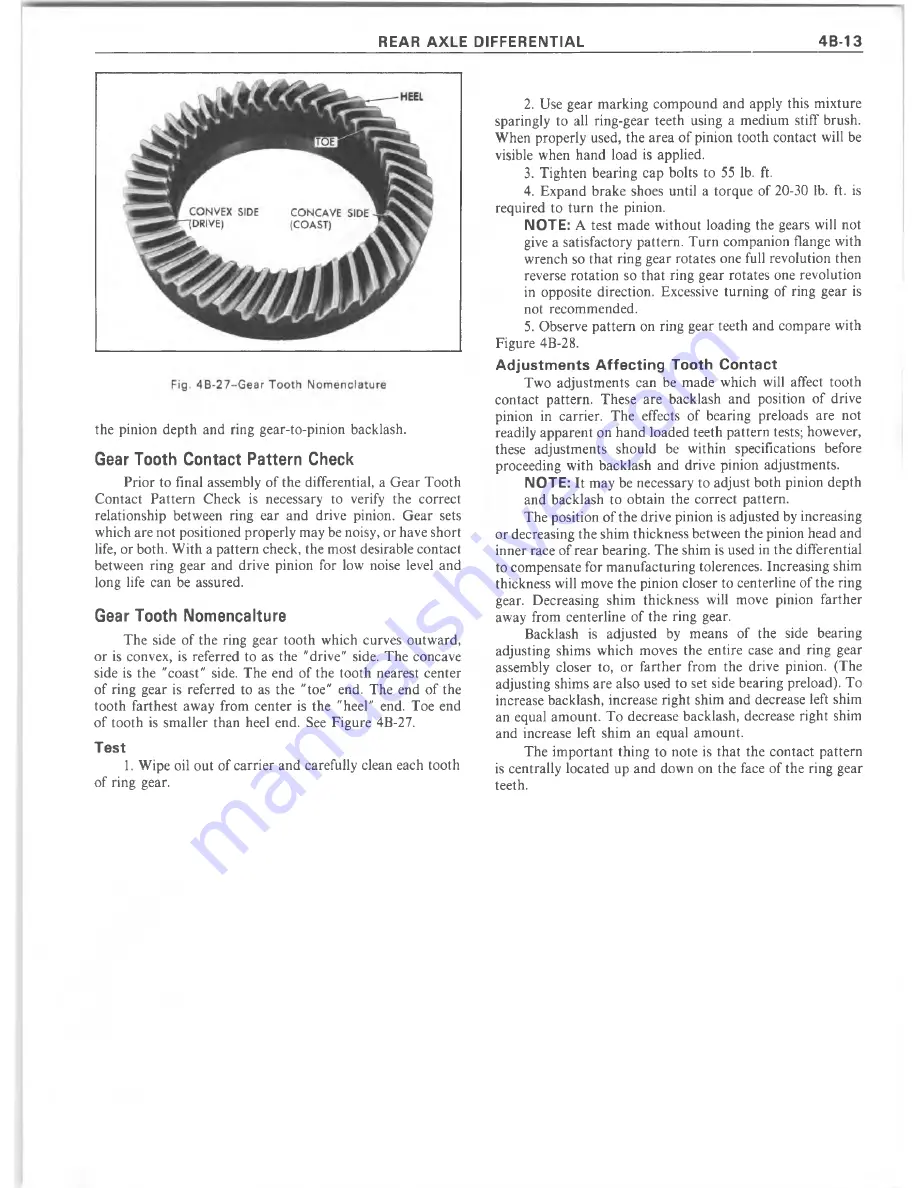
REAR AXLE DIFFERENTIAL
4B-13
the pinion depth and ring gear-to-pinion backlash.
Gear Tooth Contact Pattern Check
Prior to final assembly of the differential, a G ear Tooth
Contact P attern Check is necessary to verify the correct
relationship between ring ear and drive pinion. G ear sets
which are not positioned properly may be noisy, or have short
life, or both. W ith a pattern check, the most desirable contact
between ring gear and drive pinion for low noise level and
long life can be assured.
Gear Tooth Nomencalture
The side of the ring gear tooth which curves outw ard,
or is convex, is referred to as the "drive" side. The concave
side is the "coast" side. The end of the tooth nearest center
of ring gear is referred to as the "toe" end. The end of the
tooth farthest away from center is the "heel" end. Toe end
of tooth is sm aller than heel end. See Figure 4B-27.
Test
1.
Wipe oil out of carrier and carefully clean each tooth
of ring gear.
2. Use gear m arking com pound and apply this m ixture
sparingly to all ring-gear teeth using a medium stiff brush.
W hen properly used, the area of pinion tooth contact will be
visible when hand load is applied.
3. Tighten bearing cap bolts to 55 lb. ft.
4. Expand brake shoes until a torque of 20-30 lb. ft. is
required to turn the pinion.
NOTE:
A test m ade w ithout loading the gears will not
give a satisfactory pattern. Turn companion flange with
wrench so that ring gear rotates one full revolution then
reverse rotation so that ring gear rotates one revolution
in opposite direction. Excessive turning of ring gear is
not recommended.
5. Observe pattern on ring gear teeth and compare with
Figure 4B-28.
Adjustments Affecting Tooth Contact
Two adjustm ents can be made which will affect tooth
contact pattern. These are backlash and position of drive
pinion in carrier. The effects of bearing preloads are not
readily apparent on hand loaded teeth pattern tests; however,
these adjustm ents should be within specifications before
proceeding with backlash and drive pinion adjustments.
NOTE:
It may be necessary to adjust both pinion depth
and backlash to obtain the correct pattern.
The position of the drive pinion is adjusted by increasing
or decreasing the shim thickness between the pinion head and
inner race of rear bearing. The shim is used in the differential
to compensate for m anufacturing tolerences. Increasing shim
thickness will move the pinion closer to centerline of the ring
gear. Decreasing shim thickness will move pinion farther
away from centerline of the ring gear.
Backlash is adjusted by means of the side bearing
adjusting shims which moves the entire case and ring gear
assembly closer to, or farther from the drive pinion. (The
adjusting shims are also used to set side bearing preload). To
increase backlash, increase right shim and decrease left shim
an equal am ount. To decrease backlash, decrease right shim
and increase left shim an equal am ount.
The im portant thing to note is that the contact pattern
is centrally located up and down on the face of the ring gear
teeth.
Содержание 1977 10 Series
Страница 1: ......
Страница 2: ......
Страница 4: ......
Страница 6: ......
Страница 42: ......
Страница 65: ...STEERING 3B 23 Fig 3B 65 M easure Back and Remark Housing Fig 3B 67 Tighten Lock Nut...
Страница 86: ...4B 14 OVERHAUL MANUAL Fig 4B 28 Gear Teeth C ontact Pattern Check...
Страница 125: ...REAR AXLE DIFFERENTIAL 4B 53 Fig 18E Gear Teeth Contact Pattern Check...
Страница 156: ......
Страница 164: ...4C 8 OVERHAUL MANUAL Fig 4C 12 Gear Tooth Pattern Contact Pattern...
Страница 166: ......
Страница 194: ......
Страница 284: ......
Страница 320: ......
Страница 322: ...400 7A 2 OVERHAUL MANUAL Fig 7A 1C Side Cross Section Typical...
Страница 444: ...7B 64 OVERHAUL MANUAL Fig 7B 11S M od el 2 03 Transfer Case Exploded V iew...
Страница 458: ......
Страница 466: ......
Страница 467: ......
Страница 468: ......