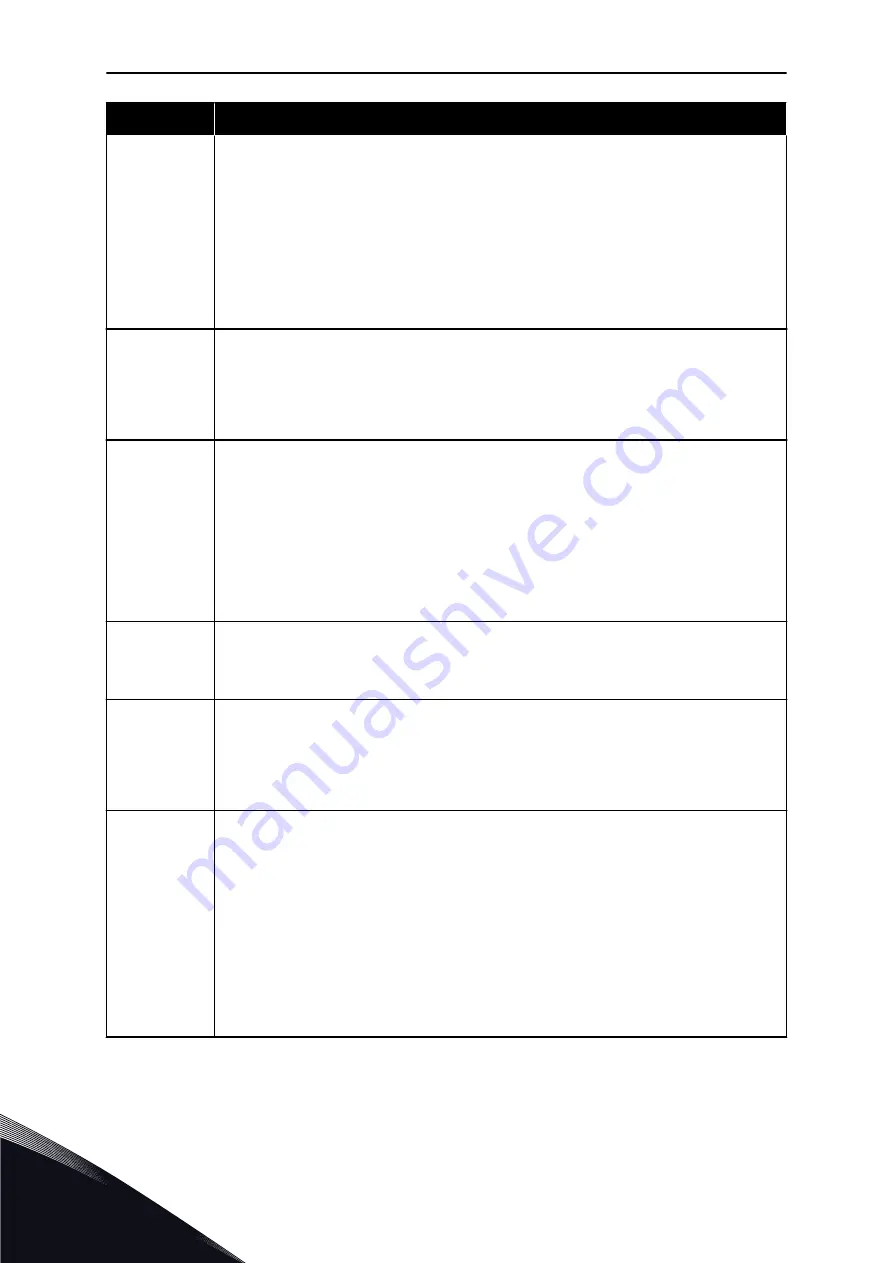
Step
Action
1
Examine the wiring.
•
See the correct power cabling (mains cable, motor cable) of the drive in Installation Man-
ual.
•
See the correct control cabling (I/O, PID feedback sensor, communication) in Fig. 18
Electric wiring diagramme of the Multi-pump (multidrive) system, example 1A and in Fig. 16
The default control connections of Multi-pump (multidrive) application.
•
If redundancy is necessary, make sure that the PID feedback signal (by default: AI2) is
connected to a minimum of 2 drives. See the wiring instructions in Fig. 18 Electric wiring
diagramme of the Multi-pump (multidrive) system, example 1A.
2
Do a power-up of the drive and start the parametrisation.
•
Start the parametrisation with the drives that have the PID feedback signal connected.
These drives can operate as the master of the Multi-pump system.
•
You can do the parametrisation with the keypad or PC the tool.
3
Select the Multi-pump (multidrive) application configuration with parame-
ter P1.2.
•
Most of the Multi-pump-related settings and configurations are made automatically,
when the Multi-pump (multidrive) application is selected with parameter P1.2 Applica-
tion (ID 212). See 2.5 Multi-pump (multidrive) application wizard.
•
If you use the keypad for the parametrisation, the Application wizard starts when param-
eter P1.2 Application (ID 212) is changed. The Application wizard helps you with Multi-
pump-related questions.
4
Set the motor parameters.
•
Set the motor nameplate parameters specified by the rating plate of the motor.
5
Set the total number of drives used in the Multi-pump system.
•
This value is set with parameter P1.35.14 Quick Setup Parameter Menu.
•
The same parameter is in the menu Parameters -> Group 3.15 -> P3.15.2
•
By default, the Multi-pump system has 3 pumps (drives).
6
Select the signals that are connected to the drive.
•
Go to parameter P1.35.16 (Quick Setup Parameter Menu).
•
The same parameter is in the menu Parameters -> Group 3.15 -> P3.15.4.
•
If the PID feedback signal is connected, the drive can operate as the master of the Multi-
pump system. If the signal is not connected, the drive operates as a slave unit.
•
Select Signals connected, if the start and the PID feedback signals (the pressure sensor,
for example) are connected to the drive.
•
Select Start signal only, if only the start signal is connected to the drive (the PID feedback
signal is not connected).
•
Select Not connected, if the start or the PID feedback signals are not connected to the
drive.
VACON · 322
PARAMETER DESCRIPTIONS
10
LOCAL CONTACTS: HTTP://DRIVES.DANFOSS.COM/DANFOSS-DRIVES/LOCAL-CONTACTS/
Содержание 100 flow
Страница 1: ...vacon 100 flow ac drives application manual ...
Страница 2: ......
Страница 6: ...VACON 6 LOCAL CONTACTS HTTP DRIVES DANFOSS COM DANFOSS DRIVES LOCAL CONTACTS ...