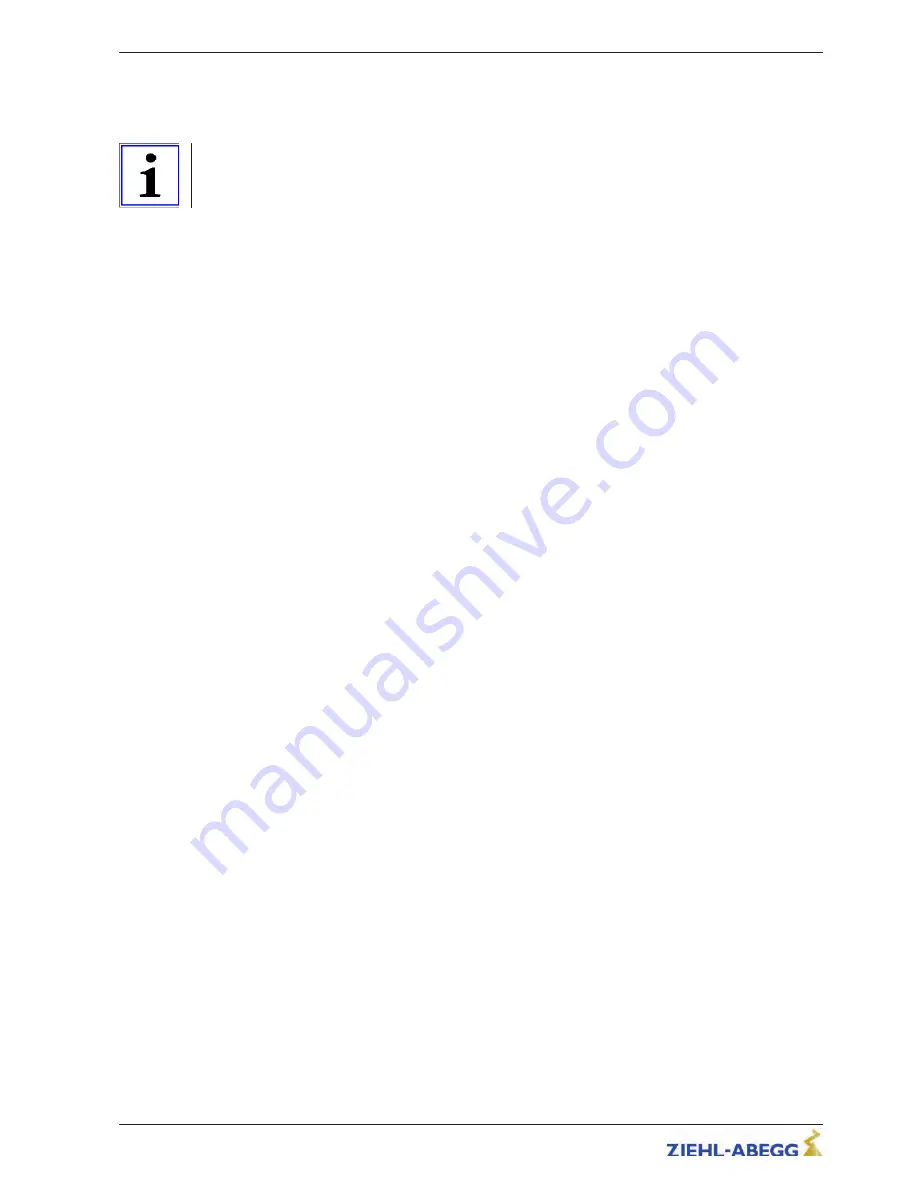
9
Serial communication
9.1
DCP (Drive Control & Position)
Information
To operate the installation with DCP protocol, the frequency inverter must be equipped with the
optional board EM3-ENC-CAN-DCP (Art. No. 357107)!
The DCP-mode enables serial activation of the frequency inverter through an RS485 interface.
Through the bi-directional, serial triggering, the control signals are conducted through a 2- or 3-core
connection line. Generally, the lines X-IN andX-OUT are no longer required, which means the wiring
expenditure is reduced to a minimum.
9.1.1
Electrical connection
The connection is made via the interface X-DCP on the frequency inverter (see chapter "Electrical
Installation / DCP Interface (X-DCP)".
9.1.2
The various DCP protocols
DCP_01
The operating principle is similar to a conventional triggering via the (X-IN) control inputs and (X-OUT)
control outputs. The elevator control transmits the required activation signals (e.g. controller enable,
direction of travel, speed, deceleration point) to the frequency inverter as command bits and receives
the status messages as status bits as return information from the frequency inverter (e.g. signals for
mechanical brakes and motor contactor, speed monitoring and general alarm).
DCP_03
The DCP_03 protocol is an expanded version of the DCP_01 protocol. As compared with the DCP_01
protocol, it has:
•
faster data transmission
•
a faster communication channel
•
an automatic compatibility check between the software in the frequency inverter and software in the
control
DCP_02
The transmission of the command and status bit correspond to the DCP_01-protocol. In addition,
travel is residual path oriented: With the start command, the open loop control determines the path to
the next
fl
oor for the frequency inverter. This path is continuously updated during the drive (residual
path). The frequency inverter adapts its traveling speed to the residual path and the car arrives directly
at the
fl
oor, time optimized and jolt-free without crawl drive. An absolute rotary encoder is required for
setting the residual path!The brake path (shown in the inverter
’
s display) must be manually entered
into the open loop control beforehand.Through the entered brake path and the current residual path
during an incoming call during the trip, the open loop control can decide whether it is still possible to
stop.If no call comes in latest
DCP_04
The DCP_03 protocol is an expanded version of the DCP_01 protocol. As compared with the DCP_01
protocol, it has:
•
faster data transmission
•
a faster communication channel
•
an automatic compatibility check between the software in the frequency inverter and software in the
control
•
a Braking distance transmission: The control unit continuously transmits the braking distance for
the current speed to the open loop control. That means during an incoming call, the trip the open
loop control can decide whether it is still possible to stop.
Original operating instructions
ZETADYN 3C
Serial communication
R-TBA08_03-GB 1619
Part.-No. 00163322-GB
65/204
Содержание ZETADYN 3C
Страница 196: ...Original operating instructions ZETADYN 3C EU declaration of conformity R TBA08_03 GB 1619 Part No 00163322 GB 196 204...
Страница 197: ...Original operating instructions ZETADYN 3C EU declaration of conformity R TBA08_03 GB 1619 Part No 00163322 GB 197 204...
Страница 198: ...Original operating instructions ZETADYN 3C EU declaration of conformity R TBA08_03 GB 1619 Part No 00163322 GB 198 204...
Страница 199: ...Original operating instructions ZETADYN 3C EU declaration of conformity R TBA08_03 GB 1619 Part No 00163322 GB 199 204...
Страница 200: ...Original operating instructions ZETADYN 3C EU declaration of conformity R TBA08_03 GB 1619 Part No 00163322 GB 200 204...
Страница 203: ...Original operating instructions ZETADYN 3C R TBA08_03 GB 1619 Part No 00163322 GB 203 204...