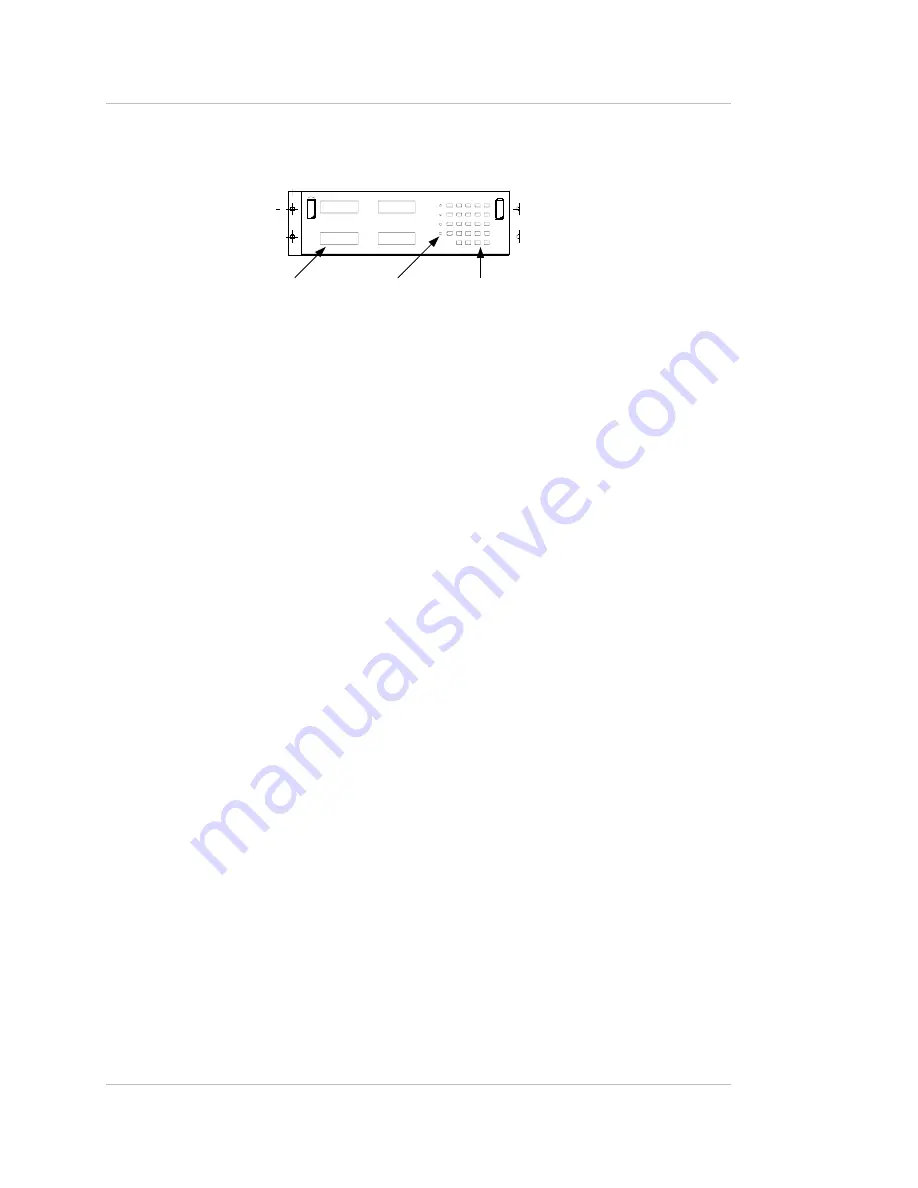
Installation
28
W-4510 Weigh Scale Technical Reference Manual
Access keys and indicators
Figure 11: Rack mount displays
The Pro Pac can communicate with up to four field units. Each display window represents a
different field unit with labels A, B, C, and D. If one or more field units connect to a rack
mount unit, select the desired field unit by pressing the key with the corresponding letter. A
red indicator lights up for the active display window.
Display
windows
Indicator
lights
Numeric keypad
Summary of Contents for W-4510
Page 9: ...Preface viii W 4510 Weigh Scale Technical Reference Manual Notes...
Page 15: ...Preface xiv W 4510 Weigh Scale Technical Reference Manual Notes...
Page 17: ...Preface xvi W 4510 Weigh Scale Technical Reference Manual Notes...
Page 29: ...Introduction 12 W 4510 Weigh Scale Technical Reference Manual Notes...
Page 125: ...Calibration 108 W 4510 Weigh Scale Technical Reference Manual Notes...
Page 145: ...Diagnostics and repair 128 W 4510 Weigh Scale Technical Reference Manual Notes...
Page 155: ...Appendix I Parameter blocks 138 W 4510 Weigh Scale Technical Reference Manual Notes...