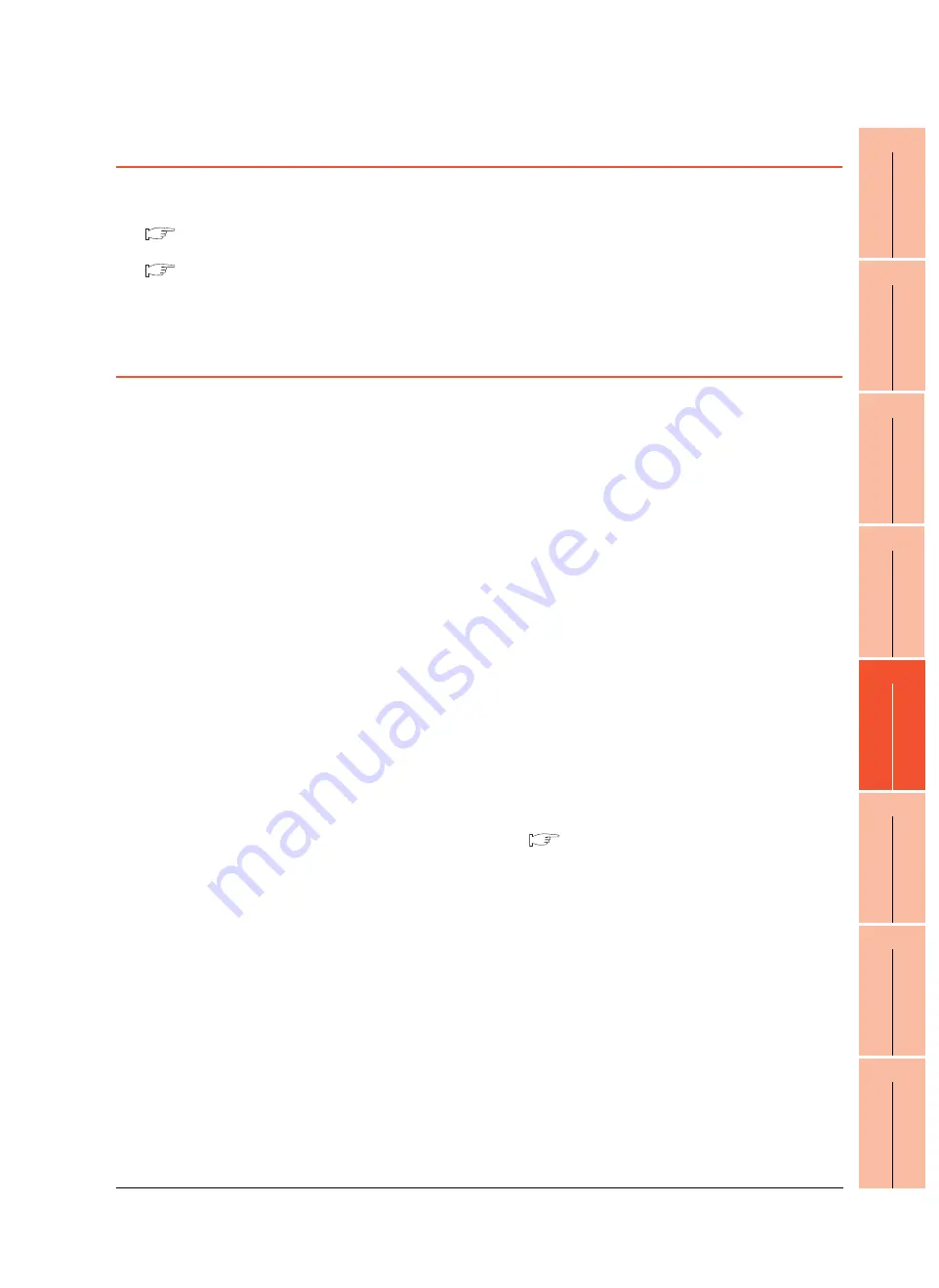
32. CONNECTION TO IAI ROBOT CONTROLLER
32.6 Device Range that Can Be Set
32 - 21
28
ENERG
Y MEAS
UR
ING
UNIT
/
ELECT
RIC M
UL
TI-
MEASURING
INSTRU
M
ENT
CO
NNECT
IO
N
29
GO
T
MUL
T
I-
DRO
P
CONNECTION
30
MUL
T
I-CHA
N
N
E
L
FUNCT
ION
31
F
A
TRANS
P
ARENT
FUNCTION
32
CO
NNE
C
TI
ON T
O
IA
I
ROBOT CON
T
ROLLER
33
CONNECTION
T
O
OMRON PLC
34
CO
N
N
EC
TI
O
N
T
O
OM
RON
T
E
MPERA
TURE
C
O
NT
ROL
LE
R
35
CONNECTION T
O
KEY
ENCE PLC
32.6 Device Range that Can Be Set
For details on the device range of controller that can be
used on GT16 Handy, refer to the following manuals.
GT Designer3 Version1 Screen Design Manual
(Fundamentals)
GOT1000Series Connection Manual
(Non-Mitsubishi Products 1) for GT Works3
32.7 Precautions
Program control device
• When Program Execution Command (0), Program
Exit Command (2), or Program Restart Command (4)
is written to the program control device (PRG 0), it
will be a request for all programs running in the
controllers.
• When unsupported write data is input to the program
control device, the following error is displayed in the
system alarm.
315: Device writing error.
Correct device.
Variable devices
The variable number 99 of Integer device and variable
number 199 of Real device are special devices used for
operations by the X-SEL controller system. Do not use
these variables for general purpose.
Command trigger compatible device
• For the device whose obtained data No.0 is a
command trigger, communication with the controller is
performed when the Write(1)/Read(2) is set to the
command trigger.
When the command trigger and setting value are
written in a batch, the communication is performed
based on the value set with batch write.
• When Clear(4) is set to the command trigger, the
communication with the controller is not performed
and the set value is initialized.
• When an unsupported set value is input to the
command trigger, the following error is displayed in
the system alarm.
315: Device writing error.
Correct device.
Device reserved for system use
Devices of ''Reserved for system uses'' are devices
with indefinite values. Do not write to these devices.
Write to the flash ROM
• The point data can be written to the flash ROM of the
X-SEL controller. When the point data is written to the
flash ROM, it is not cleared even when power supply
to the controller is turned off. However, there are limits
in the number of writing. For details, refer to the user's
manual of X-SEL controller used.
• Never turn off the main power supply during the flash
ROM write. Doing so may cause the loss of data and
malfunction of controllers. For details, refer to the
user's manual of X-SEL controller used.
Communication disconnection
• Writing to the flash ROM disconnects the
communication with controllers until the writing is
completed.
• Resetting software restarts the controllers. During this
time, the communication with controllers is
disconnected.
Station number setting of the IAI robot
controller system
The robot controller with the station number set with the
host address must be included.
32.4.2 Communication detail settings
Connection of the IAI X-SEL K type
Note the following precaution when using the controller
with the mode switch set to MANU.
• After powering up the X-SEL, connecting the GOT
before the PC software causes the program startup
disabled (A1D alarm) on the X-SEL side.
Summary of Contents for GT16
Page 1: ......
Page 2: ......
Page 46: ...1 4 1 OVERVIEW 1 1 Features ...
Page 54: ...2 8 2 SYSTEM CONFIGURATION 2 2 System Equipment ...
Page 60: ...3 6 3 SPECIFICATIONS 3 4 Battery specifications ...
Page 72: ...5 8 5 UL cUL STANDARDS AND EMC DIRECTIVE 5 2 EMC Directive ...
Page 102: ...6 30 6 OPTION 6 7 Connector Conversion Box ...
Page 106: ...7 4 7 INSTALLATION 7 1 Installing Procedure ...
Page 110: ...8 4 8 COMMUNICATION CABLE 8 1 Overview of Communication Cable ...
Page 130: ...9 20 9 HANDLING OF POWER WIRING AND SWITCH 9 4 Switch Wiring ...
Page 142: ...10 12 10 UTILITY FUNCTION 10 3 Utility Display ...
Page 184: ...11 42 11 DISPLAY AND OPERATION SETTINGS GOT SET UP 11 4 Maintenance Function ...
Page 202: ...12 18 12 COMMUNICATION INTERFACE SETTING COMMUNICATION SETTING 12 3 Ethernet Setting ...
Page 226: ...13 24 13 DEBUG 13 3 Memory Data Control ...
Page 248: ...14 22 14 SELF CHECK 14 2 Batch Self Check ...
Page 350: ...15 102 15 DATA CONTROL 15 3 OS Project Information ...
Page 410: ...19 22 19 TROUBLESHOOTING 19 2 Error Message and System Alarm ...
Page 418: ...App 8 APPENDICES Appendix 3 Transportation Precautions ...
Page 422: ...REVISIONS 4 ...
Page 425: ......
Page 426: ......
Page 427: ......
Page 428: ......
Page 470: ......
Page 510: ...21 22 21 COMPUTER LINK CONNECTION 21 6 Precautions ...
Page 568: ...22 58 22 ETHERNET CONNECTION 22 5 Precautions ...
Page 584: ......
Page 626: ...25 14 25 SERVO AMPLIFIER CONNECTION 25 7 Precautions ...
Page 632: ...26 6 26 ROBOT CONTROLLER CONNECTION 26 6 Precautions ...
Page 647: ...MULTIPLE GOT CONNECTIONS 29 GOT MULTI DROP CONNECTION 29 1 ...
Page 648: ......
Page 659: ...MULTI CHANNEL FUNCTION 30 MULTI CHANNEL FUNCTION 30 1 ...
Page 660: ......
Page 675: ...FA TRANSPARENT FUNCTION 31 FA TRANSPARENT FUNCTION 31 1 ...
Page 676: ......
Page 742: ...31 66 31 FA TRANSPARENT FUNCTION 31 7 Precautions ...
Page 744: ......
Page 766: ...32 22 32 CONNECTION TO IAI ROBOT CONTROLLER 32 7 Precautions ...
Page 802: ...34 10 34 CONNECTION TO OMRON TEMPERATURE CONTROLLER 34 7 Precautions ...
Page 834: ...36 18 36 CONNECTION TO KOYO EI PLC 36 6 Device Range that Can Be Set ...
Page 858: ...38 12 38 CONNECTION TO SHARP PLC 38 6 Device Range that Can Be Set ...
Page 868: ...39 10 39 CONNECTION TO SHINKO TECHNOS INDICATING CONTROLLER 39 7 Precautions ...
Page 902: ...42 6 42 CONNECTION TO TOSHIBA MACHINE PLC 42 6 Device Range that Can Be Set ...
Page 908: ...43 6 43 CONNECTION TO PANASONIC SERVO AMPLIFIER 43 7 Precautions ...
Page 970: ...48 12 48 CONNECTION TO FUJI TEMPERATURE CONTROLLER 48 7 Precautions ...
Page 1052: ...52 26 52 CONNECTION TO AZBIL CONTROL EQUIPMENT 52 7 Precautions ...
Page 1102: ...55 14 55 CONNECTION TO GE PLC 55 7 Precautions ...
Page 1114: ...57 4 57 CONNECTION TO SICK SAFETY CONTROLLER 57 5 Device Range that Can Be Set ...
Page 1128: ...59 2 59 CONNECTION TO HIRATA CORPORATION HNC CONTROLLER ...
Page 1130: ...60 2 60 CONNECTION TO MURATEC CONTROLLER ...
Page 1132: ......
Page 1270: ...62 68 62 MICROCOMPUTER CONNECTION ETHERNET 62 8 Precautions ...
Page 1271: ...MODBUS CONNECTIONS 63 MODBUS R RTU CONNECTION 63 1 64 MODBUS R TCP CONNECTION 64 1 ...
Page 1272: ......
Page 1292: ...64 12 64 MODBUS R TCP CONNECTION 64 7 Precautions ...
Page 1293: ...CONNECTIONS TO PERIPHERAL EQUIPMENT 65 VNC R SERVER CONNECTION 65 1 ...
Page 1294: ......
Page 1298: ...65 4 65 VNC R SERVER CONNECTION 65 4 Setting in Personal Computer ...
Page 1302: ...REVISIONS 4 ...
Page 1305: ......
Page 1306: ......