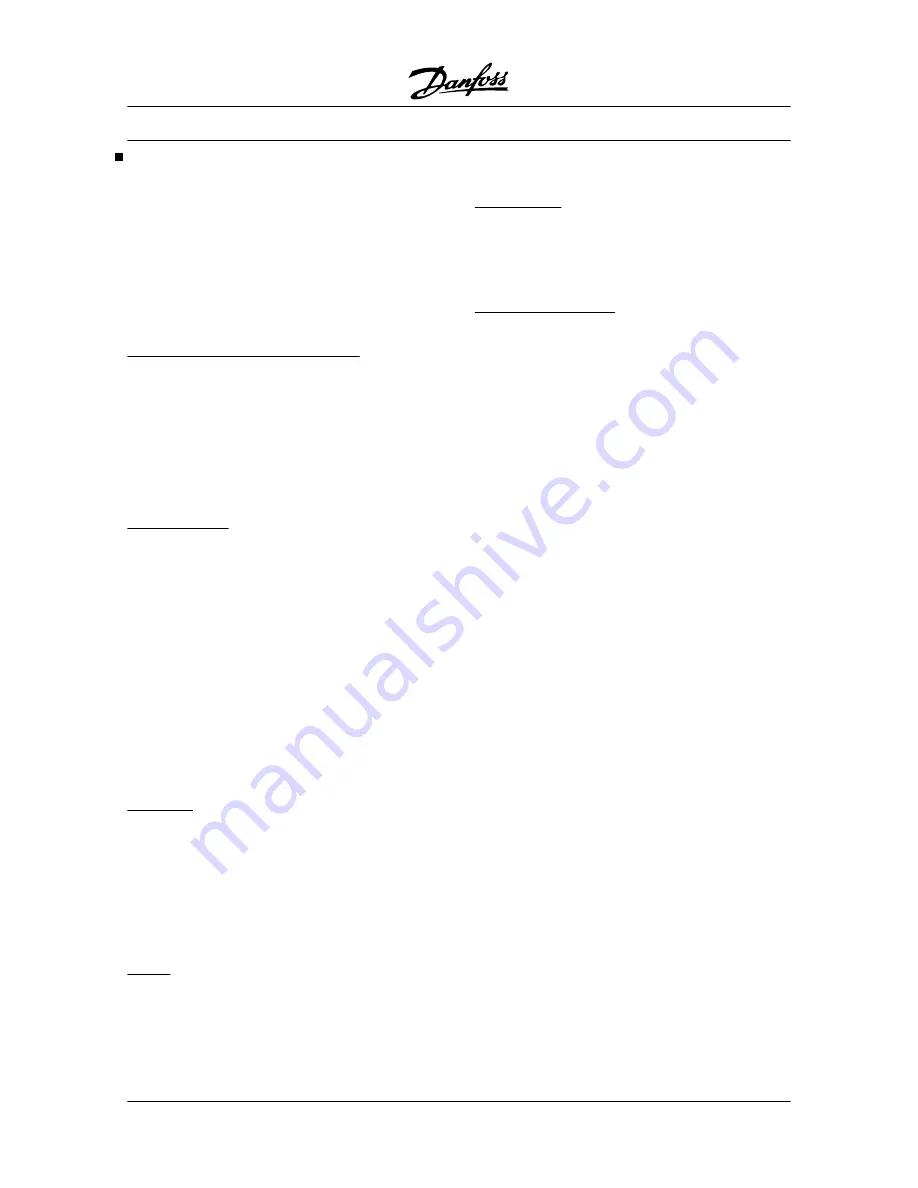
VLT 5000 controllers
VLT 5000 has three inbuilt controllers: one for speed
control, one for process control and one for torque
control.
Speed control and process control are in the form of a
PID controller that requires a feedback to an input.
Torque control is in the form of a PI controller that does
not require a feedback, since the torque is calculated
by the adjustable frequency drive on the basis of the
current measured.
Setting of speed and process controller
With respect to both PID controllers, there are a num-
ber of settings which are made in the same parame-
ters; however, the choice of controller type will affect
the choices to be made under the common parame-
ters.
In parameter 100
Configuration
, a choice is made of
controller,
Speed control, closed loop
or
Process con-
trol, closed loop
.
Feedback signal:
A feedback range must be set for both controllers. This
feedback range at the same time limits the possible
reference range, which means that if the sum of all
references is outside the feedback range, the refer-
ence will be limited to being within this range. The
feedback range is set in the units that belong to the
application (Hz, RPM, bar, °C, etc.). Setting is effected
directly in a parameter for the individual input terminal,
thereby deciding whether it should be used for feed-
back in connection with one of the controllers. Inputs
that are not used can be disabled, which will ensure
that they do not disturb control. If feedback has been
selected on two terminals at the same time, these two
signals will be added up.
Reference:
For both controllers, it is possible to set four preset
references. These can be set between -100% and
+100% of the maximum reference or the sum of the
external references. External references can be ana-
log signals, pulse signals and/or serial communication.
All references will be added and the sum will be the
reference for subsequent regulation.
It is possible to limit the reference range to a range
smaller than the feedback range. This can be an ad-
vantage if it is to be avoided that an unintended change
of an external reference makes the sum of references
move too far away from the optimum reference. As
with the feedback range, the reference range is set in
the units that belong to the applications in question.
Speed control:
This PID control has been optimized for use in appli-
cations with a need to maintain a given motor speed.
The parameters that are specific to the speed control-
ler are parameters 417 to 421.
PID for process control:
This PID control has been optimized for process con-
trol. This controller does not have a feedforward facili-
ty, but a number of special features that are relevant
to process control.
There is a choice of whether normal control is required,
in which the speed is increased in the case of an error
between the reference and the feedback, or whether
inverse control is to be applied, in which the speed is
reduced in the case of an error.
There is also a choice of whether the integrator is to
continue integrating in the case of an error, even if VLT
5000 is at the minimum/maximum frequency or at the
current limit. If VLT 5000 is in such a borderline situa-
tion, any attempt to change the motor speed will be
restricted by this limit. The integrator comes from the
works preset to stop integrating. Integration will be ad-
justed to a gain that corresponds to the given output
frequency.
In certain applications, it is either difficult or completely
impossible to measure such a factor as the level. In
such cases, it can be necessary to allow the integrator
to continue integrating on the fault, even if the motor
speed cannot be changed. This will make the integra-
tor work as a kind of counter, i.e. once the feedback
indicates that the speed must be changed in a direction
away from the borderline situation, the integration will
give this change a delay that depends on the time for
which the integrator has overcompensated for the pre-
vious error.
Furthermore, it is possible to program a starting fre-
quency in which VLT 5000 will wait without activating
the controller until this frequency has been reached.
This makes it possible, for example, to quickly build up
the necessary static pressure in a pumping system.
VLT
®
5000 Series
172
MG.51.C5.22 - VLT
p
is a registered Danfoss trademark.
Summary of Contents for VLT 5000 Series
Page 2: ...VLT 5000 Instruction Manual ...
Page 3: ......
Page 185: ...VLT 5000 Series 182 MG 51 C5 22 VLT p is a registered Danfoss trademark ...
Page 186: ...VLT 5000 Series MG 51 C5 22 VLT p is a registered Danfoss trademark 183 EC EMC ...
Page 197: ...EXTERNAL PRESET VLT 5000 Series 194 MG 51 C5 22 VLT p is a registered Danfoss trademark ...
Page 202: ...VLT 5000 Series MG 51 C5 22 VLT p is a registered Danfoss trademark 199 List of functions ...
Page 217: ...VLT 5000 Series 214 MG 51 C5 22 VLT p is a registered Danfoss trademark ...
Page 239: ......