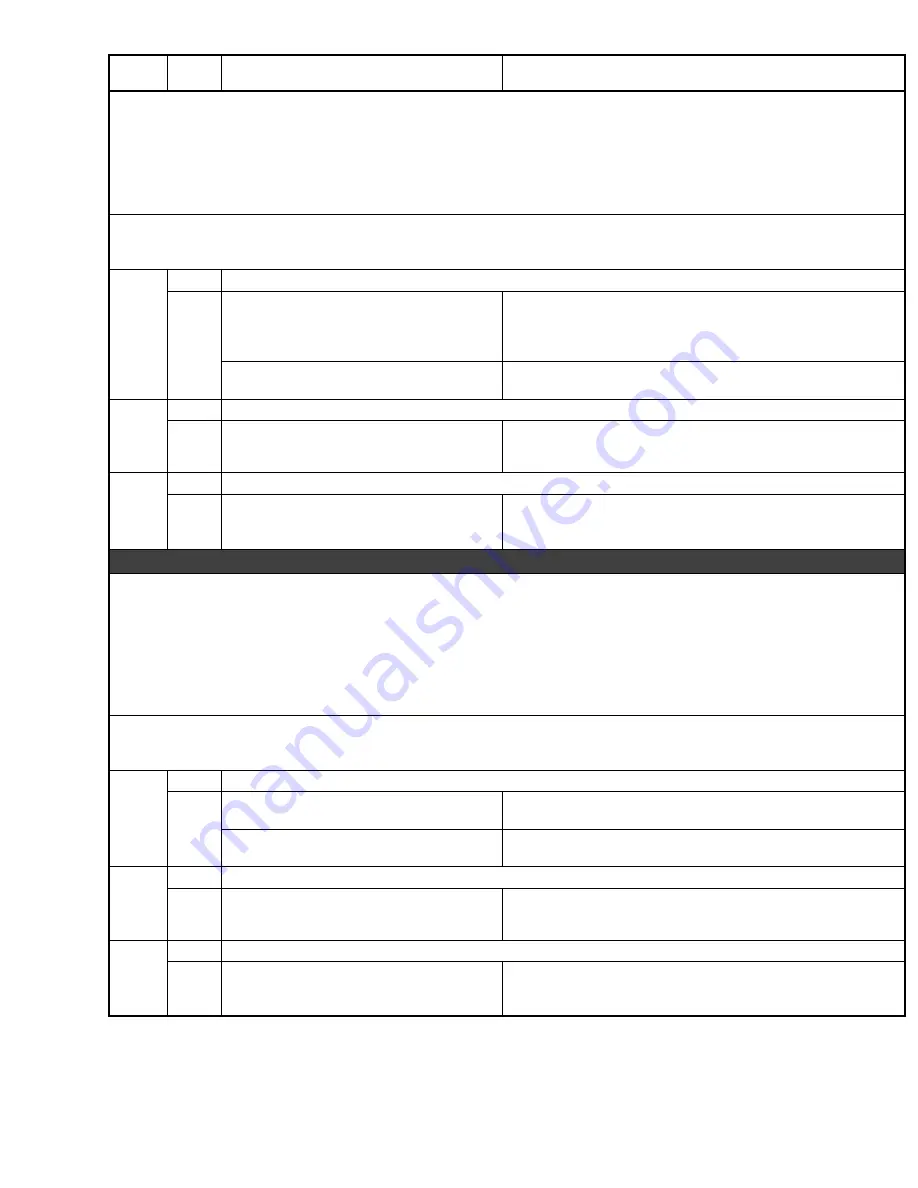
62-11039
7-75
Alarm
NO.
Steps
ALARM / CAUSE
CORRECTIVE ACTION
P153 CHECK RETURN AIR SENSOR
•
TRIGGER–ON: Return Air Sensor is not within the range of --53
°
F to +158
°
F (--47
°
C to +70
°
C)
•
UNIT CONTROL: Engine and standby operation: pre--trip will fail and display “PRE--TRIP FAIL AND
UNIT CONTROL: Engine and standby operation: pre trip will fail and display PRE TRIP FAIL AND
COMPLETED”.
•
RESET CONDITION: Auto Reset if pre--trip mode is started again, or alarm may be manually reset via
keypad or by turning the unit off, then back on again.
NOTE: Follow the steps below until a problem is found. Once a repair or correction has been made, clear the
alarm(s). (See Note 1) Operate the unit through the appropriate modes to see if any active alarm occurs. Continue
with the steps below as necessary.
1.
Check Return Air Sensor
a. Inspect Return Air Sensor & connector No physical damage to harness.
No moisture, damaged or corroded pins
1MP Plug is connected tightly to microprocessor. No wires
are pushed back through plug.
b. Check Return Air Sensor resistance
(See Note 4)
10,000 Ohms @ 77
°
F (25
°
C) [See manual for complete
table of temperatures and resistance values.]
2.
Check Return Air Sensor Wiring
a. Inspect harness & control box
connector pins & terminals (See
wiring schematic)
No physical damage to harness.
No damaged or corroded pins
3.
Check Remote Sensor Connector (2 Compartment Unit Only)
a.Locate and inspect remote sensor
connector
Cap is in place.
No physical damage.
No moisture or corrosion.
P154 CHECK SUPPLY AIR SENSOR
•
TRIGGER–ON: Supply Air Sensor is not within the maximum range of --53
°
F to +158
°
F (--47
°
C to
+70
°
C)
•
UNIT CONTROL: Engine and standby operation: pre trip will fail and display “PRE TRIP FAIL AND
•
UNIT CONTROL: Engine and standby operation: pre--trip will fail and display “PRE--TRIP FAIL AND
COMPLETED”.
•
RESET CONDITION: Auto Reset if pre--trip mode is started again, or alarm may be manually reset via
keypad or by turning the unit off, then back on again.
NOTE: Follow the steps below until a problem is found. Once a repair or correction has been made, clear the
alarm(s). (See Note 1) Operate the unit through the appropriate modes to see if any active alarm occurs. Continue
with the steps below as necessary.
1.
Check Supply Air Sensor
a. Inspect Supply Air Sensor & connector No physical damage to harness.
No moisture, damaged or corroded pins
b. Check Supply Air Sensor resistance
(See Note 4)
10,000 Ohms @ 77
°
F (25
°
C) [See manual for complete
table of temperatures and resistance values.]
2.
Check Supply Air Sensor Wiring
a. Inspect harness & control box
connector pins & terminals (See
wiring schematic)
No physical damage to harness.
No damaged or corroded pins
3.
Check Supply Sensor Connector
a.Locate and inspect remote sensor
connector
Cap is in place.
No physical damage.
No moisture or corrosion.
Содержание VECTOR 1800 MT
Страница 1: ......
Страница 2: ...OPERATION SERVICE MANUAL for VECTOR 1800 MT Trailer Multi Temp Refrigeration Units ...
Страница 19: ...1 5 62 11039 1 3 SAFETY DECALS ...
Страница 20: ...1 6 62 11039 62 03958 00 Heat Warning 62 03957 01 High Voltage 62 60280 00 Standby Safety ...
Страница 21: ...1 7 62 11039 ...
Страница 303: ...10 1 62 11039 ...
Страница 310: ...10 8 62 11039 BASED ON ENGINEERING SCHEMATIC 62 60926 REV G NEXT SHT ...
Страница 311: ...10 9 62 11039 FROM PREVIOUS SHT ...