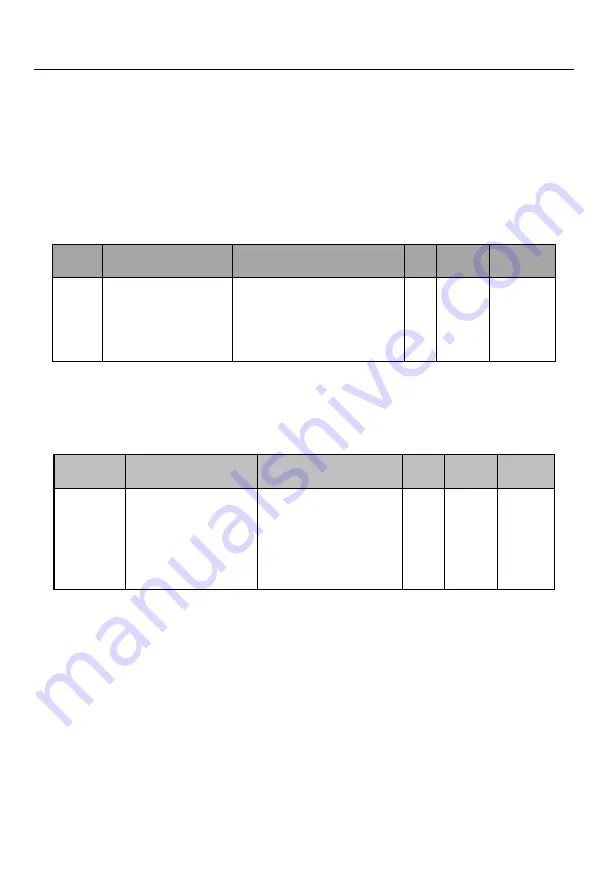
User Manual of EM730/EM730E Series Inverter
235
F10.05=1: enable the master-slave communication function;
F10.06=0: select the current inverter as the slave;
Select one setting as the communication setting. If F09.00=6 is set and the process PID is
set separately (F00.05=10, F00.06=1), the slave inverter will be set to the host output
current for PID adjustment.
You can set the receiving proportional coefficient (F10.08) to determine how the slave
inverter receives data. If F10.08=0.80 is set, the final application data is “Recv (received data) *
0.80 (F10.08)”.
Functio
n code
Function code name
Parameter description
Unit
Default
setting
Attribute
F10.56
Options of 485
EEPROM writing
0-10: default operation (for
commissioning)
11: writing not triggered
(available after
commissioning)
0
〇
For the application “PLC controller/HMI + inverter”, you can set F10.56=11 after
debugging. Then all write data of PLC communication will not be stored, which can avoid
damage to the memory.
If you need parameter settings and power-down storage, set F10.56=0 first.
Function
code
Function code name
Parameter description
Unit
Default
setting
Attribute
F10.59
SCI response option
0: Reply to both read and
write commands
1: Reply to write
commands only
2: No reply to both read
and write commands
0
〇
F10.59=0: During the Modbus communication with the upper computer, both read and
write parameters will be returned to the upper computer.
F10.59=1: During the Modbus communication with the upper computer, the read
parameters will be returned to the upper computer, while the write parameters will not.
F10.59=2: During the Modbus communication with the upper computer, both read and
write parameters will not be returned to the upper computer. This can improve the
communication efficiency.