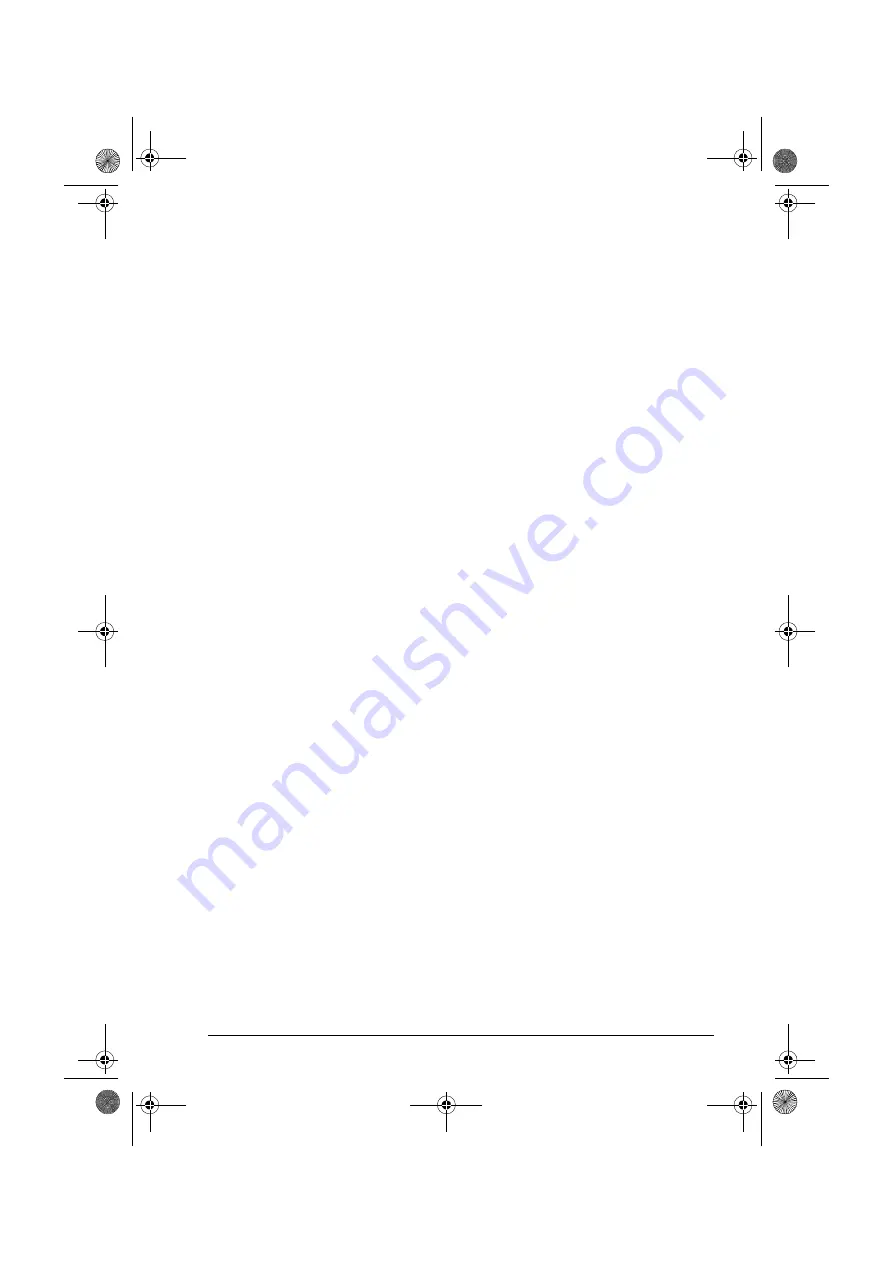
Control macros 79
Terminal sizes:
R0…R5: 0.2…2.5 mm
2
(ter24V, DGND, DCOM, B+, A-)
0.14…1.5 mm
2
(terminals DI, AI, AO, AGND, RO, STO)
R6…R9: 0.14…2.5 mm
2
(all terminals)
Tightening torques: 0.5…0.6 N·m (0.4 lbf·ft)
Notes:
1)
The signal source is powered externally. See the manufacturer’s instructions. To use sensors
supplied by the drive aux. voltage output, see chapter
Electrical installation
, section
Connection examples of two-wire and three-wire sensors
in the
Hardware manual
of the
drive.
2)
Ground the outer shield of the cable 360 degrees under the grounding clamp on the
grounding shelf for the control cables.
3)
Connected with jumpers at the factory.
4)
Only frames R6…R11 have terminals 40 and 41 for external 24 V AC/DC input.
5)
All control boards do not have switches S1, S2 and S3. In that case, select voltage or current
for inputs AI1 and AI2 and output AO1 with parameters
,
and
, respectively.
Input signals
•
Setpoint for PID (AI1)
•
Actual feedback from PID (AI2)
•
Run enable (DI2)
•
Start/Stop selection (DI6)
Output signals
•
Analog output AO1: Output frequency
•
Analog output AO2: Motor current
•
Relay output 1: Running
•
Relay output 2: Fault (-1)
•
Relay output 3: PFC2 (first PFC auxiliary motor)
ACS580 FW.book Page 79 Wednesday, September 21, 2016 9:48 PM