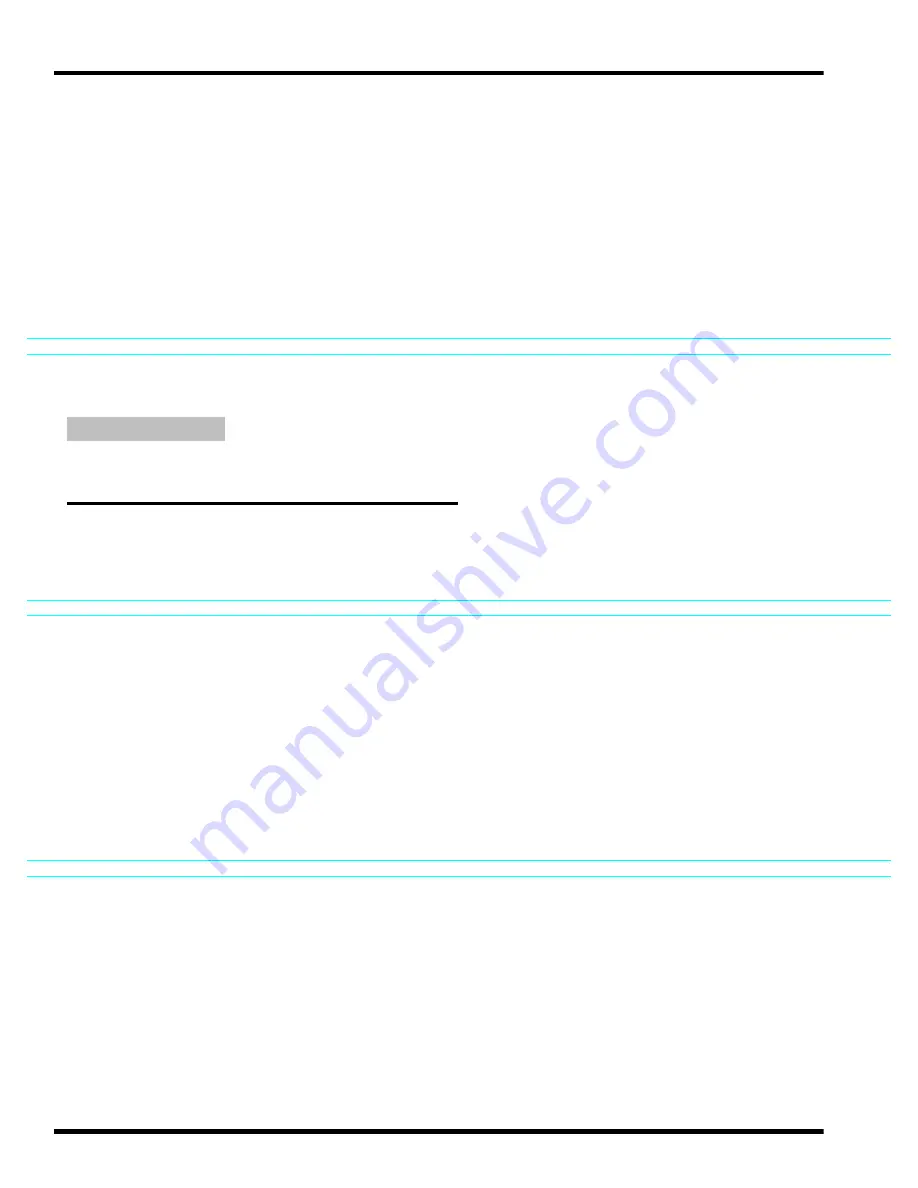
5-14
6999-0003 7/15/99
ENGINE REMOVAL/INSTALLATION
(StepNumber)
(StepNumber)
(StepNumber)
(StepNumber)
3. Loop the drive belt around the engine drive sprocket, and
the rear wheel driven sprocket.
1. DRIVE BELT
2. DRIVE SPROCKET
3. REAR WHEEL DRIVEN
SPROCKET
4. Move the rear wheel back, until there is tension on the belt.
5. Tighten the rear wheel adjusters to establish a constant
belt tension.
Notice
Do not finish tighten the axle adjustment locknuts, axle
nut or drive pulley nut, this will be completed in later
procedures.
1. MOVE REAR WHEEL BACK 2. REAR WHEEL ADJUSTER
Drive Sprocket Nut
6. With the transmission in gear and the rear brake held on.
Tighten the drive sprocket nut, to a torque of 95 ft-lb.
7. On tabbed washer, bend the locking tabs down, into the
drive sprocket nut to lock it in place.
1. DRIVE SPROCKET NUT
2. TABBED WASHER
3. LOCKING TABS
Drive Sprocket Cover
8. Install the drive sprocket
1. DRIVE SPROCKET COVER
Summary of Contents for HCX 1999
Page 1: ......
Page 5: ...FOREWORD 6999 0003 7 15 99 iii...
Page 7: ...6999 0003 7 15 99 v...
Page 8: ...1 0 6999 0003 7 15 99 ROUTINE MAINTENANCE 1...
Page 10: ...1 2 6999 0003 7 15 99 ROUTINE MAINTENANCE TROUBLESHOOTING MAINTENANCE INTERVALS...
Page 18: ...1 10 6999 0003 7 15 99 ROUTINE MAINTENANCE...
Page 19: ...ROUTINE MAINTENANCE 6999 0003 7 15 99 1 11...
Page 20: ...ROUTINE MAINTENANCE NOTES 6999 0003 7 15 99 1 12...
Page 21: ...ROUTINE MAINTENANCE 6999 0003 7 15 99 1 13...
Page 22: ...2 0 6999 0003 7 15 99 BODY EXHAUST 2...
Page 37: ...BODY EXHAUST 6999 0003 7 15 99 2 15...
Page 38: ...3 0 6999 0003 7 15 99 LUBRICATION SYSTEM 3 10732...
Page 49: ...LUBRICATION SYSTEM NOTES 6999 0003 7 15 99 3 11...
Page 50: ...4 0 6999 0003 7 15 99 ENGINE CONTROL SYSTEM 4...
Page 206: ...5 0 6999 0003 7 15 99 ENGINE REMOVAL INSTALLATION 5...
Page 208: ...5 2 6999 0003 7 15 99 ENGINE REMOVAL INSTALLATION TROUBLESHOOTING...
Page 235: ...ENGINE REMOVAL INSTALLATION 6999 0003 7 15 99 5 29...
Page 236: ...5 30 6999 0003 7 15 99 ENGINE REMOVAL INSTALLATION...
Page 237: ...ENGINE REMOVAL INSTALLATION 6999 0003 7 15 99 5 31...
Page 238: ...5 32 6999 0003 7 15 99 ENGINE REMOVAL INSTALLATION...
Page 239: ...ENGINE REMOVAL INSTALLATION 6999 0003 7 15 99 5 33...
Page 240: ...5 34 6999 0003 7 15 99 ENGINE REMOVAL INSTALLATION...
Page 241: ...ENGINE REMOVAL INSTALLATION 6999 0003 7 15 99 5 35...
Page 242: ...5 36 6999 0003 7 15 99 ENGINE REMOVAL INSTALLATION...
Page 243: ...ENGINE REMOVAL INSTALLATION 6999 0003 7 15 99 5 37...
Page 244: ...5 38 6999 0003 7 15 99 ENGINE REMOVAL INSTALLATION...
Page 245: ...ENGINE REMOVAL INSTALLATION NOTES 6999 0003 7 15 99 5 39...
Page 246: ...6 0 6999 0003 7 15 99 CYLINDER HEAD CAM DRIVE 6...
Page 274: ...7 0 6999 0003 7 15 99 CYLINDER PISTON 7...
Page 292: ...8 0 6999 0003 7 15 99 CRANKCASE CRANKSHAFT 8...
Page 308: ...9 0 6999 0003 7 15 99 PRIMARY DRIVE 9 10794...
Page 316: ...10 0 6999 0003 7 15 99 CLUTCH 10 10758...
Page 333: ...CLUTCH NOTES 6999 0003 7 15 99 10 17...
Page 334: ...11 0 6999 0003 7 15 99 TRANSMISSION 11 10822...
Page 352: ...12 0 6999 0003 7 15 99 WHEELS 12 10736...
Page 373: ...WHEELS NOTES 6999 0003 7 15 99 12 21...
Page 374: ...13 0 6999 0003 7 15 99 FRONT SUSPENSION STEERING 13...
Page 392: ...14 0 6999 0003 7 15 99 REAR SUSPENSION 14...
Page 398: ...14 6 6999 0003 7 15 99 REAR SUSPENSION StepNumber 1 2...
Page 399: ...REAR SUSPENSION 6999 0003 7 15 99 14 7...
Page 400: ...15 0 6999 0003 7 15 99 BRAKES 15...
Page 420: ...16 0 6999 0003 7 15 99 BATTERY CHARGING SYSTEM 16...
Page 431: ...BATTERY CHARGING SYSTEM NOTES 6999 0003 7 15 99 16 11...
Page 432: ...17 0 6999 0003 7 15 99 STARTER 17 10722...
Page 443: ...STARTER NOTES 6999 0003 7 15 99 17 11...
Page 444: ...18 0 6999 0003 7 15 99 LIGHTS GAUGES SWITCHES 18...
Page 472: ...18 28 6999 0003 7 15 99 LIGHTS GAUGES SWITCHES...
Page 474: ...WIRING SCHEMATIC NOTES 19 2 6999 0003 7 15 99...