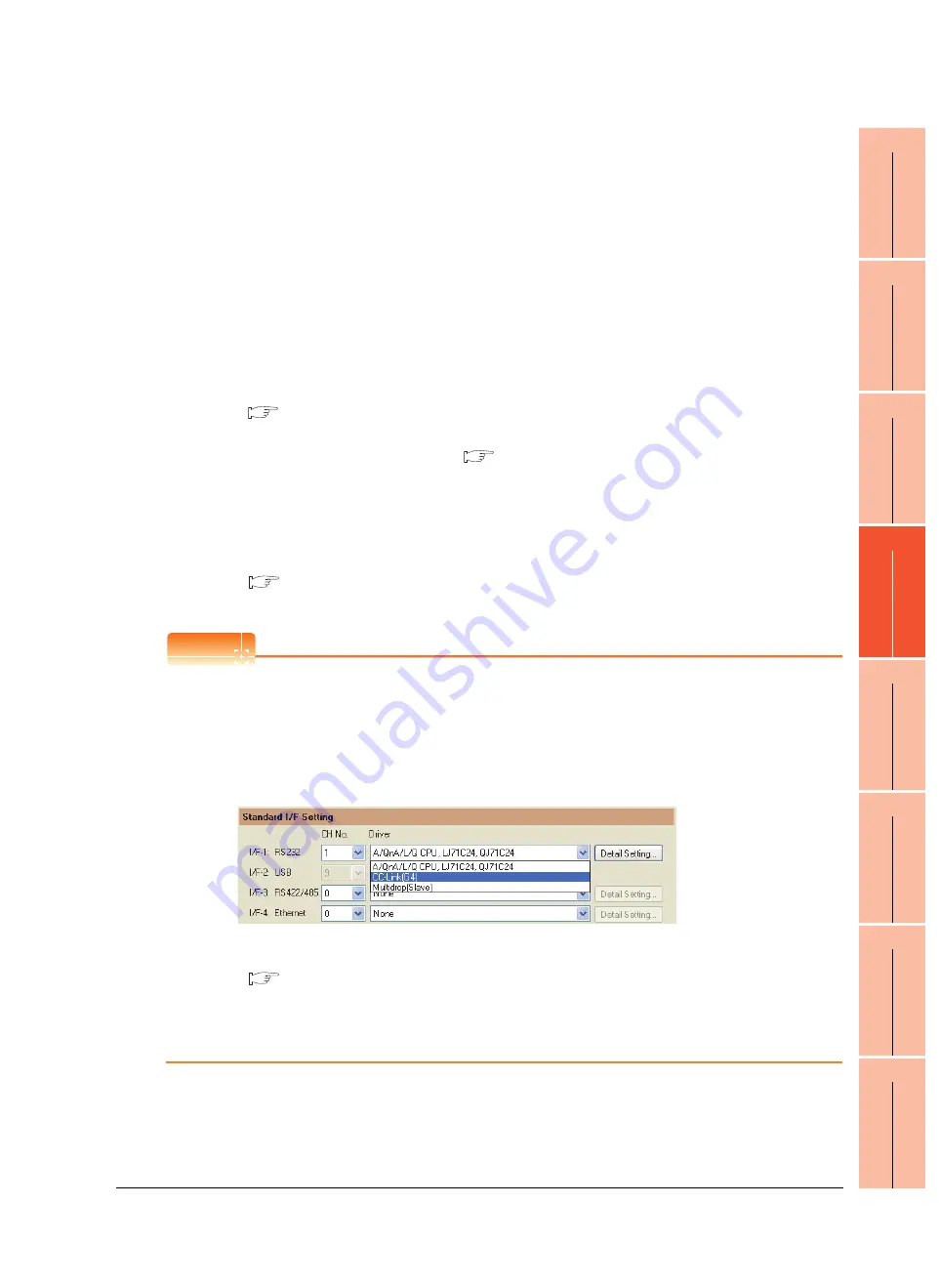
12. COMMUNICATION INTERFACE SETTING (COMMUNICATION SETTING)
12.1 Communication Setting
12 - 3
9
HANDLING OF PO
WER WI
RI
N
G
AND SWIT
CH
10
UTIL
ITY FUNC
TION
11
DI
SPLA
Y
A
N
D
OP
ERA
T
IO
N
SE
TTI
N
GS
12
COMMUNICA
TION
INTE
RF
A
C
E
SE
TT
IN
G
13
DE
BUG
14
S
E
LF CHECK
15
D
A
TA
CONTROL
16
IN
ST
ALLA
TI
ON OF
COREOS,
B
O
OT
OS A
ND
ST
ANDA
RD MONI
TO
R OS
(3) Channel number specification menu BOX
Set channel No. to use with standard interface.
Refer to This section (4) for driver that can be assigned to each channel.
• Fixed to 9 for the USB interface.
*1
Cannot be assigned with Ethernet I/F Assignment.
(4) Driver display BOX
The name of communication driver assigned to the channels or the driver set with the Communication Setting of
GT Designer3 is displayed.
For details of drivers to be displayed, refer to the following manual.
GT Designer3 Version1 Screen Design Manual (Fundamentals)
Display [None] in the driver display BOX in case of the followings.
• The communication driver is not installed. (
• In channel number specification menu BOX, [0] is set.
When the channel number is set to [9], the communication driver [Host (PC)] is automatically assigned.
(5) Assign Ethernet I/F
The communication settings for the Ethernet connection can be made.
Ethernet I/F Assignment can assign up to four channels per interface.
POINT
POINT
POINT
Precautions for communications between GOT and controller
(1) Installing communication driver and downloading Communication Setting
The followings below are required for the communication interface to communicate with the controller.
1)
Installing communication drivers (Up to 4 communication drivers)
2)
Assigning the channel number and communication driver for the communication interface
3)
Downloading the contents (project data) assigned in 2).
Perform1), 2), 3) by GT Designer3.
Refer to the following for details.
17. DRAWING SOFTWARE SETTINGS (CONTROLLER SETTING AND COMMON SETTINGS)
(2) When Communication Setting has not been downloaded.
When [Communication Settings] has not been downloaded using drawing software, make the communication
settings in the drawing software or on the utility screen of the GOT.
0
: Set when the communication interface is not used.
1 to 4 : Set when connecting to a controller.
9
*1
: Set when connecting with PC (GT Designer3 ).
*
: Set when using the function that uses the gateway function (when connection types except the Ethernet
connection is used for connecting to controllers), Ethernet download function.
Summary of Contents for GT16
Page 1: ......
Page 2: ......
Page 46: ...1 4 1 OVERVIEW 1 1 Features ...
Page 54: ...2 8 2 SYSTEM CONFIGURATION 2 2 System Equipment ...
Page 60: ...3 6 3 SPECIFICATIONS 3 4 Battery specifications ...
Page 72: ...5 8 5 UL cUL STANDARDS AND EMC DIRECTIVE 5 2 EMC Directive ...
Page 102: ...6 30 6 OPTION 6 7 Connector Conversion Box ...
Page 106: ...7 4 7 INSTALLATION 7 1 Installing Procedure ...
Page 110: ...8 4 8 COMMUNICATION CABLE 8 1 Overview of Communication Cable ...
Page 130: ...9 20 9 HANDLING OF POWER WIRING AND SWITCH 9 4 Switch Wiring ...
Page 142: ...10 12 10 UTILITY FUNCTION 10 3 Utility Display ...
Page 184: ...11 42 11 DISPLAY AND OPERATION SETTINGS GOT SET UP 11 4 Maintenance Function ...
Page 202: ...12 18 12 COMMUNICATION INTERFACE SETTING COMMUNICATION SETTING 12 3 Ethernet Setting ...
Page 226: ...13 24 13 DEBUG 13 3 Memory Data Control ...
Page 248: ...14 22 14 SELF CHECK 14 2 Batch Self Check ...
Page 350: ...15 102 15 DATA CONTROL 15 3 OS Project Information ...
Page 410: ...19 22 19 TROUBLESHOOTING 19 2 Error Message and System Alarm ...
Page 418: ...App 8 APPENDICES Appendix 3 Transportation Precautions ...
Page 422: ...REVISIONS 4 ...
Page 425: ......
Page 426: ......
Page 427: ......
Page 428: ......
Page 470: ......
Page 510: ...21 22 21 COMPUTER LINK CONNECTION 21 6 Precautions ...
Page 568: ...22 58 22 ETHERNET CONNECTION 22 5 Precautions ...
Page 584: ......
Page 626: ...25 14 25 SERVO AMPLIFIER CONNECTION 25 7 Precautions ...
Page 632: ...26 6 26 ROBOT CONTROLLER CONNECTION 26 6 Precautions ...
Page 647: ...MULTIPLE GOT CONNECTIONS 29 GOT MULTI DROP CONNECTION 29 1 ...
Page 648: ......
Page 659: ...MULTI CHANNEL FUNCTION 30 MULTI CHANNEL FUNCTION 30 1 ...
Page 660: ......
Page 675: ...FA TRANSPARENT FUNCTION 31 FA TRANSPARENT FUNCTION 31 1 ...
Page 676: ......
Page 742: ...31 66 31 FA TRANSPARENT FUNCTION 31 7 Precautions ...
Page 744: ......
Page 766: ...32 22 32 CONNECTION TO IAI ROBOT CONTROLLER 32 7 Precautions ...
Page 802: ...34 10 34 CONNECTION TO OMRON TEMPERATURE CONTROLLER 34 7 Precautions ...
Page 834: ...36 18 36 CONNECTION TO KOYO EI PLC 36 6 Device Range that Can Be Set ...
Page 858: ...38 12 38 CONNECTION TO SHARP PLC 38 6 Device Range that Can Be Set ...
Page 868: ...39 10 39 CONNECTION TO SHINKO TECHNOS INDICATING CONTROLLER 39 7 Precautions ...
Page 902: ...42 6 42 CONNECTION TO TOSHIBA MACHINE PLC 42 6 Device Range that Can Be Set ...
Page 908: ...43 6 43 CONNECTION TO PANASONIC SERVO AMPLIFIER 43 7 Precautions ...
Page 970: ...48 12 48 CONNECTION TO FUJI TEMPERATURE CONTROLLER 48 7 Precautions ...
Page 1052: ...52 26 52 CONNECTION TO AZBIL CONTROL EQUIPMENT 52 7 Precautions ...
Page 1102: ...55 14 55 CONNECTION TO GE PLC 55 7 Precautions ...
Page 1114: ...57 4 57 CONNECTION TO SICK SAFETY CONTROLLER 57 5 Device Range that Can Be Set ...
Page 1128: ...59 2 59 CONNECTION TO HIRATA CORPORATION HNC CONTROLLER ...
Page 1130: ...60 2 60 CONNECTION TO MURATEC CONTROLLER ...
Page 1132: ......
Page 1270: ...62 68 62 MICROCOMPUTER CONNECTION ETHERNET 62 8 Precautions ...
Page 1271: ...MODBUS CONNECTIONS 63 MODBUS R RTU CONNECTION 63 1 64 MODBUS R TCP CONNECTION 64 1 ...
Page 1272: ......
Page 1292: ...64 12 64 MODBUS R TCP CONNECTION 64 7 Precautions ...
Page 1293: ...CONNECTIONS TO PERIPHERAL EQUIPMENT 65 VNC R SERVER CONNECTION 65 1 ...
Page 1294: ......
Page 1298: ...65 4 65 VNC R SERVER CONNECTION 65 4 Setting in Personal Computer ...
Page 1302: ...REVISIONS 4 ...
Page 1305: ......
Page 1306: ......