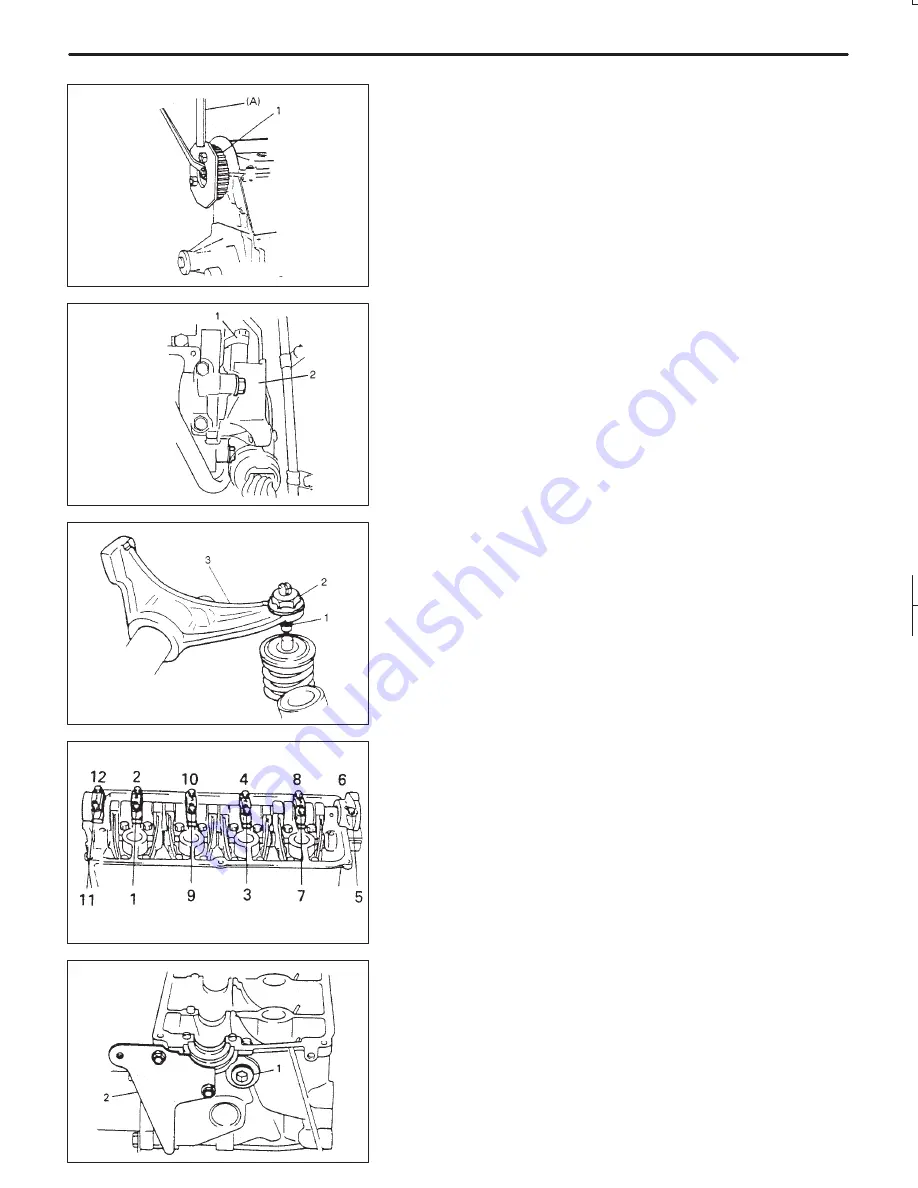
YH4
GRAND
VITARA
1. Camshaft pulley
1. CMP sensor
2. CMP sensor case
1. Valve adjusting screw
2. Lock nut
3. Rocker arm
1. Oil plug
2. Timing belt
inside cover
ENGINE MECHANICAL (G16 ENGINE)
6A1-33
5) Remove camshaft timing belt pulley by using special tool.
Special Tool
(A): 09917-68220
6) Remove cylinder head cover as previously outlined.
7) Disconnect CMP sensor connector and remove CMP sensor
case from cylinder head.
Place a container or rag under CMP sensor case, for a small
amount of oil flows out during removal of case.
8) After loosening all valve adjusting screw lock nuts, turn adjust-
ing screws back all the way to allow all rocker arms to move
freely.
9) Remove camshaft housing and camshaft.
NOTE:
To remove camshaft housing bolts, loosen them in such
order as indicated in figure, a little at a time.
10) Remove rocker arm shaft plug and timing belt inside cover.
Summary of Contents for 2000 Grand Vitara SQ416
Page 75: ...ENGINE DIAGNOSIS G16 J20 ENGINES 6 71 Fig 1 for Step 3...
Page 179: ...6 1 68 ENGINE H25 ENGINE a Fig for STEP 2 3 a HO2S heater relay...
Page 190: ...ENGINE H25 ENGINE 6 1 79 a Fig for STEP 2 3 a HO2S heater relay...
Page 541: ...6E1 4 ENGINE AND EMISSION CONTROL SYSTEM G16 J20 ENGINES G16 ENGINE...
Page 542: ...ENGINE AND EMISSION CONTROL SYSTEM G16 J20 ENGINES 6E1 5...
Page 543: ...6E1 6 ENGINE AND EMISSION CONTROL SYSTEM G16 J20 ENGINES J20 ENGINE...
Page 544: ...ENGINE AND EMISSION CONTROL SYSTEM G16 J20 ENGINES 6E1 7...
Page 552: ...ENGINE AND EMISSION CONTROL SYSTEM G16 J20 ENGINES 6E1 15...
Page 592: ...6E2 4 ENGINE AND EMISSION CONTROL SYSTEM H25 ENGINE...
Page 593: ...ENGINE AND EMISSION CONTROL SYSTEM H25 ENGINE 6E2 5...
Page 597: ...ENGINE AND EMISSION CONTROL SYSTEM H25 ENGINE 6E2 9...
Page 723: ...6H 30 CHARGING SYSTEM 17 Make sure that rotor turns smoothly...