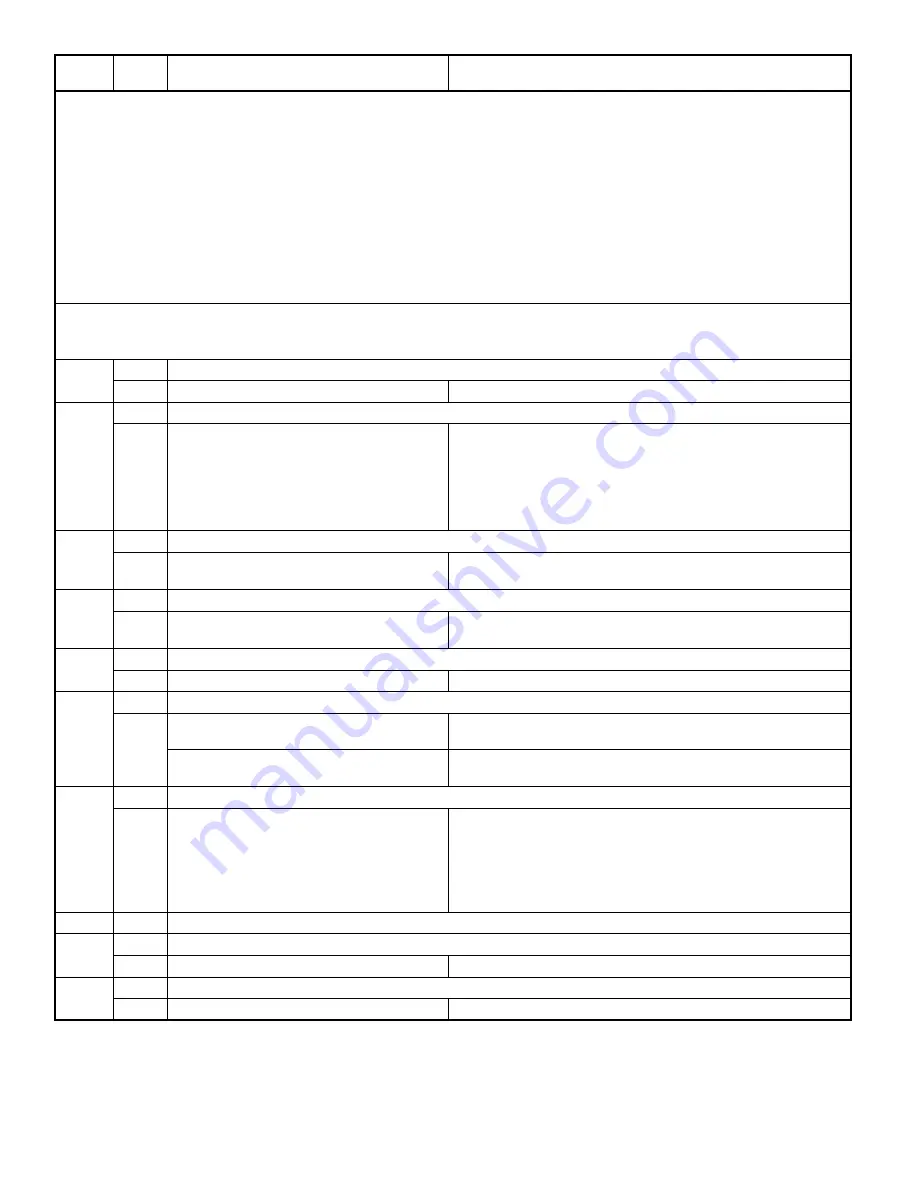
7-12
62-11039
Alarm
NO.
Steps
ALARM / CAUSE
CORRECTIVE ACTION
18
LOW REFRIGERANT PRESSURE
•
TRIGGER–ON (A):
Both UL1 and UL2 are energized AND unit is in engine mode AND in low speed AND compressor is
running AND low suction pressure shutdown delay in configurations has elapsed since energizing UL1
AND Suction Pressure is less than --10 in. Hg (0.3 Bar)
•
UNIT CONTROL: Engine operation: alarm only or (if configured for shutdown) engine and unit shutdown
•
UNIT CONTROL: Engine operation: alarm only or (if configured for shutdown) engine and unit shutdown
and alarm. Standby operation: alarm only or (if configured for shutdown) refrigeration system shutdown
and alarm with PSCON still energized.
•
RESET CONDITION: If alarm only, auto reset when either UL1 or UL2 is de--energized. If unit and
system shut down and alarm, auto reset after 15 minutes. Alarm may be manually reset via keypad or by
turning the unit OFF, then ON again.
NOTE: Follow the steps below until a problem is found. Once a repair or correction has been made, the active alarm
should clear itself (see reset condition above). Operate the unit through the appropriate modes to see if any active
alarm occurs. Continue with the steps below as necessary.
1.
Check Refrigerant Charge
a. Check for undercharged system
Level must be above lower sight glass
2.
Check System Pressures
a. Install Manifold Test Set and check and
compare compressor discharge &
suction pressures with those shown on
the microprocessor controller.
Suction pressure must be above 3 PSIG (0.2 Bar)
Suction & Discharge Pressures must have the same
reading on gauges & on micro display.
NOTE: Microprocessor suction pressure reading has
a maximum value of 100 psig (7.5 bar)
3.
Manually Defrost Unit
a. Defrost
unit
and
terminate
automatically.
Typical defrost cycle time is 5--20 minutes
Suction pressure should rise gradually during cycle.
4.
Perform Pre--Trip Check
a. Run Pre--Trip & check for alarms
Any active alarms must be corrected and cleared before
proceeding.
5.
Check Unloader Operation
a. Check front and rear unloaders
See Alarms 85 and 86
6.
Check CSMV
a. Check compressor suction
modulation valve
See procedure “How To Check CSMV” See Section 8.23
b. Check airflow (with unit running).
Even airflow through the entire coil
No “dead” spots
7.
a. Check evaporator section, return air
bulkhead, air chute, cleanliness of
evap. coil
Good Air Flow
Return air not restricted
Air chute in good condition
No damage to blower wheel
Evap. coil clean
Evap. fan rotation ok
8.
Check Expansion Valve (EVXV)
9.
Check Expansion Valve For Compartment 2
a. Check superheat of valve
Refer to Section 8.18.2
10.
Check Expansion Valve For Compartment 3
a. Check superheat of valve
Refer to Section 2.12
Содержание VECTOR 1800 MT
Страница 1: ......
Страница 2: ...OPERATION SERVICE MANUAL for VECTOR 1800 MT Trailer Multi Temp Refrigeration Units ...
Страница 19: ...1 5 62 11039 1 3 SAFETY DECALS ...
Страница 20: ...1 6 62 11039 62 03958 00 Heat Warning 62 03957 01 High Voltage 62 60280 00 Standby Safety ...
Страница 21: ...1 7 62 11039 ...
Страница 303: ...10 1 62 11039 ...
Страница 310: ...10 8 62 11039 BASED ON ENGINEERING SCHEMATIC 62 60926 REV G NEXT SHT ...
Страница 311: ...10 9 62 11039 FROM PREVIOUS SHT ...