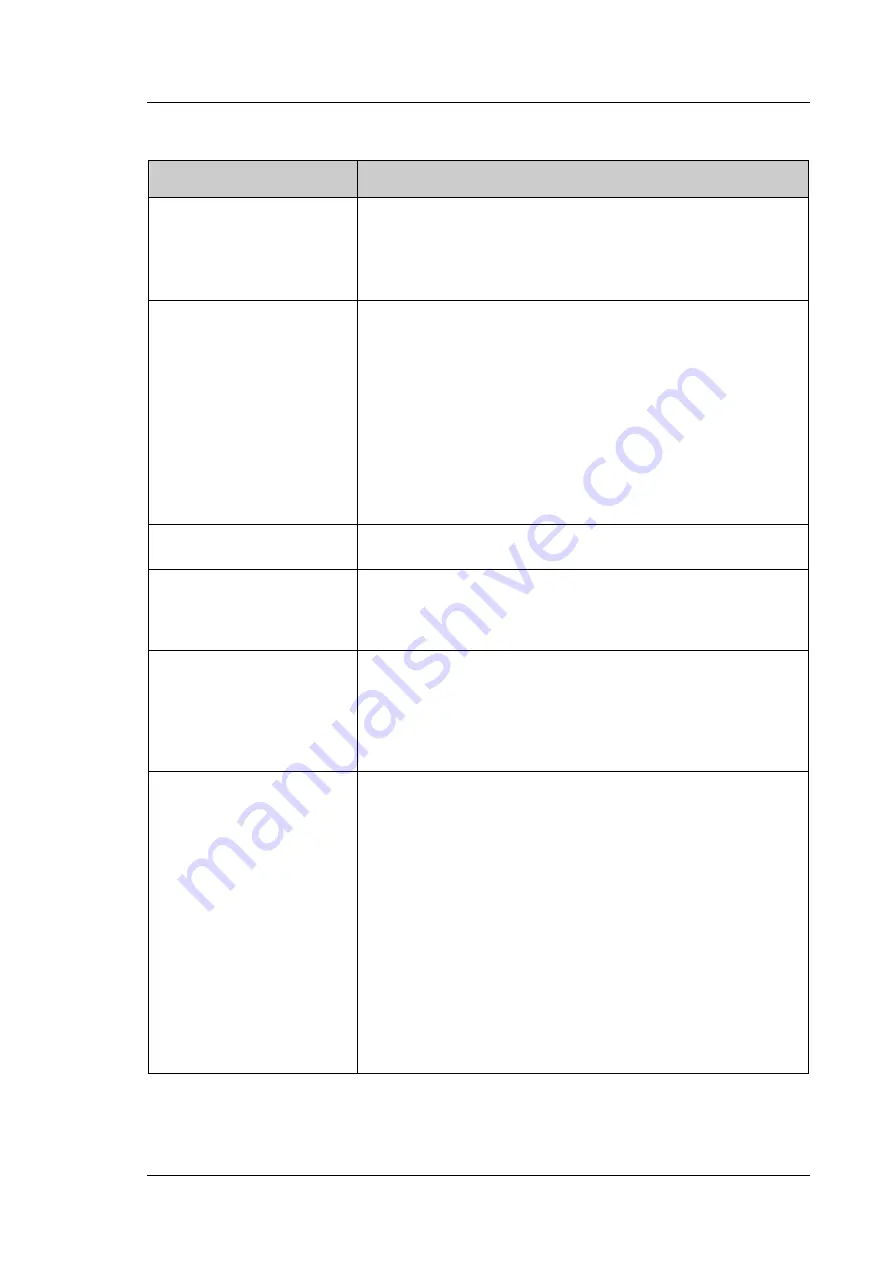
UltiMate 3000 Series:
SD, RS, and BM Pumps
Operating Instructions
Page
107
Error Message
Remedial Action
Leak detected
When this message appears, the flow is automatically turned off after
180 seconds.
The leak sensor has reported a leak.
Find and eliminate the source for the leak. Dry the leak sensor and
tray (
page 124).
Motor current too large
The motor current is too high when the pump is running.
The flow path before the transducer for the system pressure may be
blocked. Make sure that neither the capillary from the working
cylinder to the equilibration cylinder nor the capillary to the purge
unit is blocked. Replace the capillaries if necessary.
Verify that the check valve cartridges are installed in the direction of
flow (
page 128).
Inspect the purge valve for indications of blockage. Replace the
purge valve screw if necessary (
The motor may be defective.
No abortable command was
executing.
An attempt was made to perform an Abort command. However, no
action or command was being executed that can be aborted.
Position error
A position error is reported for the pump.
Turn the pump off and on again by pressing the power switch on the
rear of the module. If the message appears again, contact Dionex
Service.
Pressure buildup during
maintenance operation.
Please open the purge valve.
A pressure of more than 0.5 MPa built up during piston and/or piston
seal maintenance. Open the purge valve to reduce the pressure. If you
are operating an
ISO-3100BM, observe the precautions on page 90.
If the message appears during the internal maintenance procedure
(
page 99), perform an additional purge cycle (
page 54).
Pressure fallen below lower
limit
The solvent reservoirs are empty. Fill the reservoirs and purge the
system
(
.
There are air bubbles in solvent line. Check the filter frits; purge the
system (
The solvent emits gas when mixing. Degas the solvent. Check the
degasser.
There is a leak in the system. Find and eliminate the source for the
leak. Tighten loose connections.
One of the check valves is defective. Clean or replace the valve
cartridges (
page 128). Purge the system (
page
).
The lower pressure limit cannot be reached for the specified flow.
The main task of the lower pressure limit is to monitor the system for
leakage. Leakage may occur especially at the fittings and or screw
joints, the switching valve in the autosampler, or the piston seals.
Содержание UltiMate 3000 Series
Страница 2: ...UltiMate 3000 Series SD RS and BM Pumps Operating Instructions ...
Страница 4: ...UltiMate 3000 Series SD RS and BM Pumps Page II Operating Instructions ...
Страница 5: ...UltiMate 3000 Series SD RS and BM Pumps Operating Instructions Page III ...
Страница 6: ...UltiMate 3000 Series SD RS and BM Pumps Page IV Operating Instructions ...
Страница 7: ...UltiMate 3000 Series SD RS and BM Pumps Operating Instructions Page V ...
Страница 8: ...UltiMate 3000 Series SD RS and BM Pumps Page VI Operating Instructions ...
Страница 14: ...UltiMate 3000 Series SD RS and BM Pumps Page vi Operating Instructions ...
Страница 24: ...UltiMate 3000 Series SD RS and BM Pumps Page 10 Operating Instructions ...
Страница 58: ...UltiMate 3000 Series SD RS and BM Pumps Page 44 Operating Instructions ...
Страница 74: ...UltiMate 3000 Series SD RS and BM Pumps Page 60 Operating Instructions ...
Страница 116: ...UltiMate 3000 Series SD RS and BM Pumps Page 102 Operating Instructions ...
Страница 136: ...UltiMate 3000 Series SD RS and BM Pumps Page 122 Operating Instructions ...
Страница 200: ...UltiMate 3000 Series SD RS and BM Pumps Page 186 Operating Instructions ...
Страница 204: ...UltiMate 3000 Series SD RS and BM Pumps Page 190 Operating Instructions ...
Страница 228: ...UltiMate 3000 Series SD RS and BM Pumps Page 214 Operating Instructions ...
Страница 236: ...UltiMate 3000 Series SD RS and BM Pumps Page 222 Operating Instructions ...