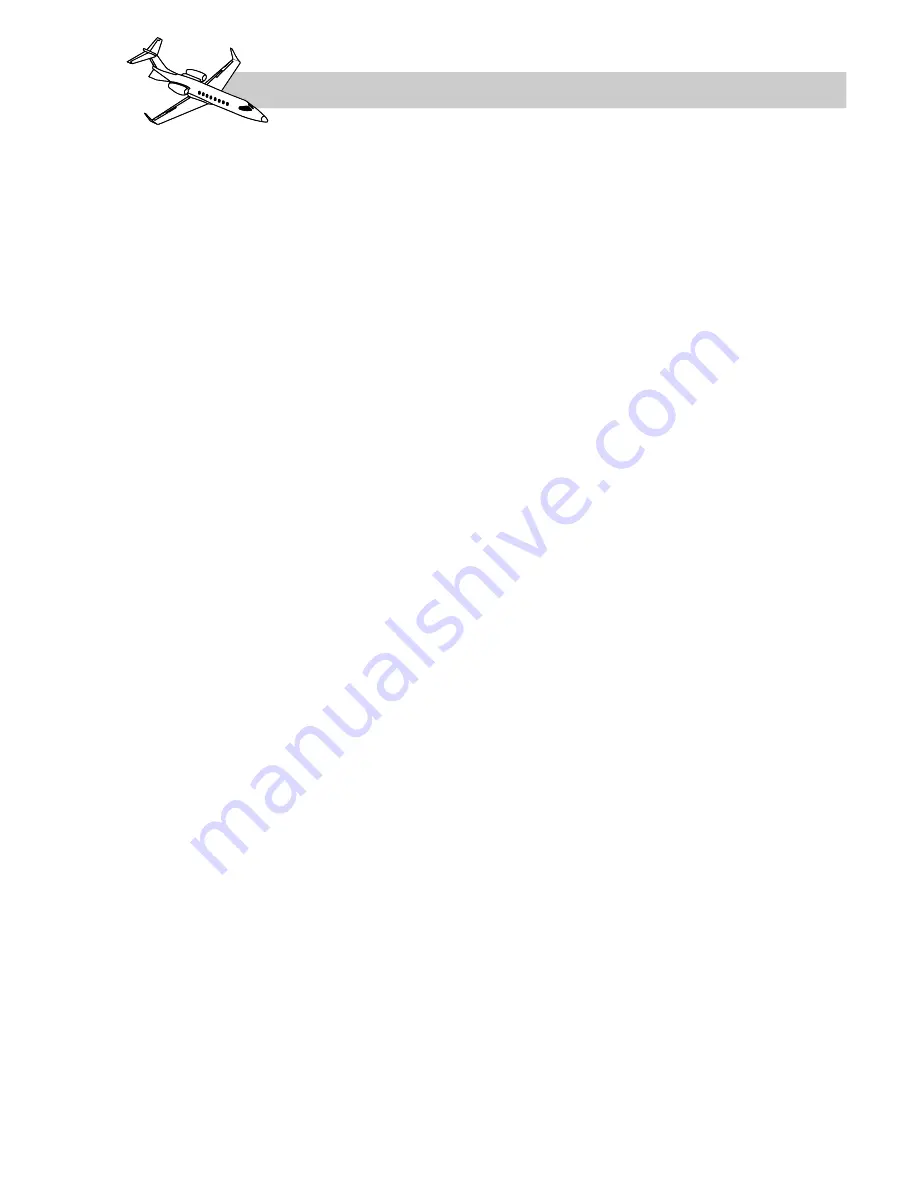
BRAKES
GENERAL
The Learjet 45 is provided with a brake-by-
wire system that electronically controls the hy-
draulic pressure applied to the brakes (Figure
14-16). The brake system has four self-ad-
justing brake assemblies, one on each main
landing gear wheel. Wear pins allow visual in-
spection for brake wear (Figure 14-17). Brake
fuses (one in each brake line) close when a
downstream hydraulic leak is detected.
The brake control system consists of four
pedal-actuated dual transducers (LVDTs).
Either pilot can control the brake pressure via
the individual pedal transducers. By depress-
ing the top section of the rudder pedals, the
transducers send signals, proportional to brake
pedal displacement, to both channels of the
Brake Control Unit (BCU). The BCU is divided
into inboard and outboard channels for isola-
tion and independence. The BCU commands
the brake shutoff valves to open, allowing hy-
draulic pressure to flow to the brake control
valves, which then meter hydraulic pressure
to each wheel brake.
Additionally, the BCU provides touchdown
protection which prevents pressure from being
sent to the individual brakes until wheel spin-
up or ground mode time-out has been estab-
lished. This prevents landing with the brakes
applied, and allows time for the airplane to es-
tablish traction prior to braking action. The
touchdown protection feature requires a 50
kts minimum wheel speed or a 3 second time
delay after the squat switch system has tran-
sitioned to the ground mode.
Locked-wheel protection is provided so that
brake pressure is removed from a wheel if that
wheel’s velocity is less than approximately
30% of the velocity of the faster wheel in a
given channel.
Gear retraction braking is also provided by the
BCU to stop rotation before the main gear
wheels enter the wheel well area. Once the
squat switches have transitioned to the air
mode, and the gear control switch is moved to
UP, a 200 psi braking command is applied for
a few seconds to stop wheel rotation.
Should the main hydraulic system fail, the
auxiliary hydraulic system provides pressure
for normal braking capability with anti-skid
protection. In the event of multiple failures
(total hydraulic and/or electrical), emergency
braking pressure is available from the brake
accumulator, via the hand operated emer-
gency/parking brake system. The brake accu-
mulator also powers the parking brake and is
set by locking the emergency/parking brake
handle, located on the center pedestal, in the
applied position (Figure 14-18).
BRAKE OPERATION
Depressing either set of brake pedals sends an
electronic signal, proportional to pedal de-
flection, to the BCU. The Brake Control Unit
also receives wheel speed signals from the
four axle-mounted wheel-speed transducers,
and the left and right squat switches. Brake
pressure transducer inputs to the BCU close
the brake control/anti-skid control loop. The
BCU resolves the various inputs and sends
the electronic signal commanding the brake
control valves to meter hydraulic pressure to
the wheel brakes. The brake system (Figure 14-
16) is configured so that the outboard brake
control valves operate the left and right out-
board wheel brakes and the inboard brake con-
trol valves operate the left and right inboard
brakes. This prevents a single failure from
causing an asymmetric braking condition or
more than 50% loss of braking.
When operating in slush or snow, frequent
brake applications creates friction heat that
may prevent brake freezing during ground
operations.
Electrical power for the brakes and anti-skid
system is 28 VDC. The inboard brakes receive
power from the emergency battery bus through
the INBD BRAKES circuit breaker located
on the pilot circuit breaker panel in the
14-17
FOR TRAINING PURPOSES ONLY
L E A R J E T 4 5
P I L O T T R A I N I N G M A N U A L
FlightSafety
international
L E A R J E T 4 5
P I L O T T R A I N I N G M A N U A L
FlightSafety
international