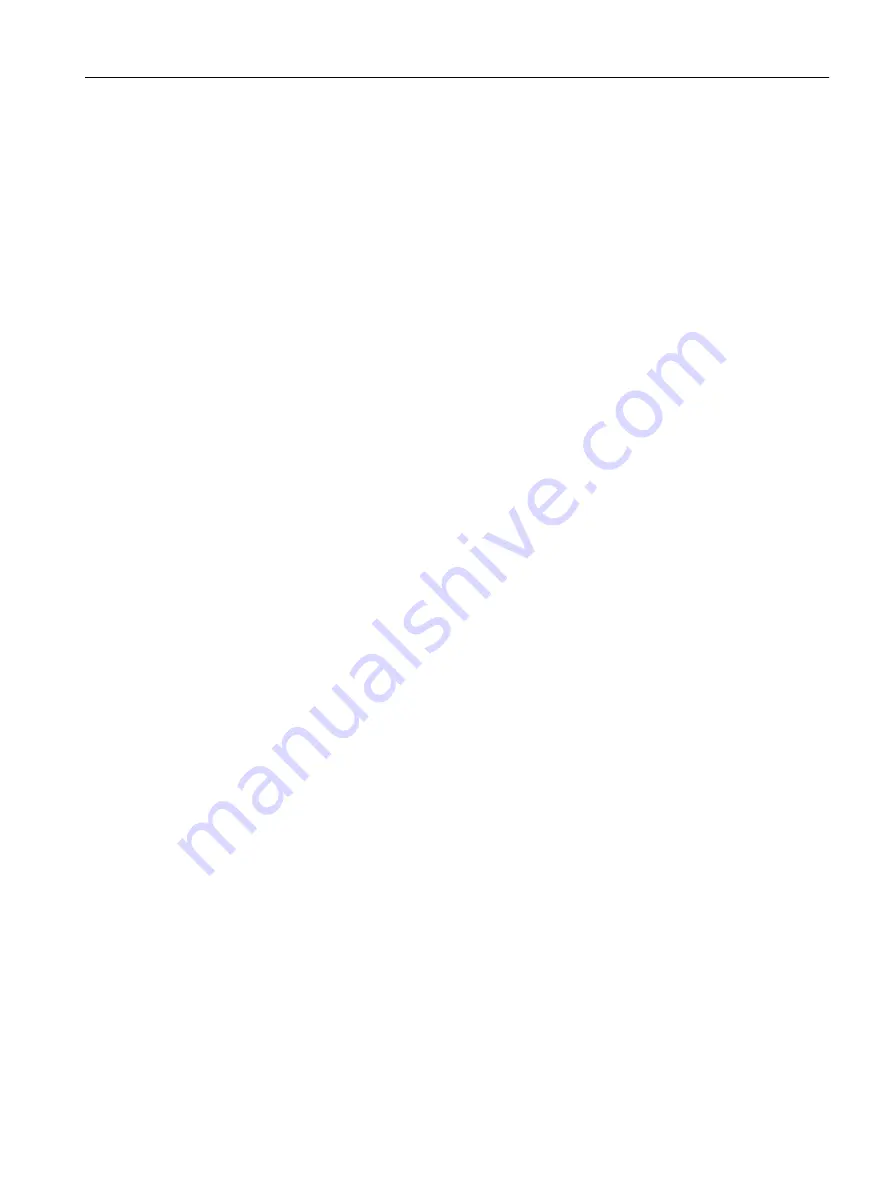
7.7
Creating and testing axes
7.7.1
Overview of SIMOTION engineering
Performing engineering with SIMOTION SCOUT
You use the engineering software to configure the individual axes and define the project
sequence by means of programs.
1. First, run through the axis wizard to configure the axes and interconnect to the real drive
(e.g. SINAMICS Integrated).
2. Provided you have completed the configuration at the drive end, we strongly recommend
for faster working that the SINAMICS Integrated is deactivated via "Target system" ⇒
"Select target device".
3. Complete your SIMOTION application, for example, by creating axis functions and
SIMOTION execution programs.
4. Compile the project and download it to the SIMOTION D4x5‑2.
7.7.2
Creating an axis with the axis wizard
Overview
The TO axis provides the user with the technological functionality and the interface to the drive/
actuator. The TO axis processes the motion control commands from the user program (e.g.
MCC) and coordinates the interface to the drives. It executes control and motion commands
and indicates statuses and actual values. The TO axis communicates with an actuator (drive
or hydraulic valve) via a fieldbus system (PROFIBUS or PROFINET via PROFIdrive protocol)
or via a direct setpoint interface (analog ±10 V or pulse/direction).
When running through the axis wizard, the basic settings are made for the axis and the TO axis
interconnected to a drive (e.g. SINAMICS Integrated). Further options are available when "Use
symbolic assignment" has been activated:
● A real axis is interconnected to an already configured drive
● A real axis including drive is created via the axis wizard and the drive interconnected to the
axis
● A real axis is created without assigning this to a drive (assignment is made later)
Commissioning (software)
7.7 Creating and testing axes
SIMOTION D4x5-2
Commissioning and Hardware Installation Manual, 03/2018, A5E33441636B
257