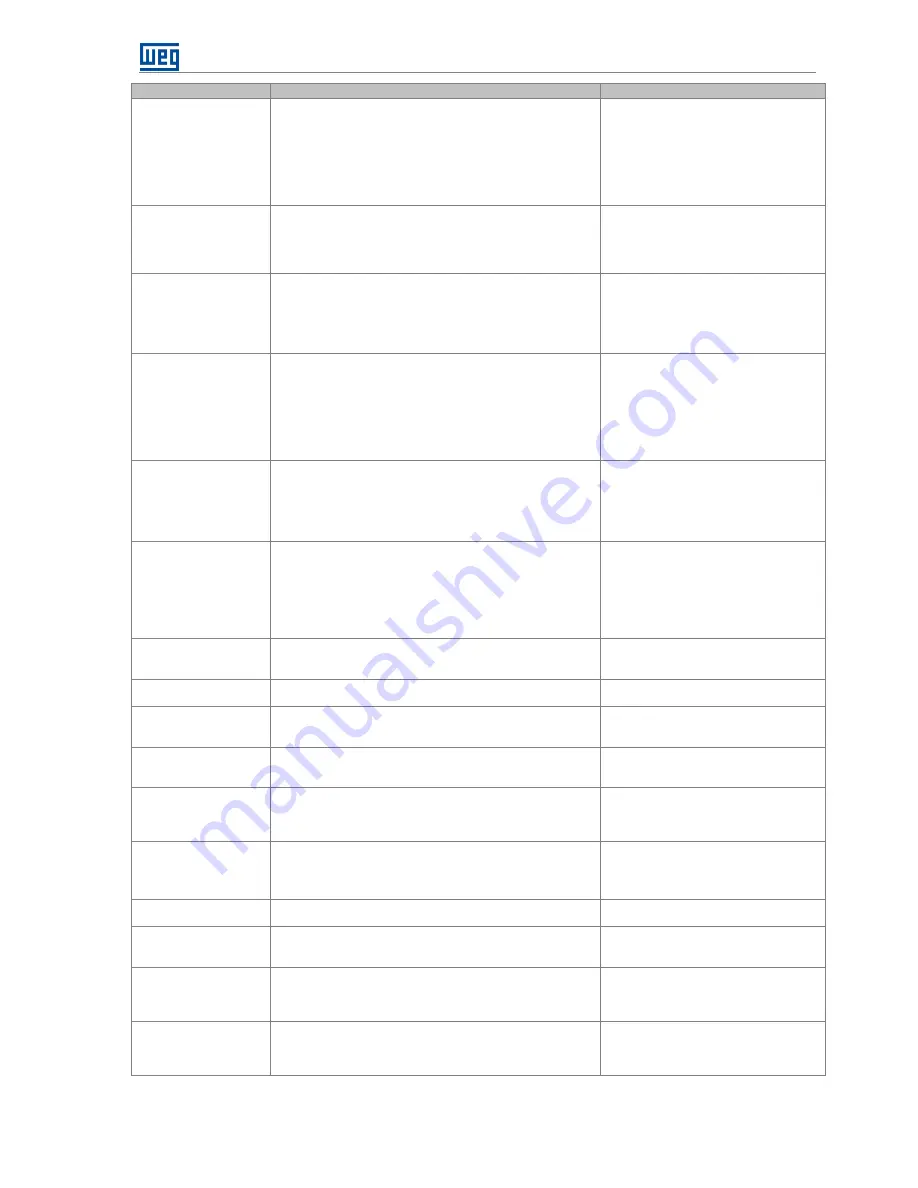
Faults and Alarms
.
CTW900 | 25
Fault/Alarm
Description
Possible Causes
F067:
Incorrect Polarity of the
Tacho or Encoder
■
Actuates when the polarity of the feedback by DC tacho or
encoder is different from the output voltage signal (EMF).
Note: This fault will be active only if the converter is configured
as Antiparallel (P0298=1) and the feedback is not set for EMF
(P0202
0).
It is also possible to disable the protection setting P0352=1.
■
Wiring of the tacho or encoder cables
inverted.
F070:
Field Overcurrent
■
Actuates when the field circuit current remains above the value
defined in P0359 (in percentage of P0404) for over 2 seconds.
( ) = (100
% + 0359)
×
0404
■
Field regulator gains too high (P0175 and
P0176).
■
Overcurrent level set too low (P0359).
F071:
Armature Overcurrent
■
Actuates when the armature circuit current remains above the
value defined in P0135 for over 2 seconds.
■
Current regulator gains too high (P0167
and P0171).
■
Maximum output current set too low
(P0135).
■
Fault on some of the thiristors of the
armature.
F072:
Motor Overload
■
Actuates when the output current exceeds the limit defined in
P0156 for a period longer than the setting in P0158.
Note: In case the output current is below the value of P0156, but
above the value of P0157, the actuation time will be give by:
072
( ) = ( 0156 ÷ 0003)
×
0158
■
Settings of P0156, P0157 and P0158
too low for the load used.
■
Overload on the motor shaft.
F074:
Field Missing
■
Actuates when field current remains below the value defined in
P0177 for a period longer than the time set in P0356.
■
Motor field not connected.
■
Field input fuses open.
■
Setting of P0177 incompatible with the
motor field.
■
Fault in the field supply when supplied
externally by means of connector X3.
F077:
Motor Stalled
■
Actuates when the armature current remains above the limit
defined in P0355 (in percentage of P0295) and speed below
P0139 for a period longer than the time set in P0137.
( ) = 0355
×
0295
Note: If P0355 is set for 0, the protection will be disabled.
■
Motor shaft locked.
■
Incorrect settings of P0355 and/or
P0139.
F079:
Fault in the Encoder
Signals
■
Actuates when a fault in the encoder pulses occurs.
■
Wiring between the encoder and
interface accessory broken.
■
Encoder defective.
F080:
CPU Fault (Watchdog)
■
Actuation of the microcontroller watchdog timer.
■
Electric noise.
■
Converter not grounded.
F082:
Copy Function Fault
■
Actuates when a fault in the copy of parameters by the keypad
(HMI) occurs.
■
Attempt to copy parameters from the
keypad (HMI) to a converter with a different
software version.
F084:
Self-Diagnose Fault
■
Actuates when an internal fault is detected on the converter.
■
Defect on the internal circuits of the
product.
■
Accessory modules poorly connected.
A088:
Communication with
keypad (HMI) Fault
■
Signals when the communication between the keypad (HMI)
and the control board is interrupted.
■
Poor contact on the keypad (HMI) cable.
■
Electric noise on the installation.
A090:
External Alarm
■
Signals an external alarm through a digital input (DI).
Note: It is necessary to set some DI for "Without External Alarm”
■
Digital input set for “Without External
Alarm” is open (0V).
F091:
External Fault
■
Actuates when some digital input set for “Without External
Fault” is open.
■
Digital input set for “Without External
Fault” is open (0V).
F098:
Invalid Offset Ia/If
■
Actuates when the measurement circuit of the armature
current (Ia) or field current (If) displays an abnormal value during
the converter initialization.
■
Defect on the measurement circuits of
armature current or field current.
F099:
Invalid Offset Ua/Tacho
■
Actuates when the measurement circuit of the armature
voltage (Ua) or tacho voltage displays an abnormal value during
the converter initialization.
■
Power-up of the converter with the
motor running.
■
Defect on the measurement circuits of
armature or tacho voltage.
A128:
Serial Communication
Timeout
■
Signals when the converter stops receiving valid telegrams
within a certain period.
Note: It may be disable by setting P0314 = 0.0s.
■
Poor installation of the communication
and/or ground cables.
■
Master sending new telegrams in a
period longer than the setting in P0314.
Содержание CTW900
Страница 2: ......
Страница 52: ...Installation and Connection 52 CTW900 Figure 5 16 Connections in XC1 for configuration 4...
Страница 69: ...Detailed Description of the Parameters CTW900 69 Figure 7 3 Block diagram of the speed reference...
Страница 135: ...Detailed Description of the Parameters CTW900 135 Figure 7 21 Block diagram of the control of the CTW900...