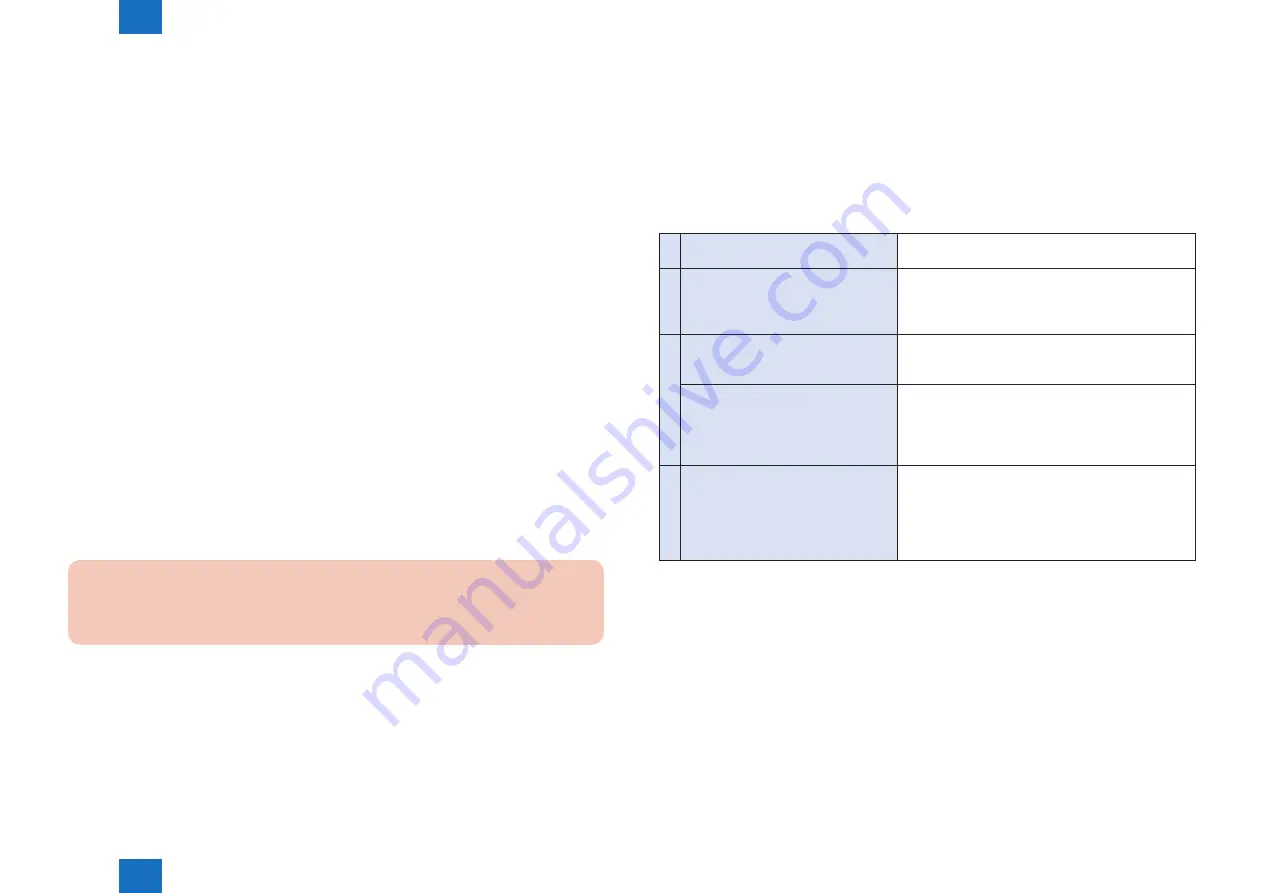
2
2
2-74
2-74
Technology > Fixing System > Various Types of Control > Fixing temperature control
Technology > Fixing System > Various Types of Control > Fixing temperature control
(5) Operation flow based on the output result
Upon user’s request or based on the status of output result or, switch the foregoing fixing
adjustment items as below.
Also, check the product usage situation and paper used by users and instruct them to
switch the each fixing adjustment appropriately.
In case of poor fixing performance;
1) Specify [Fixing priority] in [Adjust fixing of paper source] (default setting is standard).
2) Specify [Fixing priority] in [Adjust fixing for natural conditions] as well (default setting is
fixing priority).
3) Change the each category of FIX-ENV1to 4 to [2: (15 to 18.5 deg C fixed)] or [3: (to
14.9 deg C fixed)] in service mode (however, the productivity reduces on the paper in
affected category).
4) If the paper mixed mode causes poor fixing performance, specify [Fixing priority] in
[Adjust fixing for different paper sizes] (default is standard).
Or change FIX-ENV5 to [2: (15 to 18.5 deg C fixed)] or [3: (to 14.9 deg C fixed)] in
service mode (however, productivity reduces).
In case of poor productivity;
1) Specify Standard (Productivity priority) in [Adjust fixing of paper source].
2) If the issue is not fixed by step 1), specify [Standard] in [Adjust fixing for natural
conditions].
3) If the issue is not yet fixed by step 2), specify [Productivity priority] in [Adjust fixing for
natural conditions].
Caution:
Be sure to check the output result if [Standard] or [Productivity priority] is specified in
step 2) or 3).
●
Down sequence control
Decrease a print speed or place the machine in the standby status for a specified period of
time depending on the paper type to prevent a fixing failure.
1) Throughput-down for prevention of a fixing failure.
2) For the measure against the paper wrinkle, print start is waited.
3) Switching of temperature control when switching the material.
Timing/Description
1 Thick paper of LTR-size or more (105g
or more), coated paper, emboss paper Extend the paper interval and perform printing.
2
Thin paper (to 63g), coated paper1 (to
90g) or coated paper2 (91 to 120g)
and also, paper width 300mm or more
FAN control is conducted and print start is waited
until the pressure roller center temperature/edge
temperature are in the appropriate relation.
Maximum: 1 min (Timeout: 1 min)
3
A material which cannot be printed in
the current fixing temperature at the
time of material switching is entered.
Stop the job, change the control temperature by the
sequence of changing the fixing temperature control,
and then restart the job.
Thick paper/emboss/coated paper is
printed after plain paper is printed.
Wait until proper temperature control is performed
and then perform printing. (Since the temperature of
the fixing roller decreases (180 - 185 degree C) after
plain paper is printed, it is necessary to increase the
temperature.)
4
Heavy paper (106 to 300g), coated
paper (151 to 240g), special paper
(excluding transparency), special paper
(excluding transparency*)
* = texture paper, rough paper (bond
paper), labels, vellum paper
Pre-rotation is extended by 3 seconds (When the
fixing priority is specified in “adjust fixing of paper
source”, pre-rotation is extended by 18 seconds.).
T-2-71
Summary of Contents for imagePRESS 1110
Page 242: ...3 3 Periodical Service Periodical Service Periodical service item ...
Page 655: ...5 5 Adjustment Adjustment Overview When replacing parts Major adjustment ...
Page 944: ...8 8 Service Mode Service Mode Overview COPIER FEEDER SORTER BOARD Situation Mode ...
Page 1555: ... Service Tools General Circuit Diagram General Timing Chart Operator Maintenance Appendix ...