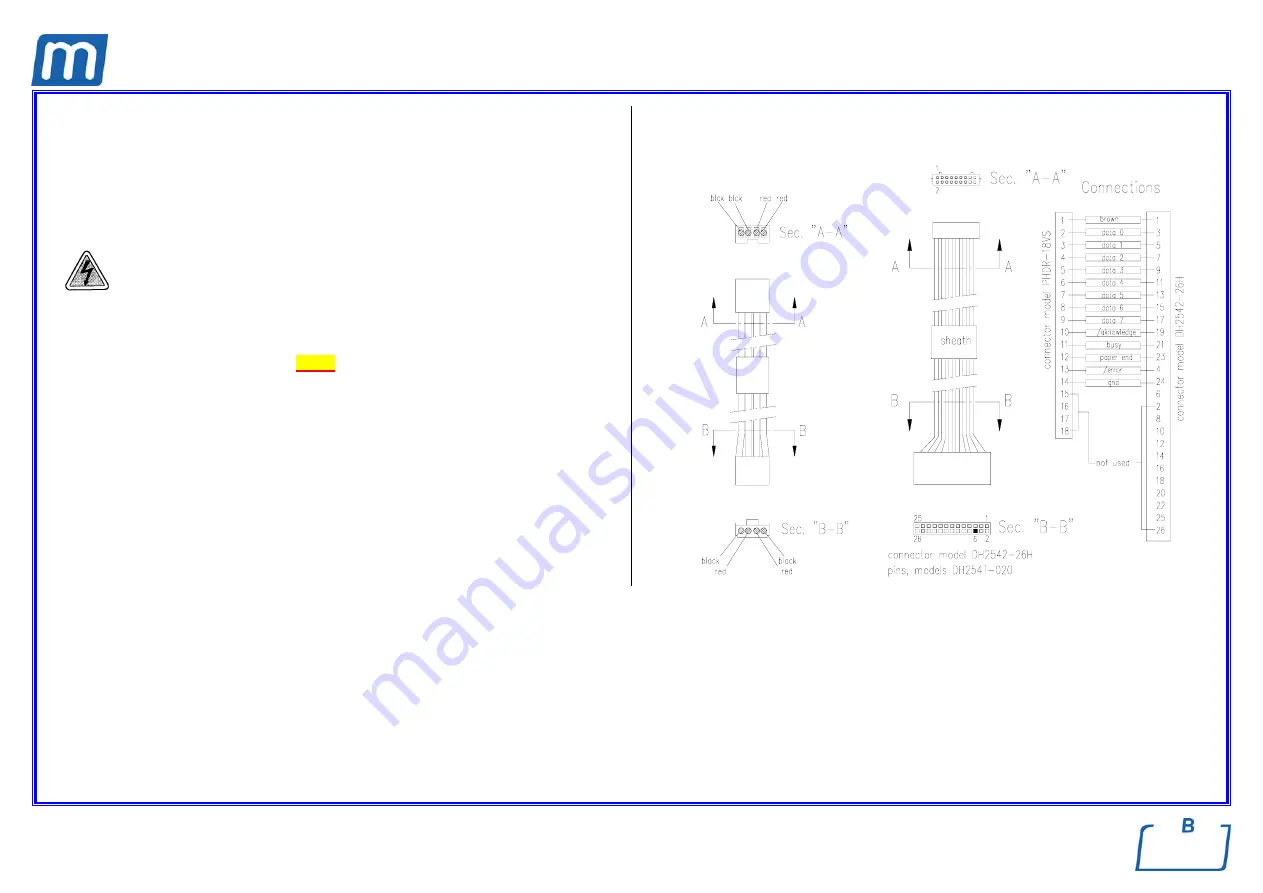
Rev. 1
Card Gr5-
5
PRINTER SIGNAL
A#2BP2570000
PRINTER POWER SUPPLY
A#2BP2580000
Before servicing, switch off the equipment and unplug the power
supply cable from the mains socket
1. Remove the covers (see card
Gr7-1
);
2. Disconnect the signal and power supply wirings from the printer, CPU board
and printer board;
3. Replace the wiring, restore connections and assembly all items proceeding in
reverse order as above;
4. Run a sterilization cycle.
Содержание millennium B
Страница 1: ...Rev 1...
Страница 202: ...Rev 1 Gr2 INDEX GROUP 2 ELECTROVALVES EV1 VALVE 1 EV2 VALVE 2 EV3 VALVE 3 EV4 VALVE 4 EV5 VALVE 5...
Страница 208: ...Rev 1 Gr3 INDEX GROUP 3 PUMPS STEAM GENERATOR WATER PUMP 1 AUTOMATIC WATER FILLING PUMP 2 VACUUM DOUBLE PUMP 3...
Страница 243: ...Rev 1 Gr7 INDEX GROUP 7 COVERS FRAME COVER 1 DOOR COVER 2 FRONT FRAME 3 SERVICE DOOR 4...
Страница 270: ...Rev 1 Page 4 4 HYDRAULIC DIAGRAM CHAMBER HEAT EXCHANGER WP VP Main tank...
Страница 271: ...Rev 1 Page 4 5 EXPLODED VIEWS TABLE 1...
Страница 272: ...Rev 1 Page 4 6 TABLE 2...
Страница 273: ...Rev 1 Page 4 7 TABLE 3...
Страница 274: ...Rev 1 Page 4 8 TABLE 4...
Страница 275: ...Rev 1 Page 4 9 TABLE 5...
Страница 276: ...Rev 1 Page 4 10 TABLE 6...