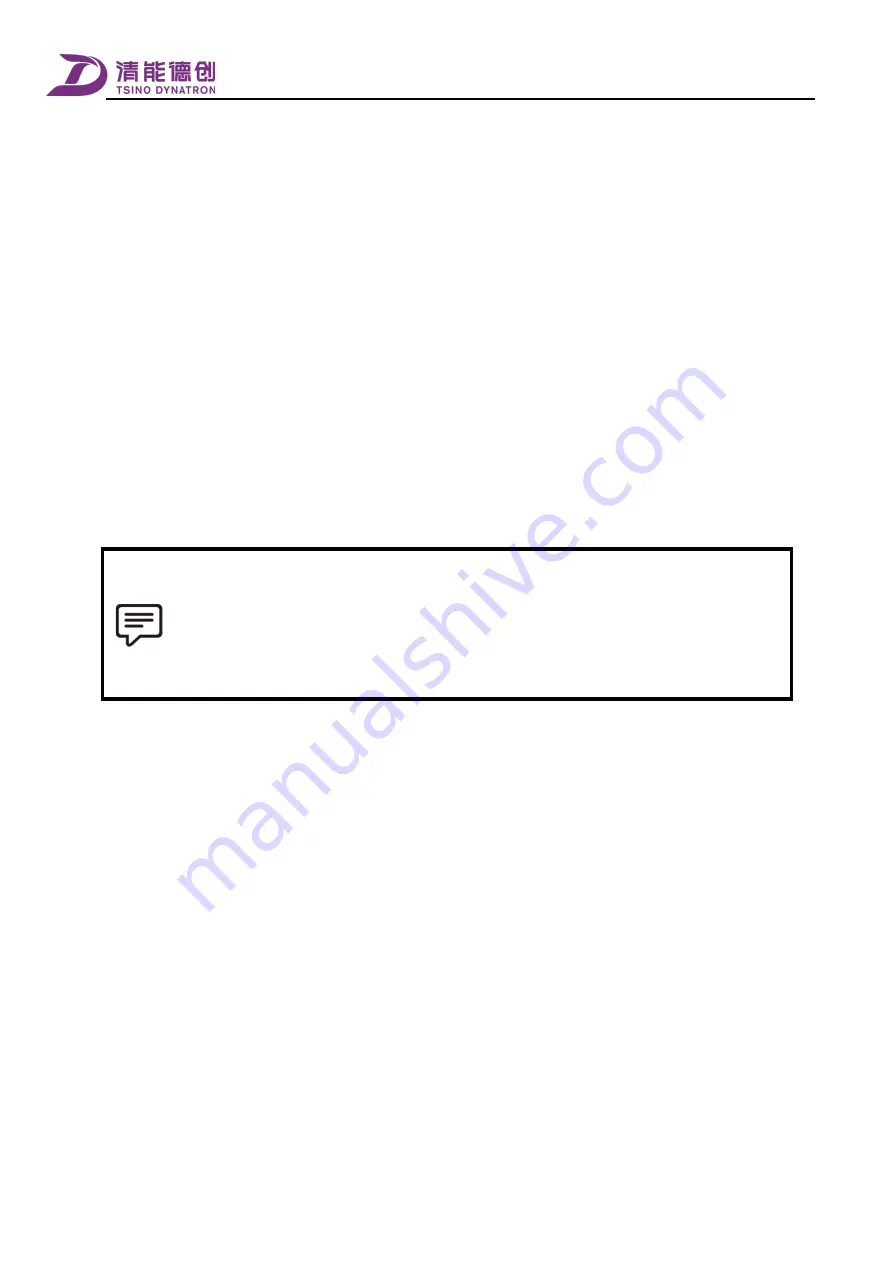
Adjustment
149
The smaller the set value of velocity loop integration time constant, the stronger the integration and the better the
response to the velocity commands. However, a small set value can cause mechanical vibration and noise. Increasing
the velocity loop integration time can reduce the overshoot of response, but a too high value might slow down the
system response.
Increasing the torque command low pass filter cutoff frequency can improve system response, while decreasing the
value can prevent vibration or overshoot.
4.
The usual sequence of adjusting parameters is as follows.
To improve system response
1)
Increase the torque command lowpass filter cutoff frequency
2)
Increase the
Velocity Loop Proportional Gain
3)
Decrease the velocity loop integration time constant
4)
Increase Position Loop Proportional Gain
To slow down system response to prevent vibration and overshoot
1)
Decrease the Position Loop Proportional Gain
2)
Increase the velocity loop integration time constant
3)
Decrease the Velocity Loop Proportional Gain
4)
Decrease the torque command lowpass filter cutoff frequency
1.
If the system vibrates while increasing the velocity loop or position loop gain, the gain shall not be
increased further.
2.
Response is the result of all parameters acting together, and when one parameter changes
significantly, other parameters usually need to be adjusted as well.
3. The current loop parameters are only related to the motor parameters, and it is usually unnecessary to
adjust them after the initial use of the configuration.
Summary of Contents for CoolDrive Series
Page 29: ...Preface 17 T2 model ...
Page 30: ...Preface 18 T3 model ...
Page 31: ...Preface 19 T4 model ...
Page 230: ...Monitoring 218 ...