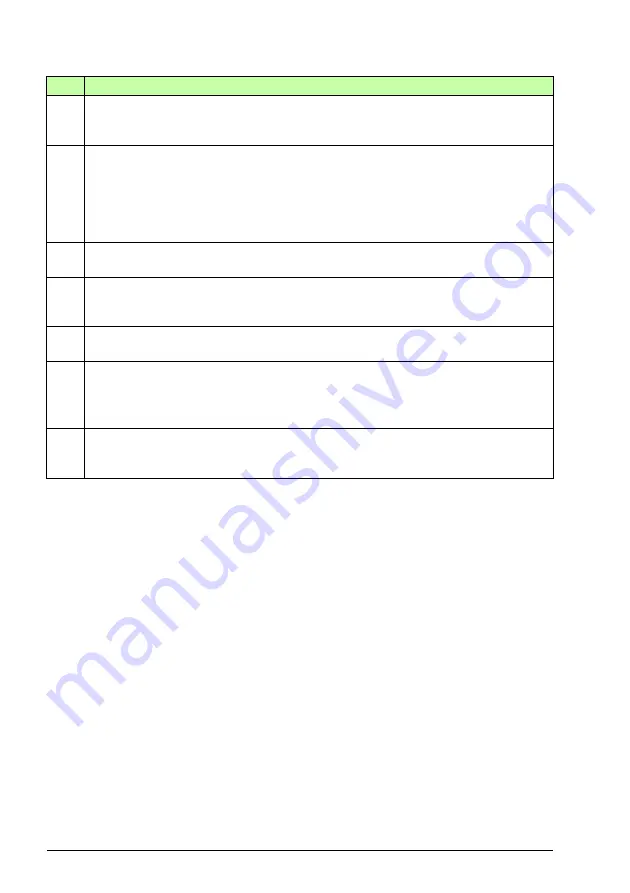
128 Safety functions
4
The Variable SLS request is received again from the safety PLC (for example, 50%).
The FSO sends a request to the drive to ramp down the motor speed to the new speed
limit.
5
After time B has elapsed, the drive starts to ramp down the motor speed. SAR1
parameter
defines the deceleration ramp. The FSO starts to monitor the ramp
with SAR1 parameters (
). The Variable SLS indication goes off (see
also section
How to fine-tune limit hit situations
on page
).
Note
: The FSO continues to monitor the existing Variable SLS limits until the new
speed limit has been reached.
6
The new motor speed has been reached and the FSO starts to monitor the motor
speed according to the new SLS limits. The Variable SLS indication goes on.
7
The Variable SLS request is received again from the safety PLC (100%). The FSO
sends a request to the drive. The FSO starts to monitor the motor speed according to
the new SLS limits.
8
After time B has elapsed and if the motor speed
is lower than the new speed limit, the
drive accelerates the motor speed to the requested speed.
9
The Variable SLS request is removed from the safety PLC (acknowledgement method
is manual or from a safety PLC).
Note
: If automatic acknowledgement is used, the Variable SLS monitoring is also
ended.
10
The Variable SLS is acknowledged and the FSO stops the SLS monitoring. The drive
continues with the speed reference set by the user. The Variable SLS indication
(parameter
) goes off.
Step Description
Summary of Contents for FSO-12
Page 1: ... OPTIONS FOR ABB DRIVES FSO 12 safety functions module User s manual ...
Page 4: ......
Page 12: ...12 Table of contents ...
Page 36: ...36 Safety information and considerations ...
Page 136: ...136 Safety functions ...
Page 196: ...196 PROFIsafe 5 To read the diagnostic messages select the I O Device Diagnostics tab ...
Page 200: ...200 PROFIsafe ...
Page 326: ...326 Start up ...
Page 386: ...386 Dimension drawings ...