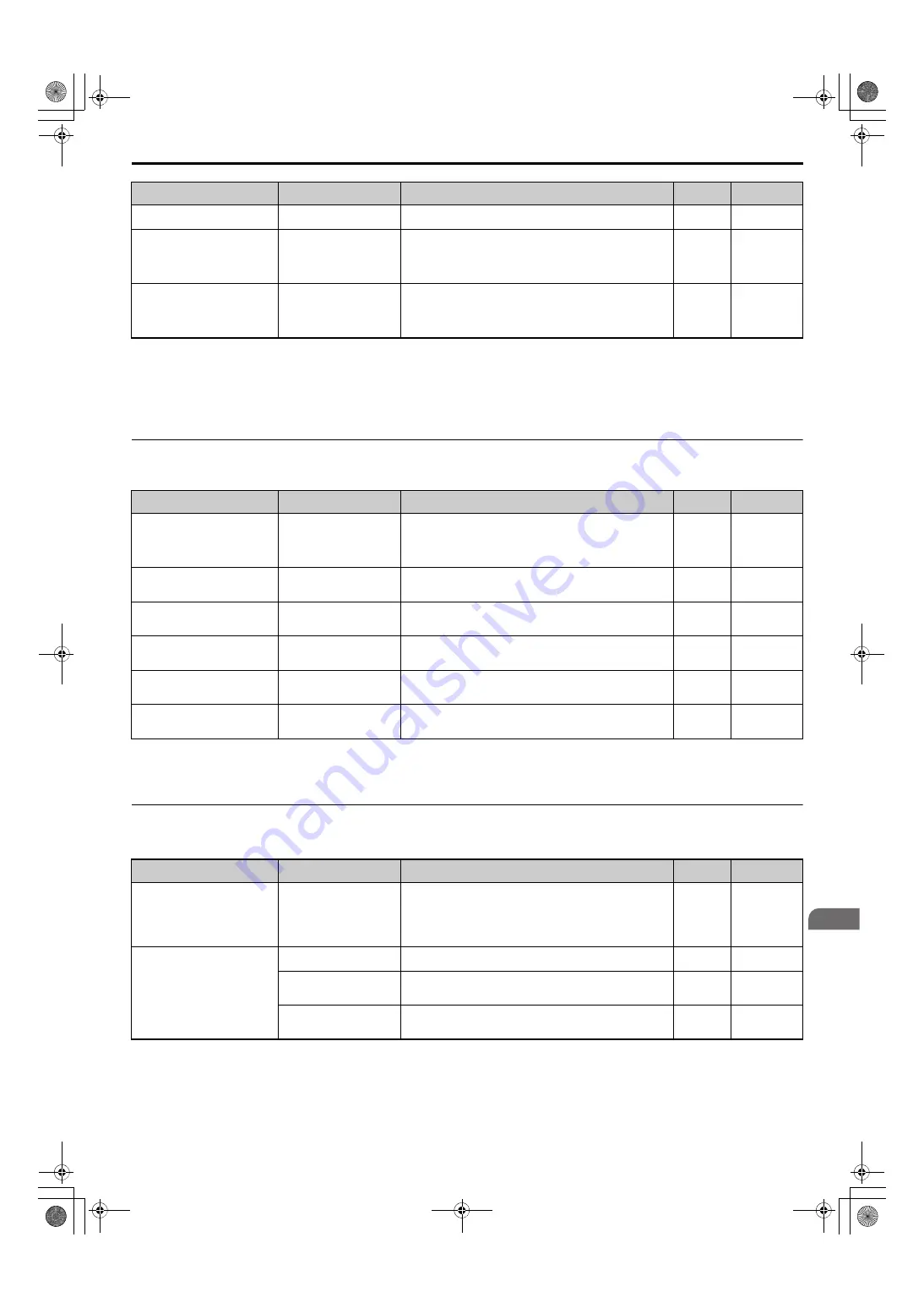
6.2 Motor Performance Fine-Tuning
YASKAWA ELECTRIC
SIEP C710636 02B YASKAWA U1000 Technical Manual
345
T
rou
bl
es
hoot
ing
6
When using OLV, leave the torque compensation gain (C4-01) at its default setting of 1.00.
◆
Fine-Tuning Closed Loop Vector Control
Table 6.3 Parameters for Fine-Tuning the Performance in CLV
◆
Fine-Tuning Open Loop Vector Control for PM Motors
Table 6.4 Parameters for Fine-Tuning Performance in OLV/PM
Poor speed precision during
regenerative operation
Slip Compensation Selection
during Regeneration (C3-04)
Enable slip compensation during regeneration by setting parameter C3-04
= 1.
0
1
• Motor noise
• Motor hunting and oscillation occur
at speeds below 10 Hz
Carrier Frequency Selection
(C6-02)
• If there is too much motor noise, the carrier frequency is too low.
• If motor hunting and oscillation occur at low speeds, reduce the carrier
frequency.
Note:
The default setting for the carrier frequency depends on the Drive
Model Selection (o2-04) and Drive Duty Mode Selection (C6-01).
1 (4 kHz)
0 to 4, F
• Poor motor torque at low speeds
• Poor speed response
• Motor instability at start
Middle Output Frequency
Voltage (E1-08)
Minimum Output Frequency
Voltage (E1-10)
• If motor torque and speed response are too slow, increase the setting.
• If the motor exhibits excessive instability at start-up, reduce the setting.
Note:
The default value is for 200 V class units. Double this value when
using a 400 V class drive. When working with a relatively light load,
increasing this value too much can result in overtorque.
E1-08: 11.0 V
E1-10: 2.0 V
Default setting
±2 V
<1> Default setting value is dependent on parameter A1-02, Control Method Selection, and o2-04, Drive Model Selection.
<2> Default settings change when the Control Method is changed (A1-02) or a different V/f pattern is selected using parameter E1-03.
<3> Default setting value is dependent on parameter o2-04, Drive Model Selection.
<4> Setting range is 1 to 4 and F for models CIMR-U
2
0028 to 2
0248, 4
0011 to 4
0414.
Setting range is 0 and F for models CIMR-U
4
0477 to 4
0930.
Problem
<1> Refer to
C5: Automatic Speed Regulator (ASR) on page 222
for details on Automatic Speed Regulator (ASR).
<2> Default setting value is dependent on parameter o2-04, Drive Model Selection.
<3> Setting range is 1 to 4 and F for models CIMR-U
2
0028 to 2
0248, 4
0011 to 4
0414.
Setting range is 0 and F for models CIMR-U
4
0477 to 4
0930.
Parameter No.
Corrective Action
Default
Suggested
Setting
• Poor torque or speed response
• Motor hunting and oscillation
ASR Proportional Gain 1
(C5-01)
ASR Proportional Gain 2
(C5-03)
• If motor torque and speed response are too slow, gradually increase the
ASR gain setting by 5.
• If motor hunting and oscillation occur, decrease the setting.
• Parameter C5-03 needs to be adjusted only if C5-05 > 0.
• Perform ASR Auto-Tuning if possible
20.00
10.00 to 50.00
• Poor torque or speed response
• Motor hunting and oscillation
ASR Integral Time 1 (C5-02)
ASR Integral Time 2 (C5-04)
• If motor torque and speed response are too slow, decrease the setting.
• If motor hunting and oscillation occur, increase the setting.
• Parameter C5-04 needs to be adjusted only if C5-05 > 0.
0.500 s
0.300 to 1.000 s
Trouble maintaining the ASR
proportional gain or the integral time at
the low or high end of the speed range
ASR Gain Switching Frequency
(C5-07)
Have the drive switch between two different ASR proportional gain and
integral time settings based on the output frequency.
0.0 Hz
0.0 to max output
frequency
Motor hunting and oscillation
ASR Primary Delay Time
Constant (C5-06)
• If motor torque and speed response are too slow, gradually decrease the
setting by 0.01.
• If the load is less rigid and subject to oscillation, increase this setting.
0.004 s
0.004 to 0.020 s
• Motor noise
• Control motor hunting and oscillation
occur at speeds below 3 Hz.
Carrier Frequency Selection
(C6-02)
• If there is too much motor noise, the carrier frequency is too low.
• If motor hunting and oscillation occur at low speeds, reduce the carrier
frequency.
1 (4 kHz)
0 to 4, F
Overshoot or undershoot when the
speed changes with high inertia load.
Feed Forward Control Selection
(n5-01)
Inertia Tuning (T1-01 = 8)
Enable Feed Forward by setting parameter n5-01 = 1 and perform Inertia
Tuning. If Inertia Tuning is not possible, set parameters C5-17, C5-18, and
n5-03 manually.
0
1
Problem
Parameter No.
Corrective Action
Default
Suggested
Setting
Motor performance not as desired
Motor parameters
(E1-
, E5-
)
• Check the settings for base and maximum frequency in the E1-
parameters
• Check E5-
parameters and make sure all motor data has been set
correctly. Be careful not to enter line to line data where single-phase data
is required, and vice versa.
• Perform Auto-Tuning.
–
–
Poor motor torque and speed response
Load Inertia (n8-55)
Adjust parameter n8-55 to meet the load inertia ratio of the machine.
0
Close to the actual
load inertia ratio
Speed Feedback Detection
Control Gain (for PM Motors)
(n8-45)
Decrease the speed feedback detection control gain (n8-45).
0.8
Decrease in
decrements of 0.05
Torque Compensation Gain
(C4-01)
Enable torque compensation.
Note:
Setting this value too high can cause overcompensation and motor
oscillation.
0
1
Problem
Parameter No.
Corrective Action
Default
Suggested
Setting
SIEP_C710636_02B_1_0.book 345 ページ 2015年11月25日 水曜日 午後4時56分