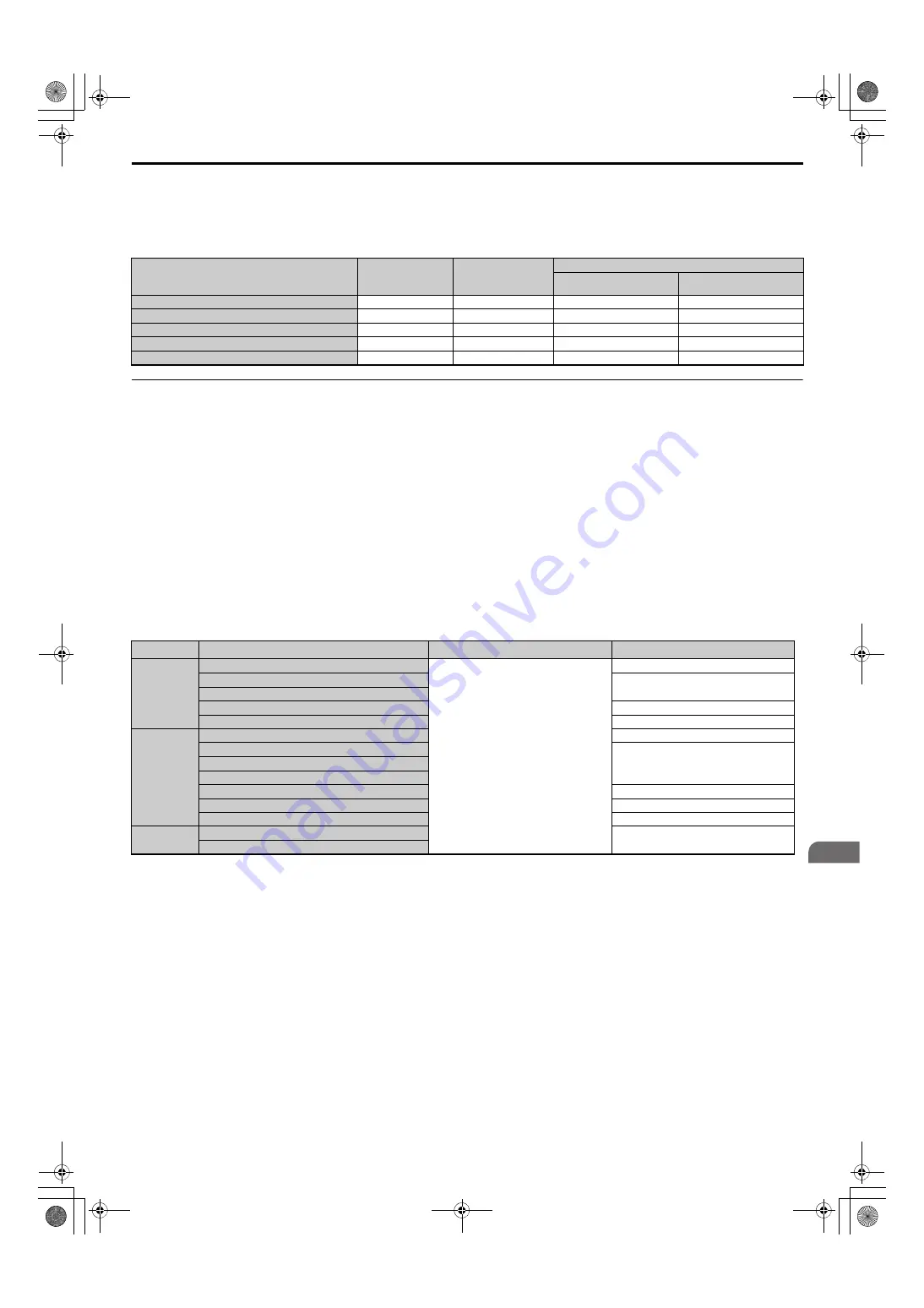
4.7 Auto-Tuning
YASKAWA ELECTRIC
SIEP C710636 02B YASKAWA U1000 Technical Manual
157
St
ar
t-
Up Pr
ogr
ammi
ng
&
O
p
er
at
io
n
4
explains that data that must be entered in order to perform the Inertia Tuning and ASR Gain Auto-Tuning.
Auto-Tuning for Permanent Magnet Motors on page 155
Table 4.26 Auto-Tuning Input Data
◆
Before Auto-Tuning the Drive
Check the items below before Auto-Tuning the drive.
■
Basic Auto-Tuning Preparations
• Auto-Tuning requires the user to input data from the motor nameplate or motor test report. Make sure this data is
available before Auto-Tuning the drive.
• For best performance, the drive input supply voltage must be greater than the motor rated voltage.
Note:
Better performance is possible when using a motor with a base voltage that is 20 V (200 V class models) or 40V (400 V class
models) lower than the input supply voltage. This is particularly important when operating the motor above 90% of base speed,
where high torque precision is required.
• To cancel Auto-Tuning, press the STOP key on the digital operator.
• When using a motor contactor, make sure it is closed throughout the Auto-Tuning process.
• When using Auto-Tuning for motor 2, make sure motor 2 is connected to the drive output when performing the tuning.
•
describes digital input and output terminal operation while Auto-Tuning is performed.
Table 4.27 Digital Input and Output Operation During Auto-Tuning
■
Notes on Rotational Auto-Tuning
• To achieve optimal performance from Rotational Auto-Tuning, the load should be decoupled from the motor.
Rotational Auto-Tuning is best suited for applications requiring high performance over a wide speed range.
• If motor and load can not be decoupled, reduce the load so that it is no greater than 30% of the rated load. Performing
Rotational Auto-Tuning with a higher load will set motor parameters incorrectly, and can cause irregular motor
rotation.
• Ensure the motor-mounted brake is fully released if installed.
• Connected machinery should be allowed to rotate the motor.
NOTICE:
Make sure that the motor and the load are not connected when performing Auto-Tuning. Failure to comply may cause
damage to equipment or injury to personnel.
NOTICE:
Electrical Shock Hazard. When executing Auto-Tuning, voltage is applied to the motor even before it rotates. Do not touch
the motor until Auto-Tuning is completed. Failure to comply may result in injury from electrical shock. If Rotational Auto-Tuning is
performed, the motor will remain stopped for approximately one minute with power applied and then the motor will rotate for one
minute.
Input Value
Input Parameter
Unit
Tuning Type (T1-01 or T2-01)
8
Inertia Tuning
9
ASR Gain Tuning
Control mode
A1-02
–
3, 7
3, 7
Test signal frequency
T3-01
Hz
YES
YES
Test signal amplitude
T3-02
rad
YES
YES
Motor inertia
T3-03
kgm
2
YES
YES
System response frequency
T3-04
Hz
N/A
YES
Motor Type
Auto-Tuning Type
Digital Input
Digital Output
IM Motor
Rotational Auto-Tuning
Digital input functions are disabled.
Functions the same as during normal operation
Stationary Auto-Tuning 2
Maintains the status at the start of Auto-Tuning
Stationary Auto-Tuning for Line-to-Line Resistance
Rotational Auto-Tuning for V/f Control
Functions the same as during normal operation
Stationary Auto-Tuning 3
Maintains the status at the start of Auto-Tuning
PM Motor
PM Motor Parameter Settings
Digital output functions are disabled.
PM Stationary Auto-Tuning
Maintains the status at the start of Auto-Tuning
PM Stationary Auto-Tuning for Stator Resistance
Z Pulse Offset Tuning
Back EMF Constant Tuning
Functions the same as during normal operation
High Frequency Injection Parameter Tuning
Digital output functions are disabled.
PM Rotational Auto-Tuning
Functions the same as during normal operation
IM and PM
Motors
Inertia Tuning
Functions the same as during normal operation
ASR Gain Auto-Tuning
SIEP_C710636_02B_1_0.book 157 ページ 2015年11月25日 水曜日 午後4時56分