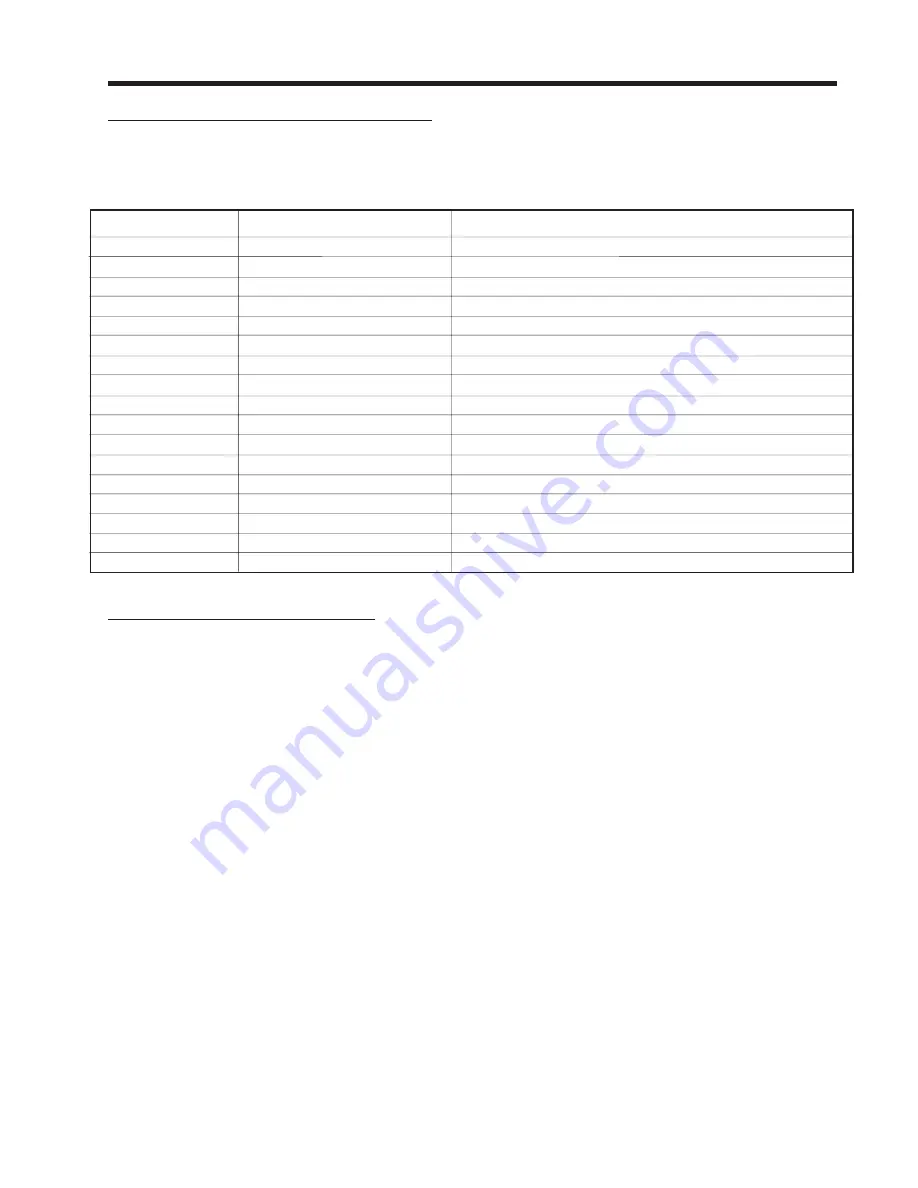
B-7
1020NFM-1D
Appendix
Navigating Through the Installation Menu
After accessing the Installation Menu, you can begin to setup your flowmeter according to the instruc-
tions in this manual. The chart below shows the PC keyboard equivalents to the 1010 keypad keys
while you are in the menu.
Terminal Mode Menu Commands
In addition to Menu, the following commands (followed by the <ENT> key) can be used to control the
flowmeter while in Terminal Mode.
Note that “n” refers to the flowmeter Channel number. For a dual channel Arithmetic site (Ch1 + Ch2
or Ch1 – Ch2) the virtual Channel is number 3.
Logger
– Invokes the download of all data stored in the datalogger. Note that the datalogger data is
not erased from the flowmeter memory when it is downloaded. It is recommended to capture this
information into a file with a “csv” extension, which can be easily imported into MS EXCEL.
SITE
– Invokes a full site download for a single channel or multi-path 1010 flowmeter.
SITE “n”
– Invokes a site download for channel “n”, where “n” = the Channel # (1, 2, 3, 4, etc.).
DP “n”
– Commands the flowmeter to download the digitized receive signal data for Channel or Path
“n”.
CLRTOT
– Clears the Totalizer for a single channel or multi-path 1010 flowmeter.
CLRTOT “n”
– Clears the Totalizer for Channel “n” of a multi-channel flowmeter.
Lf on
– Turns on the Line Feed at the end of any text string sent by the flowmeter.
Lf off
– Turns off the Line Feed at the end of any text string sent by the flowmeter.
?
– Provides a list of available Terminal Mode meter commands.
1010 Keyboard
PC Keyboard
Description
<Up Arrow>
<Up Arrow>
Move up 1 menu cell (or Flow Display screen)
<Down Arrow>
<Down Arrow>
Move down 1 menu cell (or Flow Display screen)
<Right Arrow>
<Right Arrow>
Move right 1 menu cell (or Flow Display screen)
<Left Arrow>
<Left Arrow>
Move left 1 menu cell (or Flow Display screen)
<Menu>
^L (Cntrl L)
Toggle between Menu and Flow Display
<Datalog>
^D (Cntrl D)
Generate Datalogger report
<CLR>
<Backspace> or <DEL>
Deselect list selection
<ALT+Up Arrow>
^U (Cntrl U)
Logger Display Page Advance
<+/-> (chg sign)
| (bar, shift + backslash)
Change numeric sign. Can also type (-) key.
<ENT>
<Carriage Return>
Enter Key
Digits
Digits
Numerals zero through 9
/
/
Divide by
X
* (upper case 8)
Multiply by
+
+
Plus
-
-
Minus
=
=
Equals
.
.
Decimal Point
Summary of Contents for SITRANS FUS1020
Page 3: ......
Page 206: ......
Page 207: ......
Page 208: ......
Page 209: ......
Page 210: ......
Page 211: ......
Page 212: ......
Page 213: ......
Page 214: ......
Page 215: ......
Page 216: ......
Page 217: ......
Page 218: ......
Page 219: ......
Page 220: ......
Page 221: ...21614 C ...
Page 222: ...21614 C ...
Page 223: ...990TNHM 8 OUTLINE DIMENSIONS TRANSDUCERS TRACKS DEDICATED HYBRID MODE 21614 C ...
Page 224: ...1011FTP 8 21614 C ...
Page 225: ...1011FTNF 8 21614 C ...
Page 226: ...21614 C PFA DFT FLOWTUBE INSTALLATION OUTLINE 992DFTP T 8 ...
Page 227: ...INSTALLATION OUTLINE 992 SERIES EXTENDED FLOWTUBE 21614 C 992DFTN 8 ...
Page 228: ......