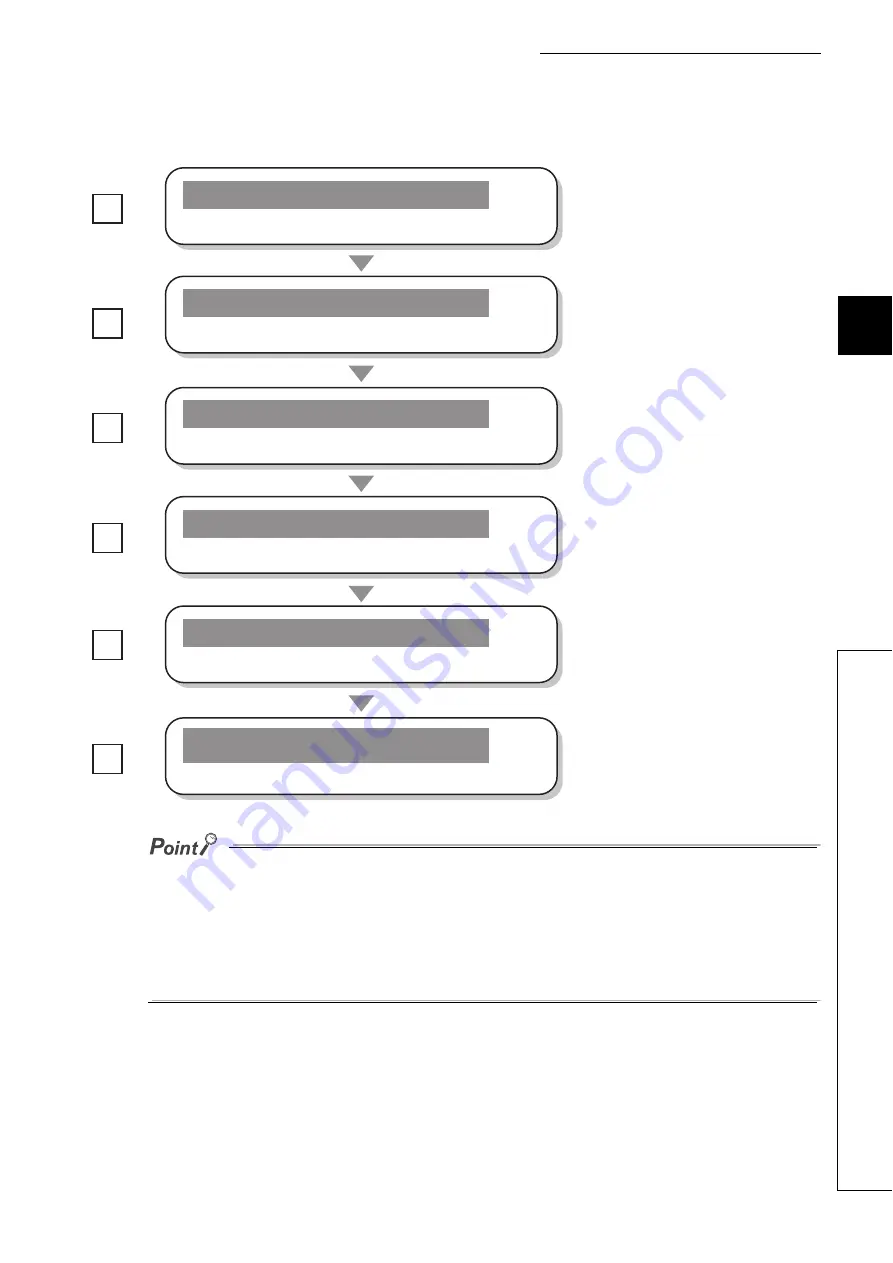
81
CHAPTER 4 PROCEDURES BEFORE OPERATION
4
(2) When the module is used as a temperature control module
●
A proper performance of temperature compensation is required for the NZ2GF2B-60TCTT4 which uses a thermocouple
for the temperature sensors. Perform warm-up operation about 15 minutes before starting operation.
●
To replace the module, follow the procedure described below.
• Turn off the power of the module and remove the temperature control module.
• Prepare a new temperature control module and follow the above procedure from "Setting a station number" to
"Parameter settings and programming". (The network parameter of the master station does not need to be set
again.)
• After checking the operation, restart the control.
For details on the setting of station numbers, refer to
the following.
•
For details on the mounting, refer to the following.
•
•
For details on the wiring, refer to the following.
•
•
•
For details on the execution of auto tuning, refer to
the following.
•
For details on the parameter settings and
programming, refer to the following.
•
•
•
Check box
Set a station number for a temperature control module.
Station number setting
Connection
Mount the temperature control module to a DIN rail.
Connect the temperature control module to a power supply,
Ethernet cables, and external devices.
Auto tuning execution
Set PID constants using the auto tuning function.
Warm-up operation
(when the NZ2GF2B-60TCTT4 is used)
Perform a warm-up operation for about 15 minutes before starting
an operation.
Wiring
Set parameters and create a program.
Parameter settings and programming
Summary of Contents for NZ2GF2B-60TCRT4
Page 2: ......
Page 86: ...84 Memo ...
Page 268: ...266 Memo ...
Page 377: ...375 APPENDICES A Appendix 6 External Dimensions Memo ...
Page 383: ...I 4 4 7 8 381 Memo ...
Page 387: ......