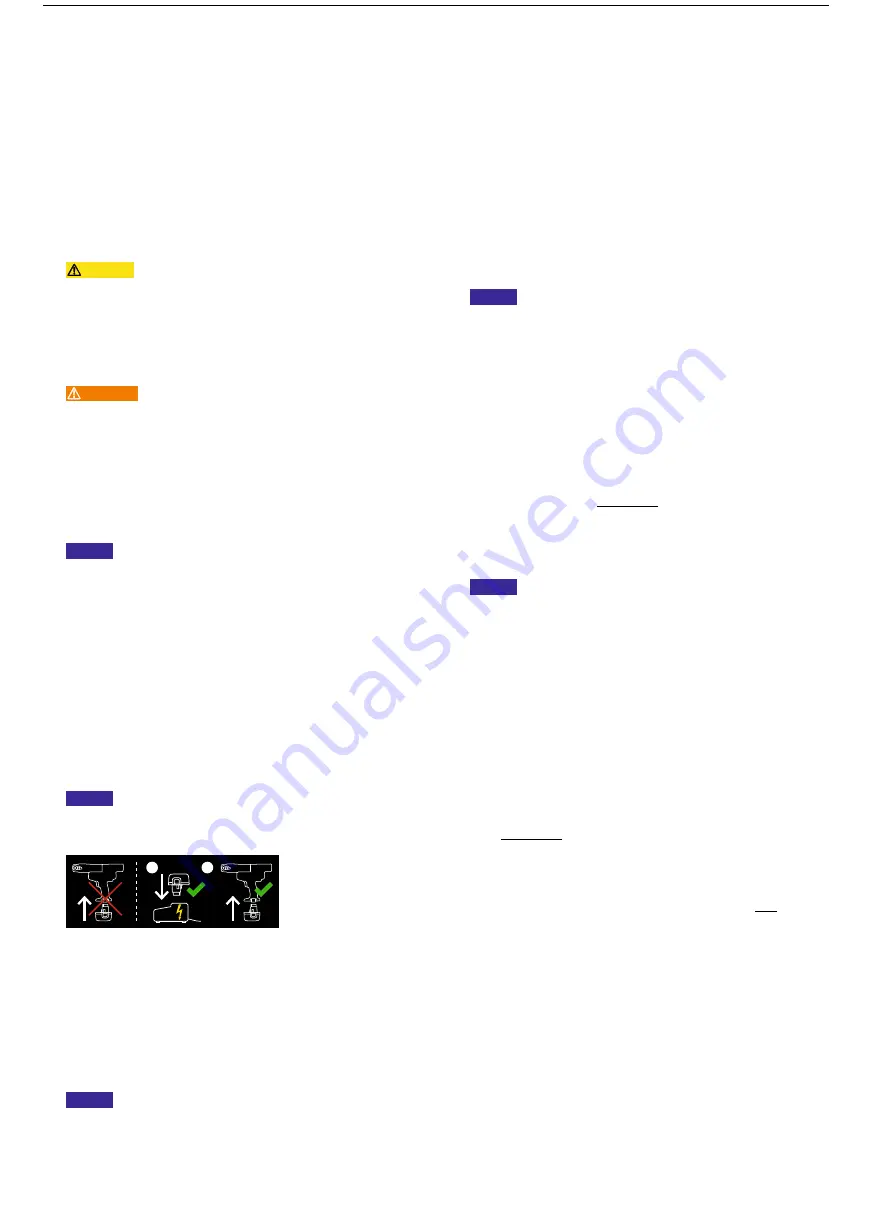
REMS battery Li-Ion
18 V, 2.6 Ah
0.63 kg (1.4 lb)
18 V, 3.5 Ah
0.64 kg (1.4 lb)
1RLVHLQIRUPDWLRQ
Emission at
workplace
82 dB (A)
90 dB (A)
90 dB (A)
Sound pressure level L
pA
= 86 dB
Sound power level
L
wA
= 97 dB
Uncertainty
K = 3 dB
1.8. Vibrations
Curvo
Curvo 50
Akku-Curvo
Weighted
effective
value of acceleration 2.5 m/s²
2.5 m/s²
2.5 m/s²
The indicated weighted effective value of acceleration has been measured
against standard test procedures and can be used by way of comparison with
another device. The indicated weighted effec ive value of acceleration can also
be used as a preliminary evaluation of the exposure.
CAUTION
The indicated weighted effective value of acceleration can differ during opera-
tion from the indicated value, dependent on the manner in which he device is
used. Dependent upon the actual conditions of use (periodic duty) it may be
necessary to establish safety precautions for the protection of the operator.
2. Preparations for Use
2.1. Electrical connection
WARNING
3D\DWWHQWLRQWRPDLQVYROWDJH
Check whether the voltage speci
¿
ed on the
rating plate matches the mains voltage before connecting the drive machine
or the rapid charger. Only operate the electrical device on the mains via a 30 mA
fault current protection device (FI switch) on building sites or similar types of
installation.
The battery and spare batteries delivered with the REMS Akku-Curvo are not
charged. Charge the batteries before using for the
¿
rst ime. Only use the REMS
rapid charger (Art. No. 571560) for charging.
Rechargeable
batteries
NOTICE
Always hold the battery upright when inser ing it in the drive unit or the rapid
charger. If inserted at an angle it can cause damage to the contacts and result
in a short circuit which damages the battery.
Total discharging by undervoltage
The Li-Ion batteries may not drop below a minimum voltage because otherwise
the battery could be damaged by "total discharge". The cells of the REMS Li-Ion
battery are delivered pre-charged to approx. 40 %. Therefore the Li-Ion batteries
must be charged before use and recharged regularly. Failure to observe this
regula ion of the cell manufacturer can lead to damage to the Li-Ion battery by
total discharging.
Total discharging due to storage
If a relatively low charged Li-Ion battery is stored, self discharging can lead to
total discharge damage of the battery after longer storage. Li-Ion batteries must
therefore be charged before storing and recharged every six months at the
latest and charged again before use.
NOTICE
Charge the battery before use. Recharge Li-Ion batteries regularly to avoid
WKHLUWRWDOGLVFKDUJH7KHUHFKDUJHDEOHEDWWHU\ZLOOEHGDPDJHGE\WRWDO
discharge.
1
2
Only use a REMS rapid charger for charging. New Li-Ion batteries and Li-Ion
batteries which have not been used for a long time only reach full capacity after
several charges. Non-rechargeable batteries may not be charged.
5DSLGFKDUJHU/L,RQ1L&G$UW1R
The green control lamp lights steadily when the mains plug is plugged in. If the
battery is inserted into the rapid charger the green control lamp
À
ashes and
the battery is charged. Charging of the battery is completed when the green
control lamp lights steadily. If the red control lamp
À
ashes, the battery is defec-
tive. If the red control lamp comes on and remains on, this indicates that the
temperature of the rapid charger and / or he battery is outside the permissible
range of 0°C to +40°C.
NOTICE
The rapid chargers are not suitable for using outdoors. Non-rechargeable
EDWWHULHVPD\QRWEHFKDUJHG7KH1L&GDQG/L,RQEDWWHULHVFDQQRWEH
LQWHUFKDQJHGLQWKHGULYHPDFKLQH
2.2. Selecting the bending tools
5(06&XUYR5(06$NNX&XUYR
Put a bending former (1) (Fig. 1) corresponding to the pipe size onto the square
(2). The mounting is designed such that the bending former can only be fully
¿
tted in one direction. Place in readiness he back former (3) sui table for the
pipe size and the insert bolt (4).
5(06&XUYR±
Put a bending former (1) (Fig. 1) corresponding to the pipe size onto the square
(12). The mounting is designed such that the bending former can only be fully
¿
tted in one direction. Place in readiness the back former (3) sui table for the
pipe size and the insert bolt (4). Insert the appropriate sized back former (3),
the support (11) and the insert bolt (4).
5(06&XUYR±
Remove adaptor block (12) and replace with adaptor block (14) into the drive
unit. Put a bending former (1) (Fig. 1) corresponding to the pipe size onto the
square (14). The moun ing is designed such that the bending former can only
be fully
¿
tted in one direction. Insert the appropriate sized back former (3), the
support (13) and the insert bolt (4).
NOTICE
:KHQXVLQJWKH5(06&XUYRWKHVXSSRUWDQGUHVSHFWLYHO\
VKRXOGEHDWWDFKHGDERYHWKHEHQGLQJDQGEDFNIRUPHUVIRUDOOVL]HV
8SWRDQGLQFOXGLQJVL]HV5ô´5WKHVXSSRUWVKRXOGDOVR
EHDWWDFKHGEHORZ7KLVLVPRXQWHGRQRQHVLGHRQWKHDGDSWRUEORFN
FROODUDQGRQWKHRWKHUVLGHZLWKWKHORFDWLQJSLQLQWKHRXWHUPRVW
ERUHKROHRIWKHVXSSRUWPDUNHGRXWLQWKHKRXVLQJVHH
7KHGULYHXQLWJHWVGDPDJHGZKHQEHQGLQJZLWKRXWWKLVVXSSRUW
3. Operation
3.1. Working procedure
Turn/slide setting ring/slide (7) to »L« (reverse). Press inching switch (8) while
gripping the motor handle (9) at the same time. The bending former turns
clockwise into its starting position in which the slipping clutch is effective.
Release the inching switch
LPPHGLDWHO\
. Do not put unnecessary load on the
clutch. Turn/slide setting ring/slide (7) to »R« (forward). Place pipe into bending
former so that the pipe end projects at least 10 mm beyond the driver (10).
With the pipe sizes 22 to 50 mm, the pipe must be pressed into the radius of
the bending former. Lower the insert bolt (4) through the matching back former
(3) and into the corresponding hole bored in the machine.
NOTICE
:KHQXVLQJWKH5(06&XUYRWKHVXSSRUWDQGUHVSHFWLYHO\
VKRXOGEHDWWDFKHGDERYHWKHEHQGLQJDQGEDFNIRUPHUVIRUDOOVL]HV
8SWRDQGLQFOXGLQJVL]HV5ô´5WKHVXSSRUWVKRXOGDOVR
EHDWWDFKHGEHORZ7KLVLVPRXQWHGRQRQHVLGHRQWKHDGDSWRUEORFN
FROODUDQGRQWKHRWKHUVLGHZLWKWKHORFDWLQJSLQLQWKHRXWHUPRVW
ERUHKROHRIWKHVXSSRUWPDUNHGRXWLQWKHKRXVLQJVHH
7KHGULYHXQLWJHWVGDPDJHGZKHQEHQGLQJZLWKRXWWKLVVXSSRUW
Ensure here that the insert bolt (4) for the sizes up to 22 mm (¾”) goes into the
left-hand locating hole (5) and for larger sizes into the right-hand hole (6).
Operate the inching switch (8) to bend the pipe. Towards the end of the required
bend, only press the switch lightly, so that the
¿
nal point is approached slowly
and thereby precisely. A scale is provided on each bending former, together
with the mark on the back former, ensures precise manufacture of arcs of up
to 180° / Curvo 50 up to 90°. Be aware that various materials spring back
differently. If a 180° bend / Curvo 50: 90° bend is produced and reaches the
end position, the slipping clutch comes into action again. Release the inching
switch
LPPHGLDWHO\
. Turn/slide setting ring/slide (7) to »L« (reverse). Allow the
bending former to run back a few deg rees until the pipe is unclamped by light
pressure on he inching switch (8). Pull out he insert bolt (4) and remove the
bent pipe. When bending on site, the bending former too can be taken off for
easier removal of the bent pipe.
Only allow the bending former to return to its starting position
after
removal of
the pipe, as otherwise the produced bend might be damaged. While bending
stainless steel pipes of press
¿
tting systems one must pay attention that the
mark at the pipe caused by the driver (10) does not lie in the sealing area of
the pressing joint.
3.2. Bending to size
If a bend is required at a certain point on the pipe, a lenght correction must be
made to suit the pipe size. For a 90° bend, the correction dimension X given
in Fig. 2 must be taken into account. The set dimension L must be reduced by
the amount X here. If the dimension L should be 400 mm for the pipe size 22,
the dimension line must be made on the pipe at 320 mm. This line is then – as
shown in Fig. 2 – to be aligned with the 0-mark on he bending former.
8QLWVXSSRUW5(06&XUYR5(06$NNX&XUYR
Vertically adjustable unit supports on tripod (Art. No. 586100) and for moun ing
on the work bench (Art. No. 586150) available as accessories.
3.4. Bending lubricant
REMS bending spray (Art. No. 140120) ensures a continuous
¿
lm of lubricant
for reduced force and even bending. High pressure-resistant, acid-free Without
HFC and therefore not harmful to the ozone layer.
g
g