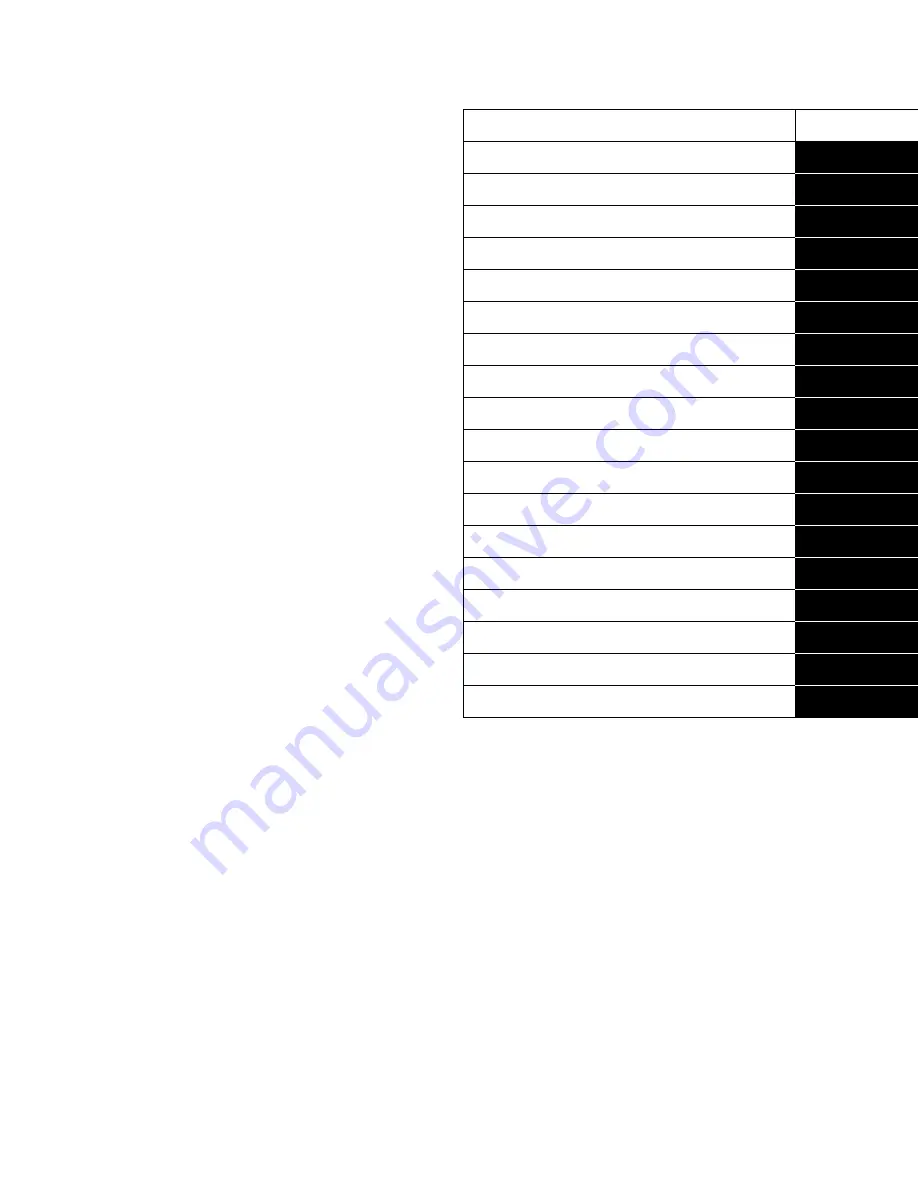
CONTENTS
Mazda6
Workshop
Manual
FOREWORD
This manual contains on-vehicle service
and diagnosis for the Mazda6.
For proper repair and maintenance,
a thorough familiarization with this manual
is important, and it should always be kept
in a handy place for quick and easy
reference.
All the contents of this manual, including
drawings and specifications, are the latest
available at the time of printing.
As modifications affecting repair or
maintenance occur, relevant information
supplementary to this volume will be made
available at Mazda dealers. This manual
should be kept up-to-date.
Mazda Motor Corporation reserves
the right to alter the specifications and
contents of this manual without obligation
or advance notice.
All rights reserved. No part of this book
may be reproduced or used in any form or
by any means, electronic or
mechanical—including photocopying and
recording and the use of any kind of
information storage and retrieval
system—without permission in writing.
Mazda Motor Corporation
HIROSHIMA, JAPAN
APPLICATION:
This manual is applicable to vehicles
beginning with the Vehicle Identification
Numbers (VIN), and related materials shown
on the following page.
© 2002 Mazda Motor Corporation
PRINTED IN The Netherlands, MARCH 2002
1730–1E–02C
Title
Section
General Information
GI
Engine
B
Lubrication System
D
Cooling System
E
Fuel and Emission Control Systems
F
Engine Electrical System
G
Clutch
H
Manual Transaxle
J
Automatic Transaxle
K
Front and Rear Axles
M
Steering System
N
Braking System
P
Suspension
R
Body
S
Body Electrical System
T
Heater and Air Conditioner Systems
U
Technical Data
TD
Special Tools
ST
Summary of Contents for 6 2002
Page 104: ...F 4 LOCATION INDEX End Of Sie FUEL SYSTEM A6E390001006W01 Engine Room Side A6E3912W015...
Page 151: ...F 36 EXHAUST SYSTEM A6E3914W002...
Page 312: ...F 182 TROUBLESHOOTING QUICK DIAGNOSTIC CHART A6E398018881W02 A6E3980W001...
Page 313: ...TROUBLESHOOTING F 183 F A6E3980W002...
Page 314: ...F 184 TROUBLESHOOTING A6E3980W003...
Page 315: ...TROUBLESHOOTING F 185 F End Of Sie A6E3980W004...
Page 410: ...K 3 K...
Page 526: ...TROUBLESHOOTING K 115 K QUICK DIAGNOSIS CHART A6E568001030W04 A6E5680W001...
Page 527: ...K 116 TROUBLESHOOTING End Of Sie A6E5680W002...
Page 653: ...ON BOARD DIAGNOSTIC ABS TCS P 57 P...
Page 701: ...TROUBLESHOOTING ABS TCS DYNAMIC STABILITY CONTROL P 105 P Vehicle with ABS TCS A6E6980W002...
Page 819: ...OUTSIDE MIRROR S 60 2 THIS PAGE IS INTENTIONALLY LEFT BLANK End Of Sie...
Page 971: ...T 76 WARNING AND INDICATOR SYSTEM Operating Order A6E8118W009...
Page 1150: ...U 4 LOCATION INDEX End Of Sie CONTROL SYSTEM A6E850001042W01 L H D A6E8500W003 A6E8500W004...
Page 1152: ...U 6 LOCATION INDEX R H D A6E8500W005 A6E8500W006...